Filter News
Area of Research
- Advanced Manufacturing (1)
- Biology and Environment (21)
- Biology and Soft Matter (1)
- Clean Energy (37)
- Electricity and Smart Grid (1)
- Functional Materials for Energy (1)
- Fusion and Fission (2)
- Materials (10)
- Materials for Computing (1)
- National Security (2)
- Neutron Science (2)
- Nuclear Science and Technology (4)
- Supercomputing (5)
- Transportation Systems (1)
News Topics
- (-) Decarbonization (78)
- (-) Net Zero (13)
- (-) Transformational Challenge Reactor (7)
- 3-D Printing/Advanced Manufacturing (119)
- Advanced Reactors (34)
- Artificial Intelligence (91)
- Big Data (53)
- Bioenergy (91)
- Biology (98)
- Biomedical (58)
- Biotechnology (22)
- Buildings (57)
- Chemical Sciences (63)
- Clean Water (29)
- Climate Change (99)
- Composites (26)
- Computer Science (186)
- Coronavirus (46)
- Critical Materials (25)
- Cybersecurity (35)
- Education (4)
- Element Discovery (1)
- Emergency (2)
- Energy Storage (108)
- Environment (194)
- Exascale Computing (37)
- Fossil Energy (5)
- Frontier (42)
- Fusion (53)
- Grid (62)
- High-Performance Computing (84)
- Hydropower (11)
- Irradiation (3)
- Isotopes (52)
- ITER (7)
- Machine Learning (47)
- Materials (143)
- Materials Science (138)
- Mathematics (7)
- Mercury (12)
- Microelectronics (2)
- Microscopy (51)
- Molten Salt (8)
- Nanotechnology (60)
- National Security (60)
- Neutron Science (130)
- Nuclear Energy (106)
- Partnerships (42)
- Physics (59)
- Polymers (33)
- Quantum Computing (32)
- Quantum Science (67)
- Renewable Energy (2)
- Security (24)
- Simulation (46)
- Software (1)
- Space Exploration (25)
- Statistics (3)
- Summit (57)
- Sustainable Energy (125)
- Transportation (95)
Media Contacts
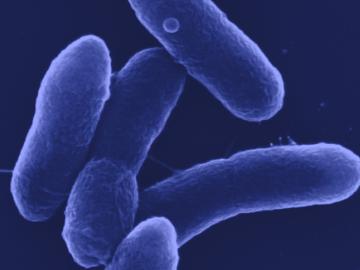
A research team led by Oak Ridge National Laboratory bioengineered a microbe to efficiently turn waste into itaconic acid, an industrial chemical used in plastics and paints.
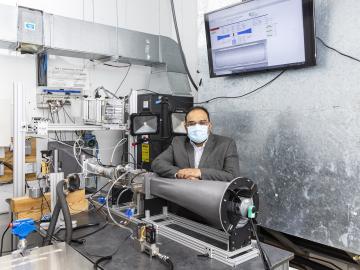
When Kashif Nawaz looks at a satellite map of the U.S., he sees millions of buildings that could hold a potential solution for the capture of carbon dioxide, a plentiful gas that can be harmful when excessive amounts are released into the atmosphere, raising the Earth’s temperature.
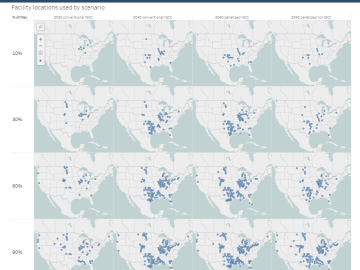
The combination of bioenergy with carbon capture and storage could cost-effectively sequester hundreds of millions of metric tons per year of carbon dioxide in the United States, making it a competitive solution for carbon management, according to a new analysis by ORNL scientists.
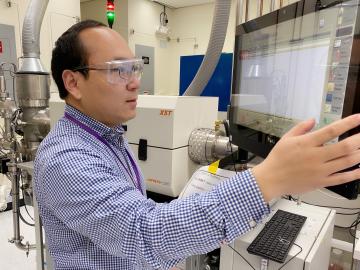
About 60 years ago, scientists discovered that a certain rare earth metal-hydrogen mixture, yttrium, could be the ideal moderator to go inside small, gas-cooled nuclear reactors.
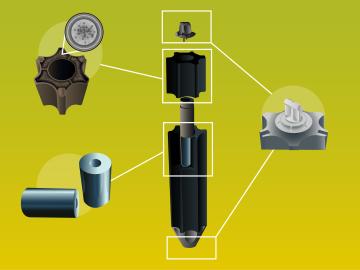
It’s a new type of nuclear reactor core. And the materials that will make it up are novel — products of Oak Ridge National Laboratory’s advanced materials and manufacturing technologies.
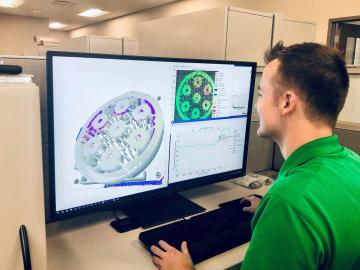
Oak Ridge National Laboratory researchers have developed artificial intelligence software for powder bed 3D printers that assesses the quality of parts in real time, without the need for expensive characterization equipment.
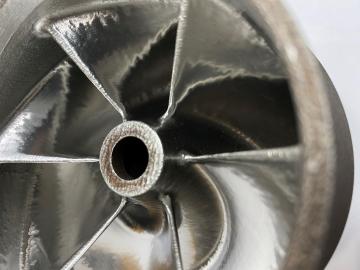
Scientists at the Department of Energy Manufacturing Demonstration Facility at ORNL have their eyes on the prize: the Transformational Challenge Reactor, or TCR, a microreactor built using 3D printing and other new approaches that will be up and running by 2023.

Researchers at the Department of Energy’s Oak Ridge National Laboratory are refining their design of a 3D-printed nuclear reactor core, scaling up the additive manufacturing process necessary to build it, and developing methods