Filter News
Area of Research
- (-) Climate and Environmental Systems (1)
- (-) Materials (33)
- Advanced Manufacturing (14)
- Biological Systems (2)
- Biology and Environment (74)
- Building Technologies (1)
- Clean Energy (91)
- Computational Biology (2)
- Computer Science (2)
- Electricity and Smart Grid (2)
- Fusion and Fission (5)
- Fusion Energy (2)
- Materials for Computing (7)
- National Security (10)
- Neutron Science (10)
- Nuclear Science and Technology (6)
- Quantum information Science (3)
- Sensors and Controls (1)
- Supercomputing (31)
News Type
News Topics
- (-) 3-D Printing/Advanced Manufacturing (10)
- (-) Bioenergy (3)
- (-) Biology (1)
- (-) Composites (6)
- (-) Grid (2)
- (-) Molten Salt (1)
- (-) Nanotechnology (16)
- Advanced Reactors (2)
- Artificial Intelligence (4)
- Big Data (2)
- Biomedical (4)
- Buildings (2)
- Chemical Sciences (11)
- Clean Water (3)
- Climate Change (2)
- Computer Science (10)
- Coronavirus (2)
- Critical Materials (5)
- Cybersecurity (1)
- Decarbonization (2)
- Energy Storage (13)
- Environment (11)
- Exascale Computing (1)
- Fusion (4)
- High-Performance Computing (1)
- Isotopes (8)
- Machine Learning (2)
- Materials (31)
- Materials Science (36)
- Mathematics (1)
- Microscopy (12)
- Neutron Science (13)
- Nuclear Energy (12)
- Partnerships (3)
- Physics (13)
- Polymers (10)
- Quantum Computing (2)
- Quantum Science (1)
- Security (1)
- Space Exploration (2)
- Summit (1)
- Sustainable Energy (5)
- Transformational Challenge Reactor (2)
- Transportation (10)
Media Contacts
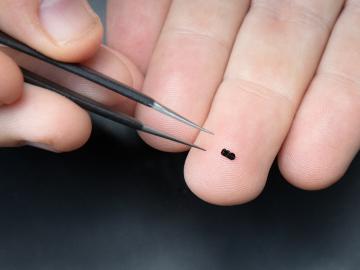
Liam Collins was drawn to study physics to understand “hidden things” and honed his expertise in microscopy so that he could bring them to light.
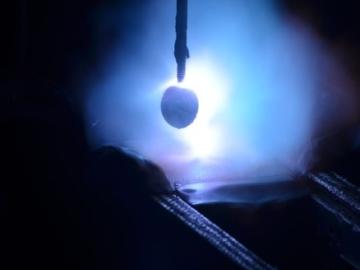
Researchers at Oak Ridge National Laboratory demonstrated that an additively manufactured polymer layer, when applied to carbon fiber reinforced plastic, or CFRP, can serve as an effective protector against aircraft lightning strikes.
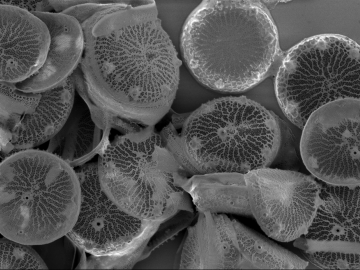
Students often participate in internships and receive formal training in their chosen career fields during college, but some pursue professional development opportunities even earlier.
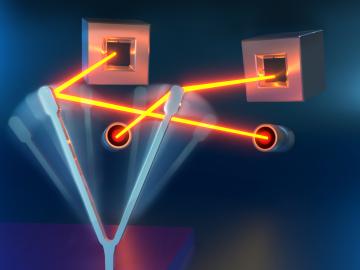
Researchers at ORNL and the National Renewable Energy Laboratory took inspiration from flying insects to demonstrate a miniaturized gyroscope, a special sensor used in navigation technologies.
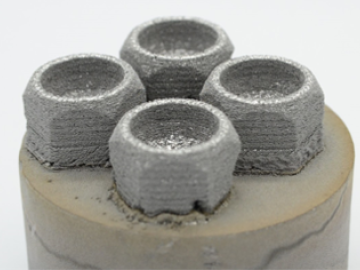
Using additive manufacturing, scientists experimenting with tungsten at Oak Ridge National Laboratory hope to unlock new potential of the high-performance heat-transferring material used to protect components from the plasma inside a fusion reactor. Fusion requires hydrogen isotopes to reach millions of degrees.
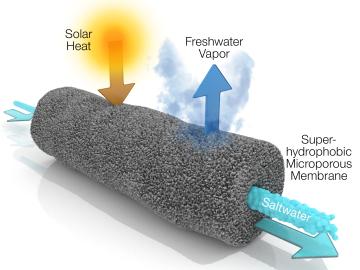
A new method developed at Oak Ridge National Laboratory improves the energy efficiency of a desalination process known as solar-thermal evaporation.
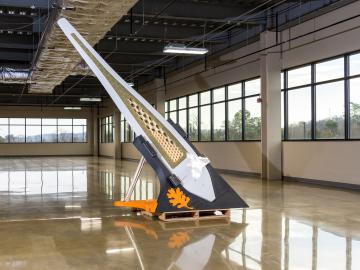
In the shifting landscape of global manufacturing, American ingenuity is once again giving U.S companies an edge with radical productivity improvements as a result of advanced materials and robotic systems developed at the Department of Energy’s Manufacturing Demonstration Facility (MDF) at Oak Ridge National Laboratory.
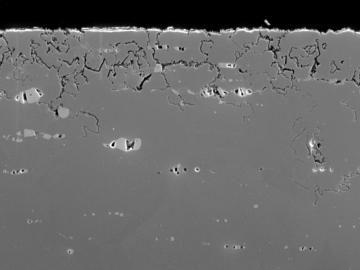
Oak Ridge National Laboratory scientists analyzed more than 50 years of data showing puzzlingly inconsistent trends about corrosion of structural alloys in molten salts and found one factor mattered most—salt purity.
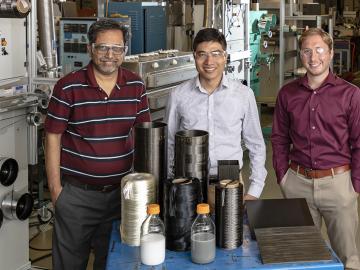
Carbon fiber composites—lightweight and strong—are great structural materials for automobiles, aircraft and other transportation vehicles. They consist of a polymer matrix, such as epoxy, into which reinforcing carbon fibers have been embedded. Because of differences in the mecha...
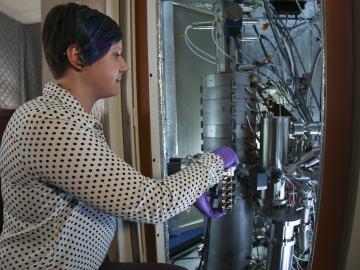
An Oak Ridge National Laboratory-led team used a scanning transmission electron microscope to selectively position single atoms below a crystal’s surface for the first time.