
Filter News
Area of Research
- Advanced Manufacturing (4)
- Biological Systems (2)
- Biology and Environment (121)
- Biology and Soft Matter (1)
- Clean Energy (130)
- Climate and Environmental Systems (5)
- Computational Engineering (1)
- Computer Science (4)
- Electricity and Smart Grid (3)
- Functional Materials for Energy (1)
- Fusion and Fission (7)
- Isotopes (1)
- Materials (36)
- Materials for Computing (3)
- Mathematics (1)
- National Security (31)
- Neutron Science (13)
- Nuclear Science and Technology (7)
- Quantum information Science (3)
- Sensors and Controls (1)
- Supercomputing (46)
News Topics
- (-) Bioenergy (91)
- (-) Composites (26)
- (-) Cybersecurity (35)
- (-) Environment (194)
- (-) Grid (62)
- (-) Mercury (12)
- (-) Molten Salt (8)
- (-) Simulation (47)
- 3-D Printing/Advanced Manufacturing (119)
- Advanced Reactors (34)
- Artificial Intelligence (91)
- Big Data (53)
- Biology (98)
- Biomedical (58)
- Biotechnology (22)
- Buildings (57)
- Chemical Sciences (63)
- Clean Water (29)
- Climate Change (99)
- Computer Science (187)
- Coronavirus (46)
- Critical Materials (25)
- Decarbonization (79)
- Education (4)
- Element Discovery (1)
- Emergency (2)
- Energy Storage (108)
- Exascale Computing (37)
- Fossil Energy (5)
- Frontier (42)
- Fusion (53)
- High-Performance Computing (84)
- Hydropower (11)
- Irradiation (3)
- Isotopes (53)
- ITER (7)
- Machine Learning (47)
- Materials (143)
- Materials Science (139)
- Mathematics (7)
- Microelectronics (2)
- Microscopy (51)
- Nanotechnology (60)
- National Security (60)
- Net Zero (13)
- Neutron Science (131)
- Nuclear Energy (106)
- Partnerships (43)
- Physics (61)
- Polymers (33)
- Quantum Computing (34)
- Quantum Science (69)
- Renewable Energy (2)
- Security (24)
- Software (1)
- Space Exploration (25)
- Statistics (3)
- Summit (57)
- Sustainable Energy (125)
- Transformational Challenge Reactor (7)
- Transportation (97)
Media Contacts
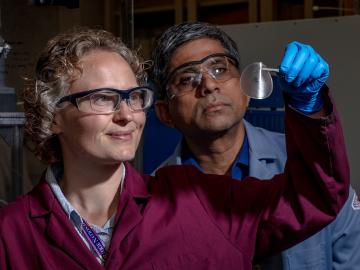
Oak Ridge National Laboratory scientists have developed a crucial component for a new kind of low-cost stationary battery system utilizing common materials and designed for grid-scale electricity storage. Large, economical electricity storage systems can benefit the nation’s grid ...
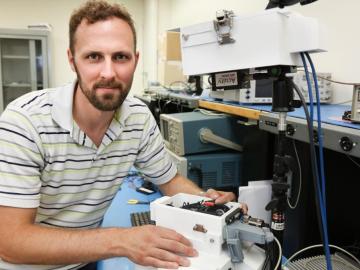
As leader of the RF, Communications, and Cyber-Physical Security Group at Oak Ridge National Laboratory, Kerekes heads an accelerated lab-directed research program to build virtual models of critical infrastructure systems like the power grid that can be used to develop ways to detect and repel cyber-intrusion and to make the network resilient when disruption occurs.
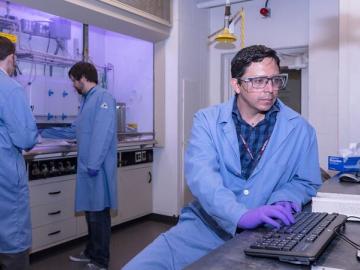
Oak Ridge National Laboratory has developed a salt purification lab to study the viability of using liquid salt that contains lithium fluoride and beryllium fluoride, known as FLiBe, to cool molten salt reactors, or MSRs. Multiple American companies developing advanced reactor technol...
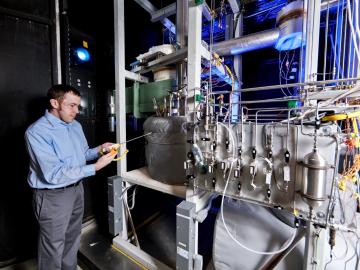
Thanks in large part to developing and operating a facility for testing molten salt reactor (MSR) technologies, nuclear experts at the Energy Department’s Oak Ridge National Laboratory (ORNL) are now tackling the next generation of another type of clean energy—concentrating ...
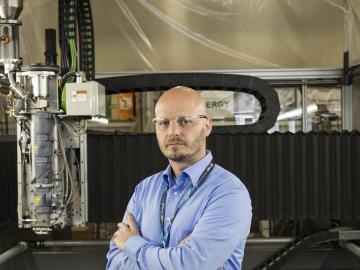
Vlastimil Kunc grew up in a family of scientists where his natural curiosity was encouraged—an experience that continues to drive his research today in polymer composite additive manufacturing at Oak Ridge National Laboratory. “I’ve been interested in the science of composites si...
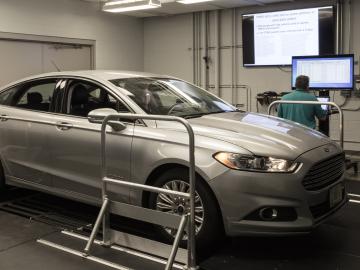
A new Oak Ridge National Laboratory-developed method promises to protect connected and autonomous vehicles from possible network intrusion. Researchers built a prototype plug-in device designed to alert drivers of vehicle cyberattacks. The prototype is coded to learn regular timing...

With the licensing to Enchi Corporation of a microbe custom-designed to produce ethanol efficiently, Oak Ridge National Laboratory (ORNL) and the BioEnergy Science Center (BESC) mark the culmination of 10 years’ research into ways to improve biofuels production. Enchi ha...
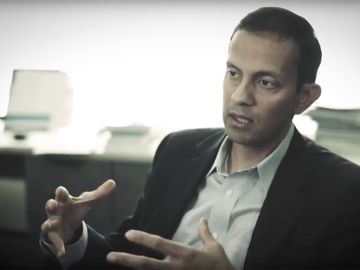
The field of “Big Data” has exploded in the blink of an eye, growing exponentially into almost every branch of science in just a few decades. Sectors such as energy, manufacturing, healthcare and many others depend on scalable data processing and analysis for continued in...

The Department of Energy has announced funding for new research centers to accelerate the development of specialty plants and processes for a new generation of biofuels and bioproducts. The Center for Bioenergy Innovation (CBI), led by Oak Ridge National Laboratory...
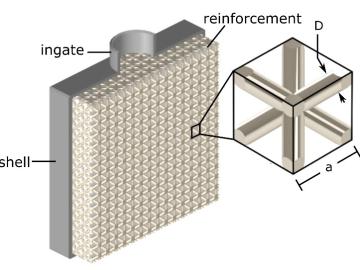
A new manufacturing method created by Oak Ridge National Laboratory and Rice University combines 3D printing with traditional casting to produce damage-tolerant components composed of multiple materials. Composite components made by pouring an aluminum alloy over a printed steel lattice showed an order of magnitude greater damage tolerance than aluminum alone.