Filter News
Area of Research
- (-) Fusion and Fission (11)
- (-) National Security (7)
- (-) Nuclear Science and Technology (12)
- (-) Transportation Systems (2)
- Advanced Manufacturing (6)
- Biology and Environment (37)
- Building Technologies (2)
- Clean Energy (129)
- Computer Science (2)
- Electricity and Smart Grid (1)
- Energy Sciences (1)
- Functional Materials for Energy (1)
- Fusion Energy (9)
- Materials (43)
- Materials for Computing (12)
- Neutron Science (10)
- Nuclear Systems Modeling, Simulation and Validation (1)
- Quantum information Science (1)
- Supercomputing (43)
News Topics
- (-) Advanced Reactors (18)
- (-) Frontier (2)
- (-) Sustainable Energy (8)
- (-) Transportation (6)
- 3-D Printing/Advanced Manufacturing (9)
- Artificial Intelligence (13)
- Big Data (6)
- Bioenergy (5)
- Biology (6)
- Biomedical (5)
- Biotechnology (1)
- Buildings (2)
- Chemical Sciences (6)
- Climate Change (5)
- Composites (1)
- Computer Science (23)
- Coronavirus (3)
- Critical Materials (1)
- Cybersecurity (19)
- Decarbonization (6)
- Energy Storage (6)
- Environment (8)
- Exascale Computing (2)
- Fossil Energy (1)
- Fusion (31)
- Grid (8)
- High-Performance Computing (6)
- Isotopes (6)
- ITER (6)
- Machine Learning (12)
- Materials (3)
- Materials Science (11)
- Microscopy (1)
- Molten Salt (4)
- Nanotechnology (2)
- National Security (34)
- Net Zero (1)
- Neutron Science (10)
- Nuclear Energy (65)
- Partnerships (7)
- Physics (4)
- Quantum Science (1)
- Security (13)
- Simulation (4)
- Space Exploration (6)
- Summit (2)
- Transformational Challenge Reactor (3)
Media Contacts

Staff at Oak Ridge National Laboratory organized transport for a powerful component that is critical to the world’s largest experiment, the international ITER project.
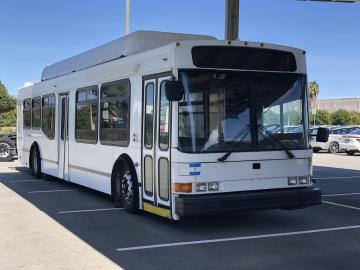
Oak Ridge National Laboratory researchers developed and demonstrated algorithm-based controls for a hybrid electric bus that yielded up to 30% energy savings compared with existing controls.
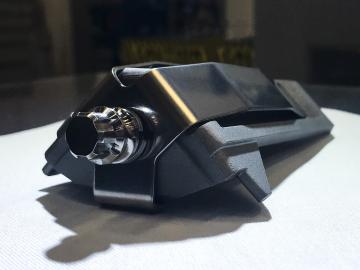
Four first-of-a-kind 3D-printed fuel assembly brackets, produced at the Department of Energy’s Manufacturing Demonstration Facility at Oak Ridge National Laboratory, have been installed and are now under routine operating
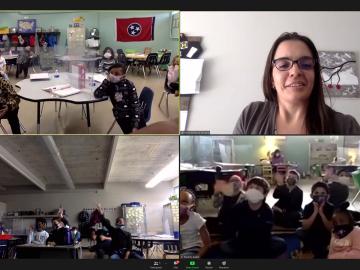
Twenty-seven ORNL researchers Zoomed into 11 middle schools across Tennessee during the annual Engineers Week in February. East Tennessee schools throughout Oak Ridge and Roane, Sevier, Blount and Loudon counties participated, with three West Tennessee schools joining in.
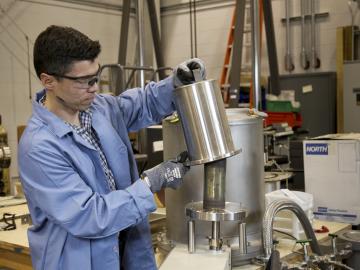
As program manager for the Department of Energy’s Oak Ridge National Laboratory’s Package Testing Program, Oscar Martinez enjoys finding and fixing technical issues.
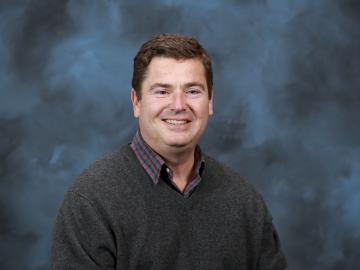
David Kropaczek, director of the Consortium for Advanced Simulation of Light Water Reactors, or CASL, at the Department of Energy’s Oak Ridge National Laboratory, has been named a fellow of the American Nuclear Society.
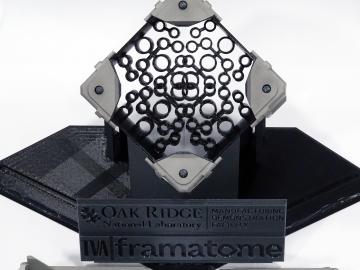
The Transformational Challenge Reactor, or TCR, a microreactor built using 3D printing and other new advanced technologies, could be operational by 2024.
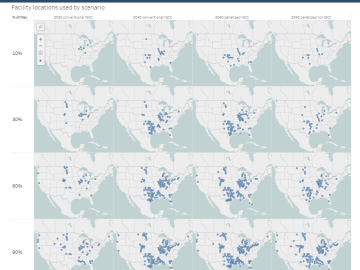
The combination of bioenergy with carbon capture and storage could cost-effectively sequester hundreds of millions of metric tons per year of carbon dioxide in the United States, making it a competitive solution for carbon management, according to a new analysis by ORNL scientists.
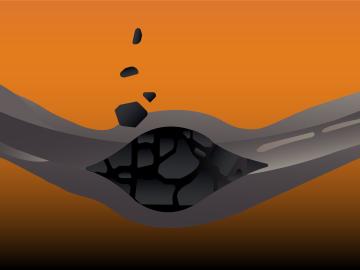
A developing method to gauge the occurrence of a nuclear reactor anomaly has the potential to save millions of dollars.
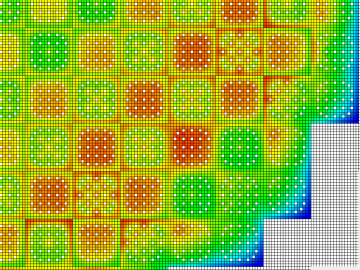
As CASL ends and transitions to VERA Users Group, ORNL looks at the history of the program and its impact on the nuclear industry.