Filter News
Area of Research
- Advanced Manufacturing (12)
- Biological Systems (1)
- Biology and Environment (14)
- Clean Energy (50)
- Computational Biology (1)
- Computational Engineering (1)
- Computer Science (8)
- Fusion and Fission (3)
- Fusion Energy (1)
- Materials (20)
- Materials for Computing (7)
- National Security (3)
- Neutron Science (34)
- Quantum information Science (6)
- Supercomputing (22)
News Topics
- (-) 3-D Printing/Advanced Manufacturing (41)
- (-) Big Data (12)
- (-) Bioenergy (22)
- (-) Frontier (6)
- (-) Machine Learning (6)
- (-) Neutron Science (36)
- (-) Quantum Science (22)
- Advanced Reactors (9)
- Artificial Intelligence (19)
- Biology (23)
- Biomedical (15)
- Biotechnology (6)
- Buildings (13)
- Chemical Sciences (7)
- Clean Water (13)
- Climate Change (11)
- Composites (8)
- Computer Science (65)
- Coronavirus (10)
- Critical Materials (4)
- Cybersecurity (10)
- Decarbonization (7)
- Energy Storage (30)
- Environment (58)
- Exascale Computing (4)
- Fusion (13)
- Grid (16)
- High-Performance Computing (19)
- Isotopes (13)
- ITER (4)
- Materials (32)
- Materials Science (42)
- Mathematics (1)
- Mercury (4)
- Microscopy (15)
- Molten Salt (1)
- Nanotechnology (16)
- National Security (7)
- Net Zero (1)
- Nuclear Energy (23)
- Physics (9)
- Polymers (7)
- Quantum Computing (5)
- Security (5)
- Space Exploration (8)
- Statistics (1)
- Summit (18)
- Sustainable Energy (43)
- Transportation (33)
Media Contacts
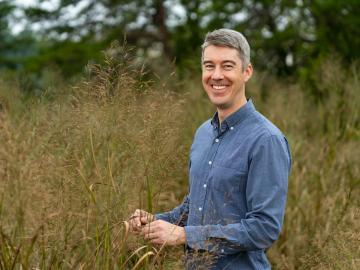
For ORNL environmental scientist and lover of the outdoors John Field, work in ecosystem modeling is a profession with tangible impacts.
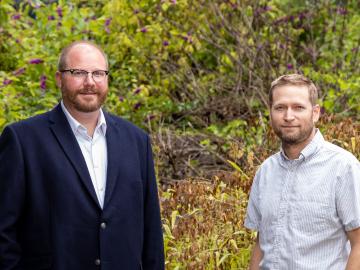
Of the $61 million recently announced by the U.S. Department of Energy for quantum information science studies, $17.5 million will fund research at DOE’s Oak Ridge National Laboratory. These projects will help build the foundation for the quantum internet, advance quantum entanglement capabilities — which involve sharing information through paired particles of light called photons — and develop next-generation quantum sensors.
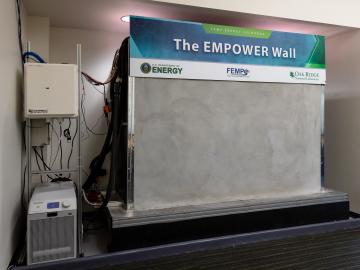
Oak Ridge National Laboratory researchers demonstrated that cooling cost savings could be achieved with a 3D printed concrete smart wall following a three-month field test.

A new tool that simulates the energy profile of every building in America will give homeowners, utilities and companies a quick way to determine energy use and cost-effective retrofits that can reduce energy and carbon emissions.
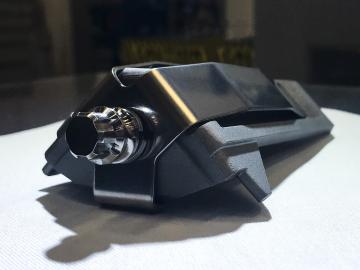
Four first-of-a-kind 3D-printed fuel assembly brackets, produced at the Department of Energy’s Manufacturing Demonstration Facility at Oak Ridge National Laboratory, have been installed and are now under routine operating
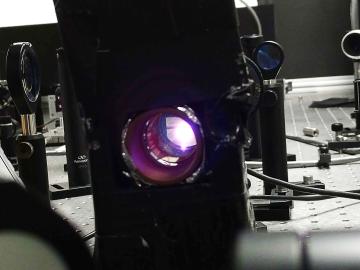
To minimize potential damage from underground oil and gas leaks, Oak Ridge National Laboratory is co-developing a quantum sensing system to detect pipeline leaks more quickly.

A research team at Oak Ridge National Laboratory have 3D printed a thermal protection shield, or TPS, for a capsule that will launch with the Cygnus cargo spacecraft as part of the supply mission to the International Space Station.
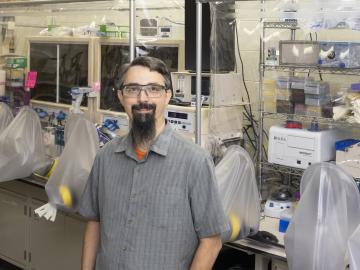
As a metabolic engineer at Oak Ridge National Laboratory, Adam Guss modifies microbes to perform the diverse processes needed to make sustainable biofuels and bioproducts.
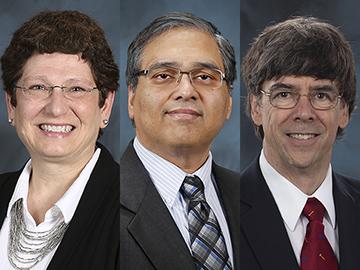
ASM International recently elected three researchers from ORNL as 2021 fellows. Selected were Beth Armstrong and Govindarajan Muralidharan, both from ORNL’s Material Sciences and Technology Division, and Andrew Payzant from the Neutron Scattering Division.

Scientists at ORNL and the University of Tennessee, Knoxville, have found a way to simultaneously increase the strength and ductility of an alloy by introducing tiny precipitates into its matrix and tuning their size and spacing.