
Filter News
Area of Research
- (-) Advanced Manufacturing (14)
- (-) Building Technologies (2)
- (-) Nuclear Science and Technology (15)
- Biology and Environment (5)
- Clean Energy (76)
- Climate and Environmental Systems (1)
- Computational Biology (1)
- Computational Engineering (3)
- Computer Science (12)
- Fuel Cycle Science and Technology (1)
- Fusion and Fission (6)
- Fusion Energy (5)
- Isotopes (11)
- Materials (31)
- Materials for Computing (8)
- Mathematics (1)
- National Security (7)
- Neutron Science (11)
- Quantum information Science (5)
- Sensors and Controls (1)
- Supercomputing (44)
- Transportation Systems (2)
News Topics
- (-) 3-D Printing/Advanced Manufacturing (14)
- (-) Computer Science (3)
- (-) Cybersecurity (1)
- (-) Isotopes (2)
- (-) Nuclear Energy (15)
- Advanced Reactors (5)
- Bioenergy (1)
- Biomedical (1)
- Buildings (1)
- Composites (3)
- Fusion (2)
- Materials (5)
- Materials Science (5)
- Molten Salt (3)
- Neutron Science (2)
- Space Exploration (3)
- Sustainable Energy (5)
Media Contacts
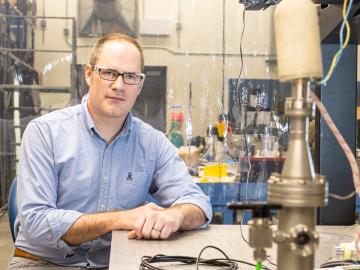
If humankind reaches Mars this century, an Oak Ridge National Laboratory-developed experiment testing advanced materials for spacecraft may play a key role.
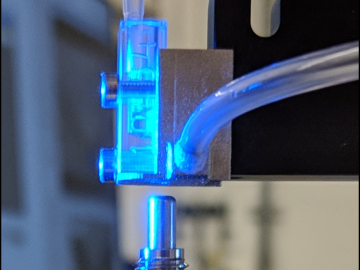
Researchers at the Department of Energy’s Oak Ridge National Laboratory have received five 2019 R&D 100 Awards, increasing the lab’s total to 221 since the award’s inception in 1963.
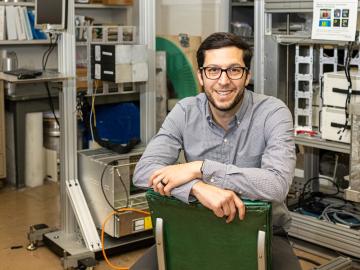
Jason Nattress, an Alvin M. Weinberg Fellow at the Department of Energy’s Oak Ridge National Laboratory, found his calling on a nuclear submarine.
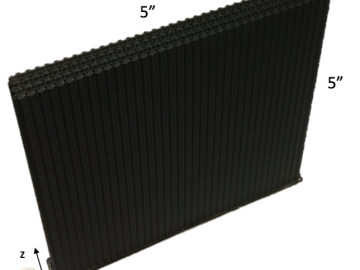
A team including Oak Ridge National Laboratory and University of Tennessee researchers demonstrated a novel 3D printing approach called Z-pinning that can increase the material’s strength and toughness by more than three and a half times compared to conventional additive manufacturing processes.
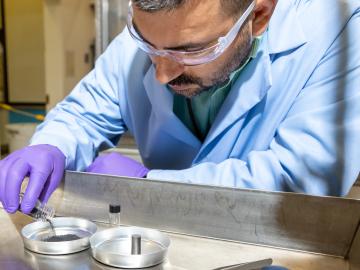
Ask Tyler Gerczak to find a negative in working at the Department of Energy’s Oak Ridge National Laboratory, and his only complaint is the summer weather. It is not as forgiving as the summers in Pulaski, Wisconsin, his hometown.
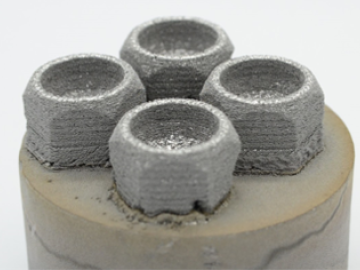
Using additive manufacturing, scientists experimenting with tungsten at Oak Ridge National Laboratory hope to unlock new potential of the high-performance heat-transferring material used to protect components from the plasma inside a fusion reactor. Fusion requires hydrogen isotopes to reach millions of degrees.

Researchers have developed high-fidelity modeling capabilities for predicting radiation interactions outside of the reactor core—a tool that could help keep nuclear reactors running longer.
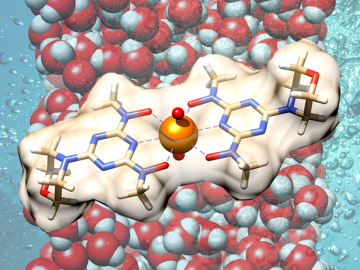
Scientists have demonstrated a new bio-inspired material for an eco-friendly and cost-effective approach to recovering uranium from seawater.
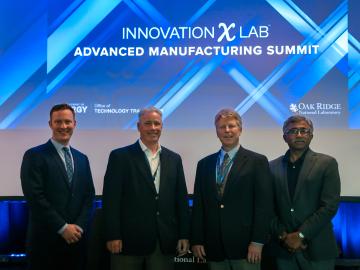
OAK RIDGE, Tenn., May 8, 2019—Oak Ridge National Laboratory and Lincoln Electric (NASDAQ: LECO) announced their continued collaboration on large-scale, robotic additive manufacturing technology at the Department of Energy’s Advanced Manufacturing InnovationXLab Summit.
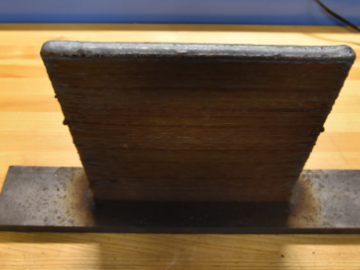
A novel additive manufacturing method developed by researchers at Oak Ridge National Laboratory could be a promising alternative for low-cost, high-quality production of large-scale metal parts with less material waste.