Filter News
Area of Research
- (-) Clean Energy (34)
- (-) Isotopes (3)
- (-) Neutron Science (4)
- Advanced Manufacturing (11)
- Biology and Environment (2)
- Building Technologies (1)
- Fusion Energy (3)
- Materials (29)
- Materials for Computing (7)
- National Security (1)
- Nuclear Science and Technology (3)
- Quantum information Science (1)
- Supercomputing (4)
- Transportation Systems (1)
News Topics
- (-) 3-D Printing/Advanced Manufacturing (23)
- (-) Isotopes (3)
- (-) Materials Science (12)
- (-) Microscopy (3)
- (-) Polymers (5)
- (-) Space Exploration (4)
- Artificial Intelligence (2)
- Big Data (1)
- Bioenergy (3)
- Biology (2)
- Biomedical (4)
- Biotechnology (1)
- Buildings (13)
- Chemical Sciences (2)
- Clean Water (4)
- Climate Change (6)
- Composites (9)
- Computer Science (9)
- Coronavirus (2)
- Critical Materials (4)
- Decarbonization (4)
- Energy Storage (24)
- Environment (16)
- Grid (15)
- High-Performance Computing (1)
- Hydropower (2)
- Irradiation (1)
- Machine Learning (2)
- Materials (16)
- Mathematics (1)
- Mercury (1)
- Nanotechnology (2)
- Net Zero (1)
- Neutron Science (23)
- Nuclear Energy (2)
- Physics (1)
- Quantum Science (1)
- Simulation (1)
- Statistics (1)
- Sustainable Energy (27)
- Transportation (27)
Media Contacts
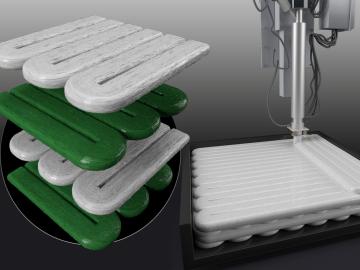
Oak Ridge National Laboratory researchers combined additive manufacturing with conventional compression molding to produce high-performance thermoplastic composites reinforced with short carbon fibers.

A team of Oak Ridge National Laboratory researchers demonstrated that an additively manufactured hot stamping die – a tool used to create car body components – cooled faster than those produced by conventional manufacturing methods.

Oak Ridge National Laboratory researchers have demonstrated that a new class of superalloys made of cobalt and nickel remains crack-free and defect-resistant in extreme heat, making them conducive for use in metal-based 3D printing applications.
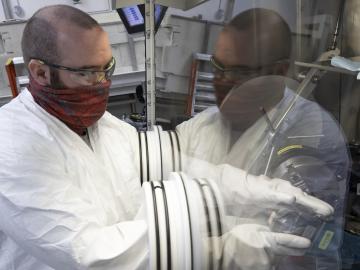
A better way of welding targets for Oak Ridge National Laboratory’s plutonium-238 production has sped up the process and improved consistency and efficiency. This advancement will ultimately benefit the lab’s goal to make enough Pu-238 – the isotope that powers NASA’s deep space missions – to yield 1.5 kilograms of plutonium oxide annually by 2026.

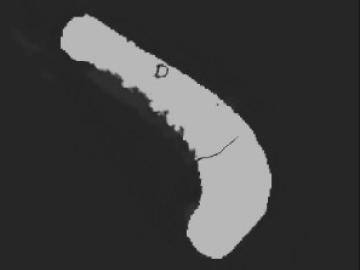
Algorithms developed at Oak Ridge National Laboratory can greatly enhance X-ray computed tomography images of 3D-printed metal parts, resulting in more accurate, faster scans.
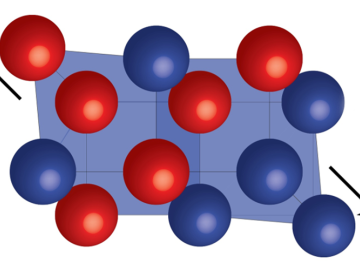
Pauling’s Rules is the standard model used to describe atomic arrangements in ordered materials. Neutron scattering experiments at Oak Ridge National Laboratory confirmed this approach can also be used to describe highly disordered materials.
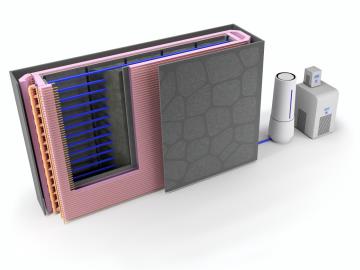
Oak Ridge National Laboratory researchers used additive manufacturing to build a first-of-its kind smart wall called EMPOWER.
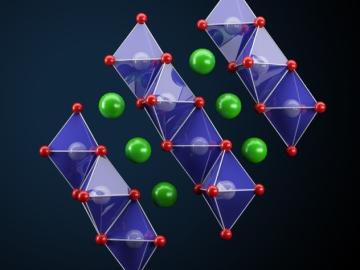
Oak Ridge National Laboratory scientists seeking the source of charge loss in lithium-ion batteries demonstrated that coupling a thin-film cathode with a solid electrolyte is a rapid way to determine the root cause.
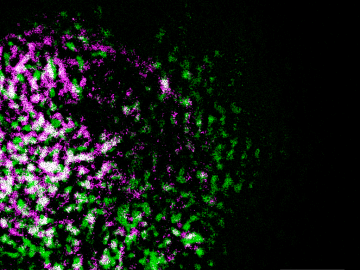
Oak Ridge National Laboratory researchers have built a novel microscope that provides a “chemical lens” for viewing biological systems including cell membranes and biofilms.