
Filter News
Area of Research
News Topics
- (-) Advanced Reactors (3)
- (-) Climate Change (8)
- (-) Isotopes (6)
- (-) Polymers (4)
- (-) Space Exploration (2)
- 3-D Printing/Advanced Manufacturing (25)
- Artificial Intelligence (5)
- Big Data (2)
- Bioenergy (11)
- Biology (4)
- Biomedical (4)
- Biotechnology (1)
- Buildings (11)
- Chemical Sciences (8)
- Clean Water (5)
- Composites (3)
- Computer Science (13)
- Coronavirus (6)
- Cybersecurity (6)
- Decarbonization (15)
- Energy Storage (22)
- Environment (23)
- Exascale Computing (1)
- Fossil Energy (1)
- Fusion (2)
- Grid (13)
- High-Performance Computing (3)
- Machine Learning (2)
- Materials (24)
- Materials Science (20)
- Mathematics (2)
- Mercury (1)
- Microelectronics (1)
- Microscopy (8)
- Nanotechnology (9)
- National Security (1)
- Net Zero (1)
- Neutron Science (11)
- Nuclear Energy (11)
- Partnerships (5)
- Physics (11)
- Quantum Computing (1)
- Quantum Science (1)
- Security (4)
- Simulation (1)
- Summit (3)
- Sustainable Energy (15)
- Transformational Challenge Reactor (2)
- Transportation (19)
Media Contacts
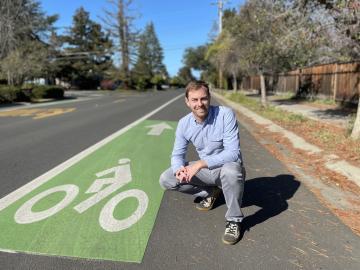
David McCollum is using his interdisciplinary expertise, international networks and boundless enthusiasm to lead Oak Ridge National Laboratory’s contributions to the Net Zero World initiative.
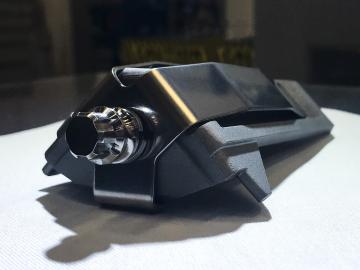
Four first-of-a-kind 3D-printed fuel assembly brackets, produced at the Department of Energy’s Manufacturing Demonstration Facility at Oak Ridge National Laboratory, have been installed and are now under routine operating

Oak Ridge National Laboratory was among an international team, led by Lawrence Livermore National Laboratory, who synthesized 108 elevated carbon dioxide, or CO2, experiments performed in various ecosystems to find out how much carbon is

On Feb. 18, the world will be watching as NASA’s Perseverance rover makes its final descent into Jezero Crater on the surface of Mars. Mars 2020 is the first NASA mission that uses plutonium-238 produced at the Department of Energy’s Oak Ridge National Laboratory.
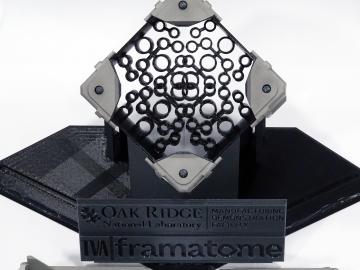
The Transformational Challenge Reactor, or TCR, a microreactor built using 3D printing and other new advanced technologies, could be operational by 2024.
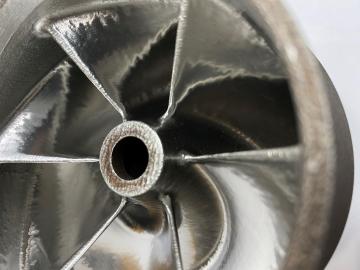
Scientists at the Department of Energy Manufacturing Demonstration Facility at ORNL have their eyes on the prize: the Transformational Challenge Reactor, or TCR, a microreactor built using 3D printing and other new approaches that will be up and running by 2023.
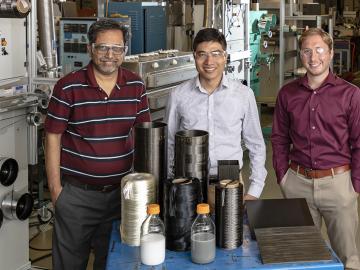
Carbon fiber composites—lightweight and strong—are great structural materials for automobiles, aircraft and other transportation vehicles. They consist of a polymer matrix, such as epoxy, into which reinforcing carbon fibers have been embedded. Because of differences in the mecha...
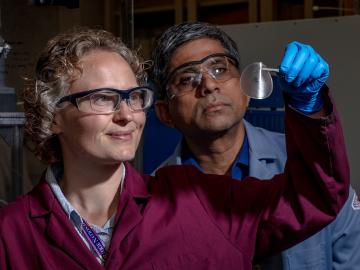
Oak Ridge National Laboratory scientists have developed a crucial component for a new kind of low-cost stationary battery system utilizing common materials and designed for grid-scale electricity storage. Large, economical electricity storage systems can benefit the nation’s grid ...
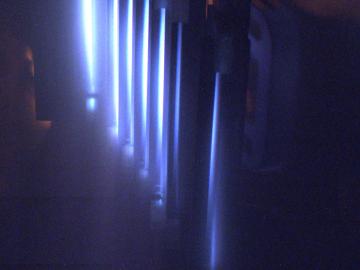
A tiny vial of gray powder produced at the Department of Energy’s Oak Ridge National Laboratory is the backbone of a new experiment to study the intense magnetic fields created in nuclear collisions.
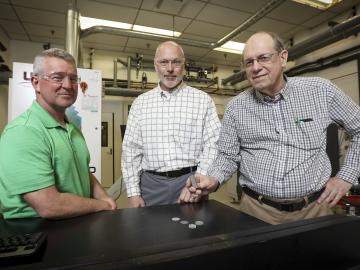
“Made in the USA.” That can now be said of the radioactive isotope molybdenum-99 (Mo-99), last made in the United States in the late 1980s. Its short-lived decay product, technetium-99m (Tc-99m), is the most widely used radioisotope in medical diagnostic imaging. Tc-99m is best known ...