
Filter News
Area of Research
- (-) Fusion and Fission (8)
- (-) Materials (62)
- Advanced Manufacturing (24)
- Biology and Environment (144)
- Biology and Soft Matter (1)
- Building Technologies (3)
- Clean Energy (183)
- Climate and Environmental Systems (5)
- Computational Biology (2)
- Computational Engineering (1)
- Computer Science (3)
- Electricity and Smart Grid (1)
- Energy Sciences (1)
- Functional Materials for Energy (1)
- Fusion Energy (3)
- Isotopes (1)
- Materials for Computing (11)
- Mathematics (1)
- National Security (13)
- Neutron Science (22)
- Nuclear Science and Technology (6)
- Quantum information Science (1)
- Supercomputing (42)
News Topics
- (-) 3-D Printing/Advanced Manufacturing (26)
- (-) Biology (5)
- (-) Clean Water (3)
- (-) Environment (17)
- (-) Net Zero (2)
- (-) Polymers (17)
- (-) Sustainable Energy (17)
- Advanced Reactors (10)
- Artificial Intelligence (10)
- Big Data (2)
- Bioenergy (11)
- Biomedical (8)
- Buildings (5)
- Chemical Sciences (34)
- Climate Change (5)
- Composites (9)
- Computer Science (19)
- Coronavirus (4)
- Critical Materials (13)
- Cybersecurity (4)
- Decarbonization (9)
- Energy Storage (35)
- Exascale Computing (3)
- Fossil Energy (1)
- Frontier (4)
- Fusion (27)
- Grid (6)
- High-Performance Computing (6)
- Irradiation (1)
- Isotopes (14)
- ITER (6)
- Machine Learning (5)
- Materials (74)
- Materials Science (80)
- Mathematics (1)
- Microscopy (27)
- Molten Salt (3)
- Nanotechnology (39)
- National Security (3)
- Neutron Science (34)
- Nuclear Energy (42)
- Partnerships (13)
- Physics (30)
- Quantum Computing (3)
- Quantum Science (11)
- Renewable Energy (1)
- Security (4)
- Simulation (4)
- Space Exploration (3)
- Summit (2)
- Transformational Challenge Reactor (3)
- Transportation (16)
Media Contacts
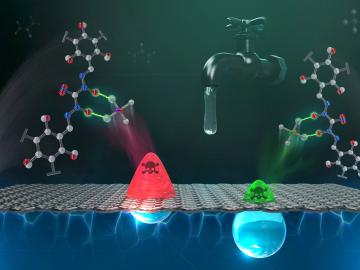
Researchers at ORNL are tackling a global water challenge with a unique material designed to target not one, but two toxic, heavy metal pollutants for simultaneous removal.
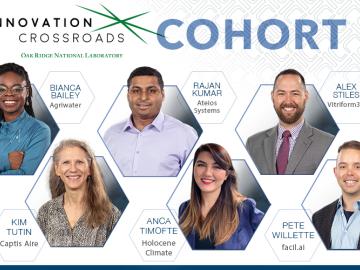
Oak Ridge National Laboratory’s Innovation Crossroads program welcomes six new science and technology innovators from across the United States to the sixth cohort.
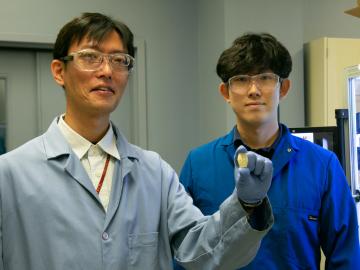
ORNL researchers have developed an upcycling approach that adds value to discarded plastics for reuse in additive manufacturing, or 3D printing.
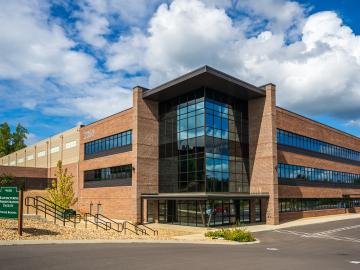
ORNL scientists will present new technologies available for licensing during the annual Technology Innovation Showcase. The event is 9 a.m. to 3 p.m. Thursday, June 16, at the Manufacturing Demonstration Facility at ORNL’s Hardin Valley campus.
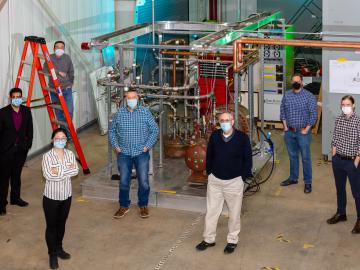
To achieve practical energy from fusion, extreme heat from the fusion system “blanket” component must be extracted safely and efficiently. ORNL fusion experts are exploring how tiny 3D-printed obstacles placed inside the narrow pipes of a custom-made cooling system could be a solution for removing heat from the blanket.
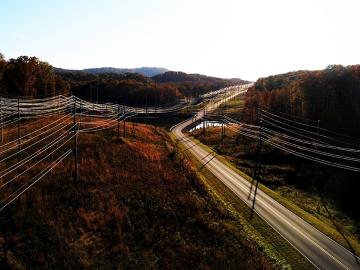
ORNL and the Tennessee Valley Authority, or TVA, are joining forces to advance decarbonization technologies from discovery through deployment through a new memorandum of understanding, or MOU.
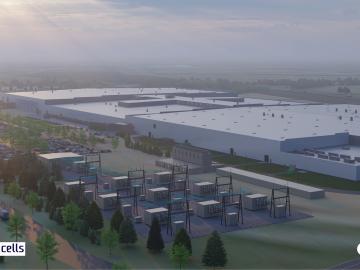
ORNL, TVA and TNECD were recognized by the Federal Laboratory Consortium for their impactful partnership that resulted in a record $2.3 billion investment by Ultium Cells, a General Motors and LG Energy Solution joint venture, to build a battery cell manufacturing plant in Spring Hill, Tennessee.

Ten scientists from the Department of Energy’s Oak Ridge National Laboratory are among the world’s most highly cited researchers, according to a bibliometric analysis conducted by the scientific publication analytics firm Clarivate.

Amy Elliott, a group leader for robotics and intelligent systems at Oak Ridge National Laboratory, has received the 2021 ASTM International Additive Manufacturing Young Professional Award for her early career research contributions
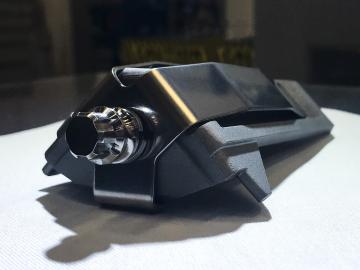
Four first-of-a-kind 3D-printed fuel assembly brackets, produced at the Department of Energy’s Manufacturing Demonstration Facility at Oak Ridge National Laboratory, have been installed and are now under routine operating