Filter News
Area of Research
News Topics
- (-) Composites (5)
- (-) Environment (12)
- (-) Materials Science (11)
- (-) Nanotechnology (4)
- (-) Space Exploration (2)
- 3-D Printing/Advanced Manufacturing (24)
- Advanced Reactors (1)
- Artificial Intelligence (3)
- Big Data (3)
- Bioenergy (3)
- Biology (7)
- Biomedical (2)
- Biotechnology (1)
- Buildings (11)
- Chemical Sciences (2)
- Clean Water (1)
- Climate Change (4)
- Computer Science (8)
- Coronavirus (4)
- Critical Materials (3)
- Decarbonization (5)
- Energy Storage (20)
- Fusion (1)
- Grid (8)
- High-Performance Computing (5)
- Materials (19)
- Mathematics (1)
- Microscopy (2)
- Net Zero (1)
- Neutron Science (14)
- Nuclear Energy (1)
- Physics (1)
- Polymers (3)
- Quantum Computing (1)
- Quantum Science (2)
- Security (1)
- Statistics (1)
- Summit (1)
- Sustainable Energy (24)
- Transportation (16)
Media Contacts
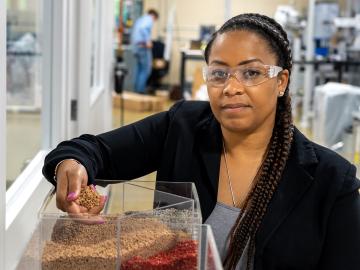
ORNL and Tuskegee University have formed a partnership to develop new biodegradable materials for use in buildings, transportation and biomedical applications.

Ten scientists from the Department of Energy’s Oak Ridge National Laboratory are among the world’s most highly cited researchers, according to a bibliometric analysis conducted by the scientific publication analytics firm Clarivate.
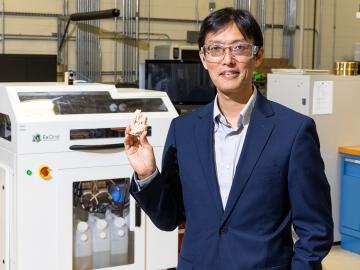
Researchers at ORNL designed a novel polymer to bind and strengthen silica sand for binder jet additive manufacturing, a 3D-printing method used by industries for prototyping and part production.

A team led by the U.S. Department of Energy’s Oak Ridge National Laboratory demonstrated the viability of a “quantum entanglement witness” capable of proving the presence of entanglement between magnetic particles, or spins, in a quantum material.
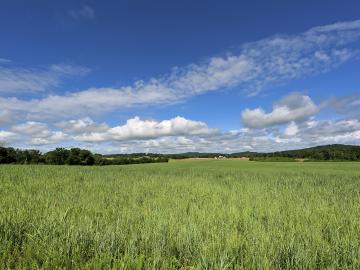
Nearly a billion acres of land in the United States is dedicated to agriculture, producing more than a trillion dollars of food products to feed the country and the world. Those same agricultural processes, however, also produced an estimated 700 million metric tons of carbon dioxide equivalent in 2018, according to the U.S. Department of Agriculture.
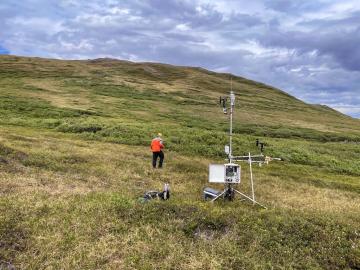
Improved data, models and analyses from ORNL scientists and many other researchers in the latest global climate assessment report provide new levels of certainty about what the future holds for the planet

A research team at Oak Ridge National Laboratory have 3D printed a thermal protection shield, or TPS, for a capsule that will launch with the Cygnus cargo spacecraft as part of the supply mission to the International Space Station.
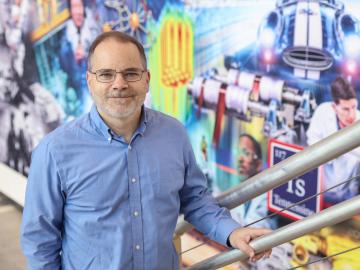
David Sholl has come to the U.S. Department of Energy’s Oak Ridge National Laboratory with a wealth of scientific expertise and a personal mission: hasten the development and deployment of decarbonization solutions for the nation’s energy system.
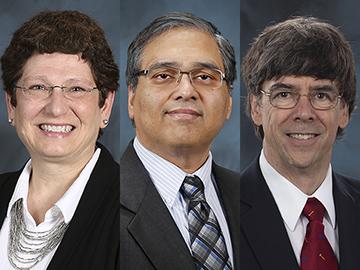
ASM International recently elected three researchers from ORNL as 2021 fellows. Selected were Beth Armstrong and Govindarajan Muralidharan, both from ORNL’s Material Sciences and Technology Division, and Andrew Payzant from the Neutron Scattering Division.

Scientists at ORNL and the University of Tennessee, Knoxville, have found a way to simultaneously increase the strength and ductility of an alloy by introducing tiny precipitates into its matrix and tuning their size and spacing.