Filter News
Area of Research
- (-) Clean Energy (25)
- (-) Neutron Science (10)
- Advanced Manufacturing (3)
- Biology and Environment (5)
- Building Technologies (1)
- Computational Engineering (2)
- Computer Science (4)
- Fusion and Fission (2)
- Materials (6)
- Materials for Computing (9)
- Mathematics (1)
- National Security (1)
- Quantum information Science (1)
- Supercomputing (6)
News Type
News Topics
- (-) Computer Science (4)
- (-) Coronavirus (2)
- (-) Microscopy (1)
- (-) Neutron Science (9)
- (-) Polymers (3)
- (-) Sustainable Energy (20)
- 3-D Printing/Advanced Manufacturing (18)
- Artificial Intelligence (1)
- Big Data (2)
- Bioenergy (2)
- Biology (5)
- Biomedical (1)
- Biotechnology (1)
- Buildings (7)
- Chemical Sciences (1)
- Clean Water (1)
- Climate Change (3)
- Composites (5)
- Critical Materials (3)
- Decarbonization (2)
- Energy Storage (13)
- Environment (6)
- Fusion (1)
- Grid (6)
- High-Performance Computing (2)
- Materials (17)
- Materials Science (8)
- Mathematics (1)
- Nanotechnology (2)
- Net Zero (1)
- Physics (1)
- Quantum Science (1)
- Space Exploration (2)
- Statistics (1)
- Transportation (10)
Media Contacts

Ten scientists from the Department of Energy’s Oak Ridge National Laboratory are among the world’s most highly cited researchers, according to a bibliometric analysis conducted by the scientific publication analytics firm Clarivate.
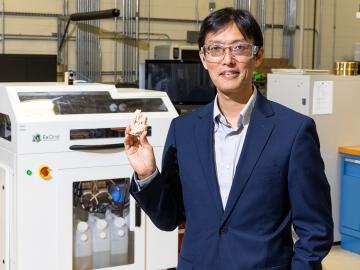
Researchers at ORNL designed a novel polymer to bind and strengthen silica sand for binder jet additive manufacturing, a 3D-printing method used by industries for prototyping and part production.
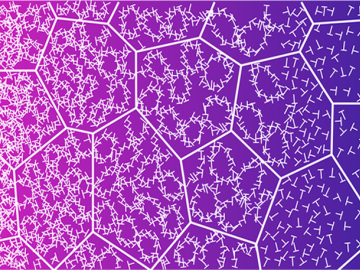
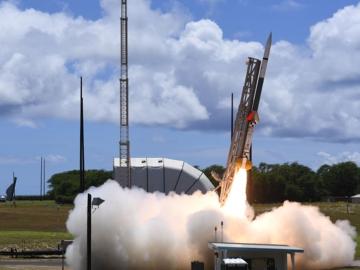
Oak Ridge National Laboratory researchers have developed a novel process to manufacture extreme heat resistant carbon-carbon composites. The performance of these materials will be tested in a U.S. Navy rocket that NASA will launch this fall.
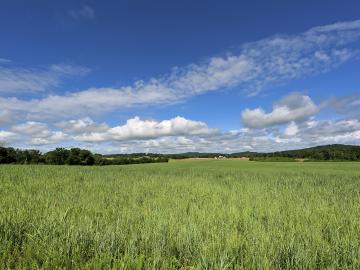
Nearly a billion acres of land in the United States is dedicated to agriculture, producing more than a trillion dollars of food products to feed the country and the world. Those same agricultural processes, however, also produced an estimated 700 million metric tons of carbon dioxide equivalent in 2018, according to the U.S. Department of Agriculture.
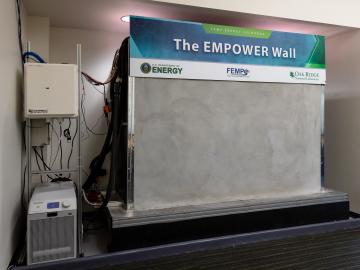
Oak Ridge National Laboratory researchers demonstrated that cooling cost savings could be achieved with a 3D printed concrete smart wall following a three-month field test.
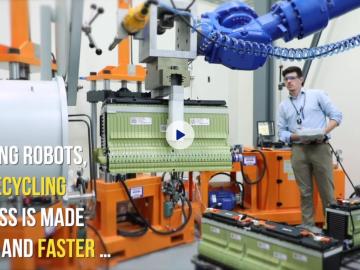
Researchers at ORNL have developed a robotic disassembly system for spent electric vehicle battery packs to safely and efficiently recycle and reuse critical materials while reducing toxic waste.

A research team at Oak Ridge National Laboratory have 3D printed a thermal protection shield, or TPS, for a capsule that will launch with the Cygnus cargo spacecraft as part of the supply mission to the International Space Station.
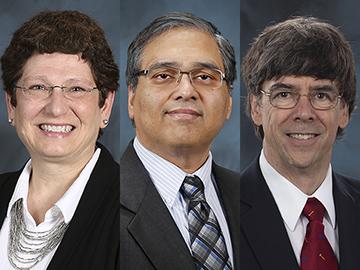
ASM International recently elected three researchers from ORNL as 2021 fellows. Selected were Beth Armstrong and Govindarajan Muralidharan, both from ORNL’s Material Sciences and Technology Division, and Andrew Payzant from the Neutron Scattering Division.

Scientists at ORNL and the University of Tennessee, Knoxville, have found a way to simultaneously increase the strength and ductility of an alloy by introducing tiny precipitates into its matrix and tuning their size and spacing.