Filter News
Area of Research
News Topics
- (-) 3-D Printing/Advanced Manufacturing (5)
- (-) Composites (3)
- (-) Computer Science (3)
- (-) Cybersecurity (1)
- (-) Isotopes (5)
- (-) Physics (5)
- (-) Space Exploration (2)
- Advanced Reactors (1)
- Bioenergy (2)
- Biology (1)
- Biomedical (3)
- Climate Change (1)
- Energy Storage (2)
- Environment (3)
- Fusion (1)
- Grid (3)
- Materials Science (8)
- Mercury (2)
- Microscopy (5)
- Molten Salt (3)
- Nanotechnology (6)
- Neutron Science (6)
- Nuclear Energy (5)
- Polymers (3)
- Security (2)
- Summit (1)
- Transportation (5)
Media Contacts
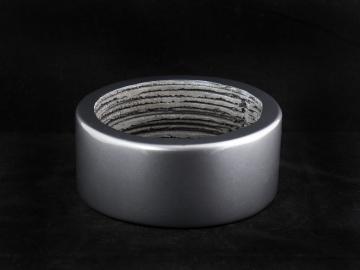
Oak Ridge National Laboratory scientists have improved a mixture of materials used to 3D print permanent magnets with increased density, which could yield longer lasting, better performing magnets for electric motors, sensors and vehicle applications. Building on previous research, ...
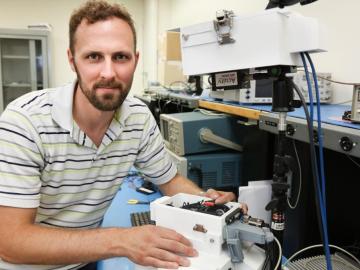
As leader of the RF, Communications, and Cyber-Physical Security Group at Oak Ridge National Laboratory, Kerekes heads an accelerated lab-directed research program to build virtual models of critical infrastructure systems like the power grid that can be used to develop ways to detect and repel cyber-intrusion and to make the network resilient when disruption occurs.
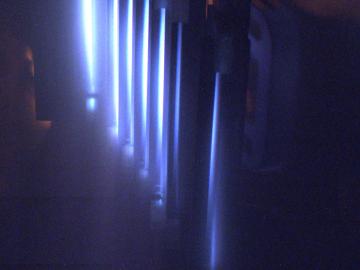
A tiny vial of gray powder produced at the Department of Energy’s Oak Ridge National Laboratory is the backbone of a new experiment to study the intense magnetic fields created in nuclear collisions.
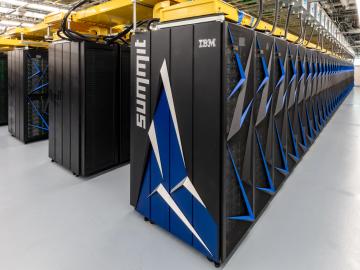
The U.S. Department of Energy’s Oak Ridge National Laboratory today unveiled Summit as the world’s most powerful and smartest scientific supercomputer.
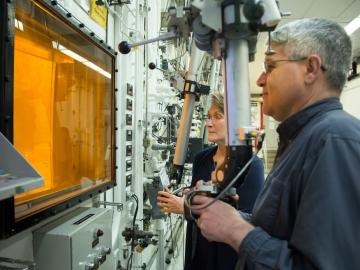
The Department of Energy’s Oak Ridge National Laboratory is now producing actinium-227 (Ac-227) to meet projected demand for a highly effective cancer drug through a 10-year contract between the U.S. DOE Isotope Program and Bayer.
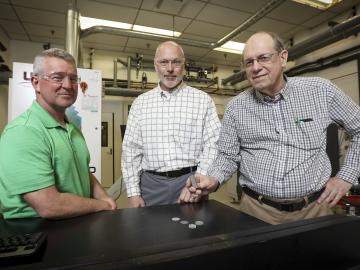
“Made in the USA.” That can now be said of the radioactive isotope molybdenum-99 (Mo-99), last made in the United States in the late 1980s. Its short-lived decay product, technetium-99m (Tc-99m), is the most widely used radioisotope in medical diagnostic imaging. Tc-99m is best known ...
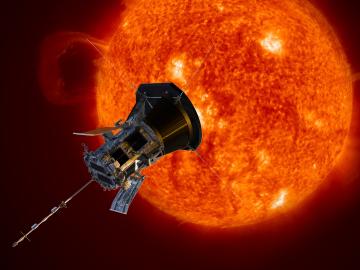
A shield assembly that protects an instrument measuring ion and electron fluxes for a NASA mission to touch the Sun was tested in extreme experimental environments at Oak Ridge National Laboratory—and passed with flying colors. Components aboard Parker Solar Probe, which will endure th...
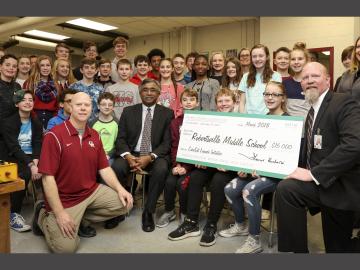
Last November a team of students and educators from Robertsville Middle School in Oak Ridge and scientists from Oak Ridge National Laboratory submitted a proposal to NASA for their Cube Satellite Launch Initiative in hopes of sending a student-designed nanosatellite named RamSat into...
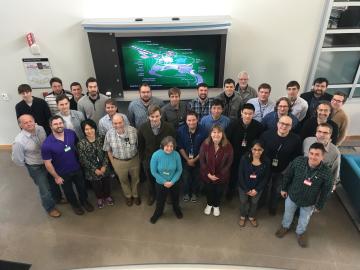
After more than a year of operation at the Department of Energy’s (DOE’s) Oak Ridge National Laboratory (ORNL), the COHERENT experiment, using the world’s smallest neutrino detector, has found a big fingerprint of the elusive, electrically neutral particles that interact only weakly with matter.
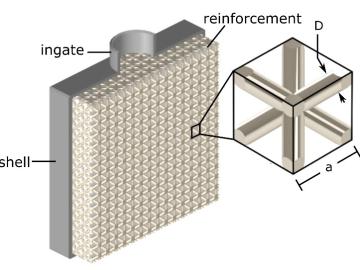
A new manufacturing method created by Oak Ridge National Laboratory and Rice University combines 3D printing with traditional casting to produce damage-tolerant components composed of multiple materials. Composite components made by pouring an aluminum alloy over a printed steel lattice showed an order of magnitude greater damage tolerance than aluminum alone.