
Filter News
Area of Research
- (-) Fusion and Fission (7)
- (-) Materials (18)
- Advanced Manufacturing (1)
- Biology and Environment (4)
- Clean Energy (70)
- Fusion Energy (7)
- Materials for Computing (5)
- National Security (3)
- Neutron Science (6)
- Nuclear Science and Technology (11)
- Nuclear Systems Modeling, Simulation and Validation (1)
- Supercomputing (7)
- Transportation Systems (2)
News Topics
- (-) Advanced Reactors (10)
- (-) Transportation (16)
- 3-D Printing/Advanced Manufacturing (26)
- Artificial Intelligence (10)
- Big Data (2)
- Bioenergy (11)
- Biology (5)
- Biomedical (8)
- Buildings (5)
- Chemical Sciences (34)
- Clean Water (3)
- Climate Change (5)
- Composites (9)
- Computer Science (19)
- Coronavirus (4)
- Critical Materials (13)
- Cybersecurity (4)
- Decarbonization (9)
- Energy Storage (35)
- Environment (17)
- Exascale Computing (3)
- Fossil Energy (1)
- Frontier (4)
- Fusion (27)
- Grid (6)
- High-Performance Computing (6)
- Irradiation (1)
- Isotopes (14)
- ITER (6)
- Machine Learning (5)
- Materials (74)
- Materials Science (80)
- Mathematics (1)
- Microscopy (27)
- Molten Salt (3)
- Nanotechnology (39)
- National Security (3)
- Net Zero (2)
- Neutron Science (34)
- Nuclear Energy (42)
- Partnerships (13)
- Physics (30)
- Polymers (17)
- Quantum Computing (3)
- Quantum Science (11)
- Renewable Energy (1)
- Security (4)
- Simulation (4)
- Space Exploration (3)
- Summit (2)
- Sustainable Energy (17)
- Transformational Challenge Reactor (3)
Media Contacts
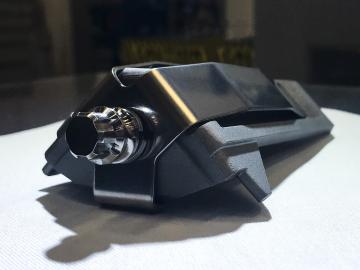
Four first-of-a-kind 3D-printed fuel assembly brackets, produced at the Department of Energy’s Manufacturing Demonstration Facility at Oak Ridge National Laboratory, have been installed and are now under routine operating
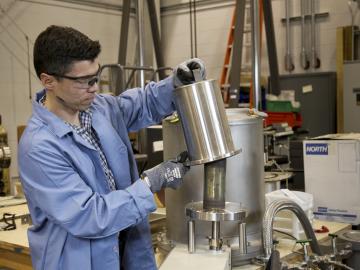
As program manager for the Department of Energy’s Oak Ridge National Laboratory’s Package Testing Program, Oscar Martinez enjoys finding and fixing technical issues.
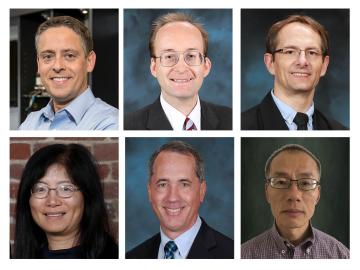
Six scientists at the Department of Energy’s Oak Ridge National Laboratory were named Battelle Distinguished Inventors, in recognition of obtaining 14 or more patents during their careers at the lab.
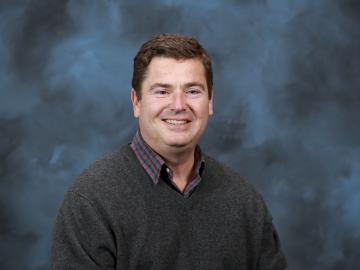
David Kropaczek, director of the Consortium for Advanced Simulation of Light Water Reactors, or CASL, at the Department of Energy’s Oak Ridge National Laboratory, has been named a fellow of the American Nuclear Society.
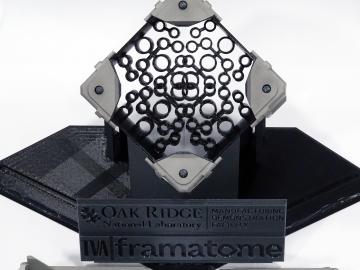
The Transformational Challenge Reactor, or TCR, a microreactor built using 3D printing and other new advanced technologies, could be operational by 2024.
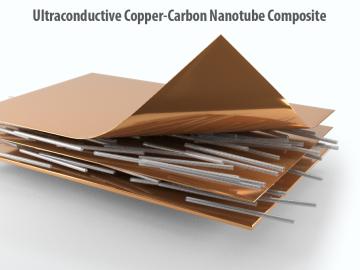
Scientists at Oak Ridge National Laboratory used new techniques to create a composite that increases the electrical current capacity of copper wires, providing a new material that can be scaled for use in ultra-efficient, power-dense electric vehicle traction motors.
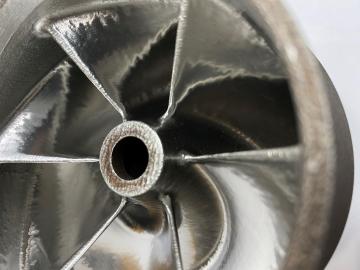
Scientists at the Department of Energy Manufacturing Demonstration Facility at ORNL have their eyes on the prize: the Transformational Challenge Reactor, or TCR, a microreactor built using 3D printing and other new approaches that will be up and running by 2023.
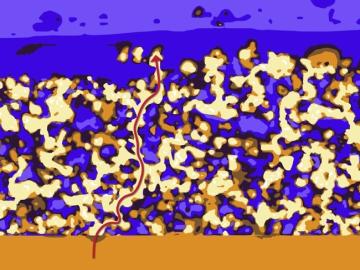
Oak Ridge National Laboratory researchers have developed a thin film, highly conductive solid-state electrolyte made of a polymer and ceramic-based composite for lithium metal batteries.

ORNL and The University of Toledo have entered into a memorandum of understanding for collaborative research.
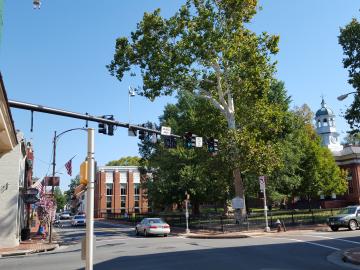
A modern, healthy transportation system is vital to the nation’s economic security and the American standard of living. The U.S. Department of Energy’s Oak Ridge National Laboratory (ORNL) is engaged in a broad portfolio of scientific research for improved mobility