
Filter News
Area of Research
- (-) Biology and Environment (24)
- (-) Clean Energy (104)
- (-) Neutron Science (32)
- Advanced Manufacturing (22)
- Building Technologies (1)
- Climate and Environmental Systems (1)
- Computer Science (4)
- Electricity and Smart Grid (1)
- Functional Materials for Energy (1)
- Fusion and Fission (27)
- Fusion Energy (13)
- Isotope Development and Production (1)
- Isotopes (2)
- Materials (101)
- Materials Characterization (1)
- Materials for Computing (16)
- Materials Under Extremes (1)
- National Security (15)
- Nuclear Science and Technology (14)
- Quantum information Science (9)
- Sensors and Controls (1)
- Supercomputing (44)
- Transportation Systems (1)
News Topics
- (-) 3-D Printing/Advanced Manufacturing (82)
- (-) Fusion (2)
- (-) Materials Science (50)
- (-) Mercury (10)
- (-) Quantum Science (8)
- (-) Security (8)
- Advanced Reactors (6)
- Artificial Intelligence (20)
- Big Data (15)
- Bioenergy (68)
- Biology (81)
- Biomedical (30)
- Biotechnology (16)
- Buildings (36)
- Chemical Sciences (20)
- Clean Water (21)
- Climate Change (59)
- Composites (19)
- Computer Science (50)
- Coronavirus (27)
- Critical Materials (9)
- Cybersecurity (9)
- Decarbonization (48)
- Energy Storage (76)
- Environment (141)
- Exascale Computing (6)
- Fossil Energy (3)
- Frontier (6)
- Grid (41)
- High-Performance Computing (25)
- Hydropower (9)
- Isotopes (2)
- Machine Learning (16)
- Materials (49)
- Mathematics (5)
- Microelectronics (1)
- Microscopy (17)
- Molten Salt (1)
- Nanotechnology (20)
- National Security (9)
- Net Zero (5)
- Neutron Science (100)
- Nuclear Energy (9)
- Partnerships (12)
- Physics (11)
- Polymers (13)
- Quantum Computing (1)
- Renewable Energy (2)
- Simulation (17)
- Space Exploration (6)
- Statistics (1)
- Summit (17)
- Sustainable Energy (93)
- Transformational Challenge Reactor (3)
- Transportation (68)
Media Contacts
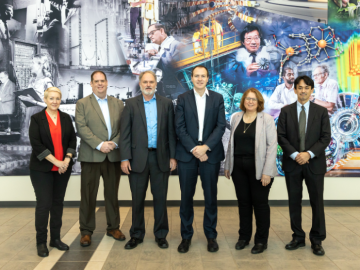
ORNL has entered a strategic research partnership with the United Kingdom Atomic Energy Authority, or UKAEA, to investigate how different types of materials behave under the influence of high-energy neutron sources. The $4 million project is part of UKAEA's roadmap program, which aims to produce electricity from fusion.

A scientific instrument at ORNL could help create a noninvasive cancer treatment derived from a common tropical plant.
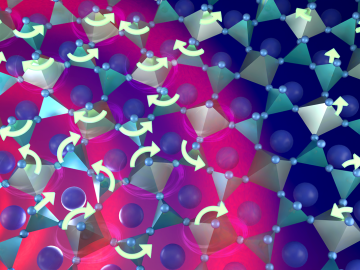
Warming a crystal of the mineral fresnoite, ORNL scientists discovered that excitations called phasons carried heat three times farther and faster than phonons, the excitations that usually carry heat through a material.

ORNL researchers have identified a mechanism in a 3D-printed alloy – termed “load shuffling” — that could enable the design of better-performing lightweight materials for vehicles.
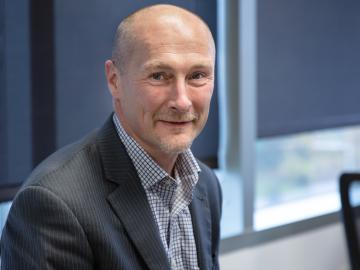
Paul Langan will join ORNL in the spring as associate laboratory director for the Biological and Environmental Systems Science Directorate.
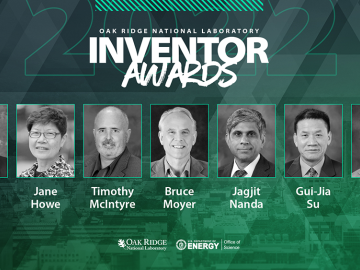
Seven scientists at the Department of Energy’s Oak Ridge National Laboratory have been named Battelle Distinguished Inventors, in recognition of their obtaining 14 or more patents during their careers at the lab.

Three researchers at ORNL have been named ORNL Corporate Fellows in recognition of significant career accomplishments and continued leadership in their scientific fields.
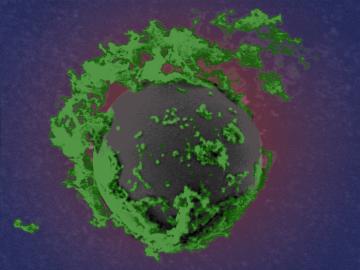
The presence of minerals called ash in plants makes little difference to the fitness of new naturally derived compound materials designed for additive manufacturing, an Oak Ridge National Laboratory-led team found.
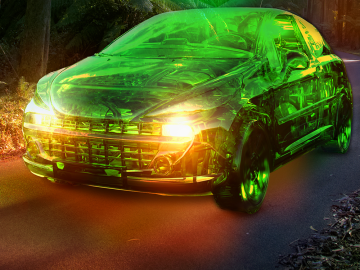
Oak Ridge National Laboratory scientists designed a recyclable polymer for carbon-fiber composites to enable circular manufacturing of parts that boost energy efficiency in automotive, wind power and aerospace applications.
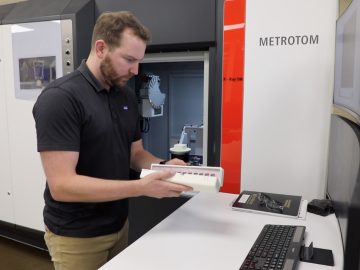
A new deep-learning framework developed at ORNL is speeding up the process of inspecting additively manufactured metal parts using X-ray computed tomography, or CT, while increasing the accuracy of the results. The reduced costs for time, labor, maintenance and energy are expected to accelerate expansion of additive manufacturing, or 3D printing.