Filter News
Area of Research
- (-) Fusion and Fission (6)
- (-) Materials (19)
- Advanced Manufacturing (3)
- Biology and Environment (68)
- Biology and Soft Matter (1)
- Clean Energy (52)
- Climate and Environmental Systems (2)
- Fusion Energy (1)
- Isotopes (16)
- Materials for Computing (1)
- National Security (14)
- Neutron Science (7)
- Nuclear Science and Technology (5)
- Quantum information Science (1)
- Supercomputing (33)
News Topics
- (-) 3-D Printing/Advanced Manufacturing (7)
- (-) Cybersecurity (1)
- (-) Environment (8)
- (-) Frontier (1)
- (-) Isotopes (6)
- (-) Space Exploration (1)
- (-) Sustainable Energy (5)
- Advanced Reactors (3)
- Artificial Intelligence (5)
- Big Data (2)
- Bioenergy (2)
- Biomedical (2)
- Buildings (1)
- Chemical Sciences (8)
- Clean Water (2)
- Composites (2)
- Computer Science (9)
- Coronavirus (1)
- Decarbonization (2)
- Energy Storage (7)
- Exascale Computing (2)
- Fusion (14)
- Grid (2)
- High-Performance Computing (3)
- ITER (2)
- Machine Learning (2)
- Materials (19)
- Materials Science (17)
- Mathematics (1)
- Microscopy (6)
- Nanotechnology (8)
- Net Zero (1)
- Neutron Science (9)
- Nuclear Energy (26)
- Partnerships (3)
- Physics (12)
- Polymers (4)
- Quantum Computing (1)
- Security (2)
- Simulation (2)
- Summit (1)
- Transformational Challenge Reactor (2)
- Transportation (5)
Media Contacts
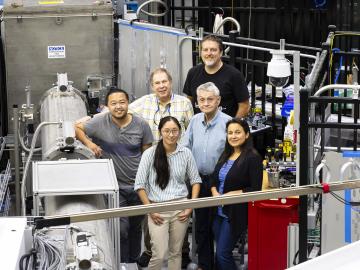
In response to a renewed international interest in molten salt reactors, researchers from the Department of Energy’s Oak Ridge National Laboratory have developed a novel technique to visualize molten salt intrusion in graphite.
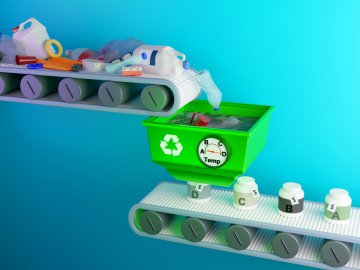
Little of the mixed consumer plastics thrown away or placed in recycle bins actually ends up being recycled. Nearly 90% is buried in landfills or incinerated at commercial facilities that generate greenhouse gases and airborne toxins. Neither outcome is ideal for the environment.
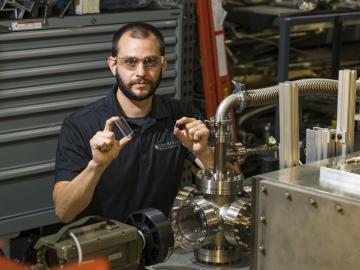
ORNL will team up with six of eight companies that are advancing designs and research and development for fusion power plants with the mission to achieve a pilot-scale demonstration of fusion within a decade.

As renewable sources of energy such as wind and sun power are being increasingly added to the country’s electrical grid, old-fashioned nuclear energy is also being primed for a resurgence.

A series of new classes at Pellissippi State Community College will offer students a new career path — and a national laboratory a pipeline of workers who have the skills needed for its own rapidly growing programs.

Researchers in the geothermal energy industry are joining forces with fusion experts at ORNL to repurpose gyrotron technology, a tool used in fusion. Gyrotrons produce high-powered microwaves to heat up fusion plasmas.
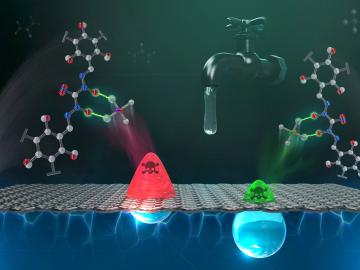
Researchers at ORNL are tackling a global water challenge with a unique material designed to target not one, but two toxic, heavy metal pollutants for simultaneous removal.
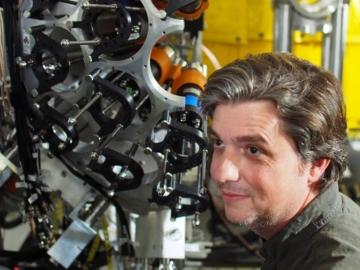
Two decades in the making, a new flagship facility for nuclear physics opened on May 2, and scientists from the Department of Energy’s Oak Ridge National Laboratory have a hand in 10 of its first 34 experiments.
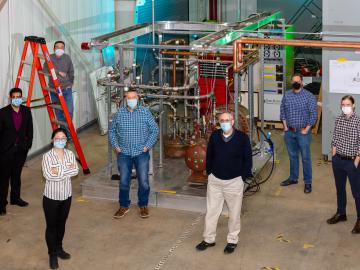
To achieve practical energy from fusion, extreme heat from the fusion system “blanket” component must be extracted safely and efficiently. ORNL fusion experts are exploring how tiny 3D-printed obstacles placed inside the narrow pipes of a custom-made cooling system could be a solution for removing heat from the blanket.
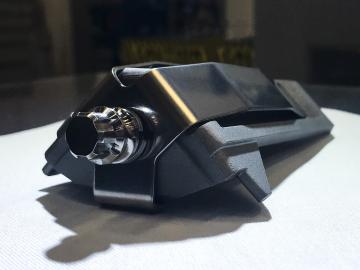
Four first-of-a-kind 3D-printed fuel assembly brackets, produced at the Department of Energy’s Manufacturing Demonstration Facility at Oak Ridge National Laboratory, have been installed and are now under routine operating