Filter News
Area of Research
News Topics
- (-) 3-D Printing/Advanced Manufacturing (4)
- (-) Biomedical (4)
- (-) Cybersecurity (1)
- (-) Environment (2)
- (-) Mercury (1)
- Bioenergy (2)
- Biology (1)
- Climate Change (1)
- Composites (2)
- Computer Science (2)
- Energy Storage (1)
- Fusion (1)
- Grid (3)
- Isotopes (5)
- Materials Science (7)
- Microscopy (4)
- Nanotechnology (7)
- Neutron Science (5)
- Nuclear Energy (2)
- Physics (4)
- Polymers (3)
- Security (2)
- Space Exploration (2)
- Summit (1)
- Transportation (4)
Media Contacts
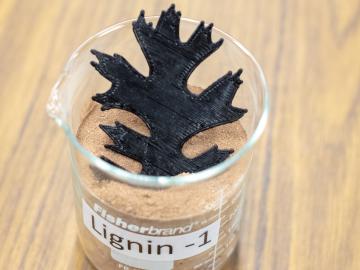
Scientists at the Department of Energy’s Oak Ridge National Laboratory have created a recipe for a renewable 3D printing feedstock that could spur a profitable new use for an intractable biorefinery byproduct: lignin.
![2018-P07635 BL-6 user - Univ of Guelph-6004R_sm[2].jpg 2018-P07635 BL-6 user - Univ of Guelph-6004R_sm[2].jpg](/sites/default/files/styles/list_page_thumbnail/public/2018-P07635%20BL-6%20user%20-%20Univ%20of%20Guelph-6004R_sm%5B2%5D.jpg?itok=DUdZNt_q)
A team of scientists, led by University of Guelph professor John Dutcher, are using neutrons at ORNL’s Spallation Neutron Source to unlock the secrets of natural nanoparticles that could be used to improve medicines.
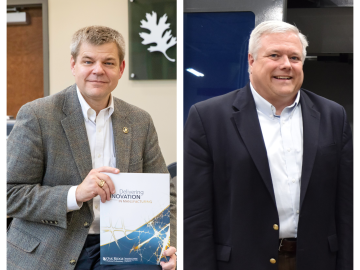
Two leaders in US manufacturing innovation, Thomas Kurfess and Scott Smith, are joining the Department of Energy’s Oak Ridge National Laboratory to support its pioneering research in advanced manufacturing.
Scientists studying a valuable, but vulnerable, species of poplar have identified the genetic mechanism responsible for the species’ inability to resist a pervasive and deadly disease. Their finding, published in the Proceedings of the National Academy of Sciences, could lead to more successful hybrid poplar varieties for increased biofuels and forestry production and protect native trees against infection.

Biologists from Oak Ridge National Laboratory and the Smithsonian Environmental Research Center have confirmed that microorganisms called methanogens can transform mercury into the neurotoxin methylmercury with varying efficiency across species.

The construction industry may soon benefit from 3D printed molds to make concrete facades, promising lower cost and production time. Researchers at Oak Ridge National Laboratory are evaluating the performance of 3D printed molds used to precast concrete facades in a 42-story buildin...
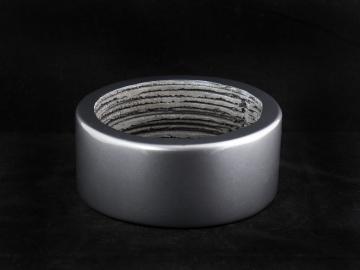
Oak Ridge National Laboratory scientists have improved a mixture of materials used to 3D print permanent magnets with increased density, which could yield longer lasting, better performing magnets for electric motors, sensors and vehicle applications. Building on previous research, ...
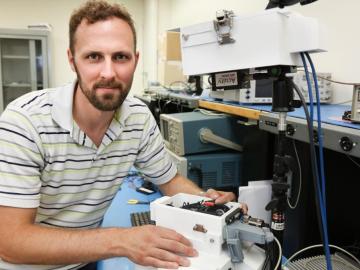
As leader of the RF, Communications, and Cyber-Physical Security Group at Oak Ridge National Laboratory, Kerekes heads an accelerated lab-directed research program to build virtual models of critical infrastructure systems like the power grid that can be used to develop ways to detect and repel cyber-intrusion and to make the network resilient when disruption occurs.
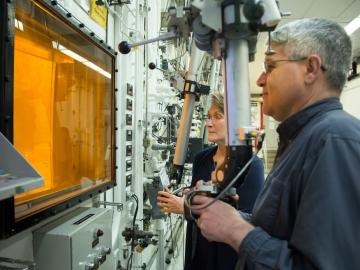
The Department of Energy’s Oak Ridge National Laboratory is now producing actinium-227 (Ac-227) to meet projected demand for a highly effective cancer drug through a 10-year contract between the U.S. DOE Isotope Program and Bayer.
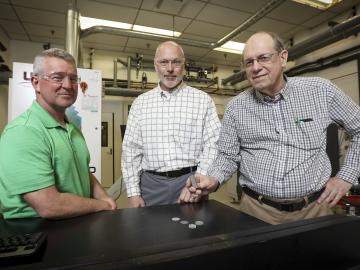
“Made in the USA.” That can now be said of the radioactive isotope molybdenum-99 (Mo-99), last made in the United States in the late 1980s. Its short-lived decay product, technetium-99m (Tc-99m), is the most widely used radioisotope in medical diagnostic imaging. Tc-99m is best known ...