Filter News
Area of Research
- (-) Clean Energy (15)
- (-) Materials for Computing (7)
- Advanced Manufacturing (2)
- Biology and Environment (11)
- Climate and Environmental Systems (1)
- Computational Biology (1)
- Computer Science (3)
- Fusion and Fission (1)
- Materials (41)
- National Security (5)
- Neutron Science (100)
- Nuclear Science and Technology (5)
- Quantum information Science (9)
- Supercomputing (35)
News Topics
- (-) Mercury (3)
- (-) Neutron Science (16)
- (-) Quantum Science (5)
- 3-D Printing/Advanced Manufacturing (80)
- Advanced Reactors (6)
- Artificial Intelligence (8)
- Big Data (5)
- Bioenergy (26)
- Biology (11)
- Biomedical (7)
- Biotechnology (4)
- Buildings (36)
- Chemical Sciences (18)
- Clean Water (8)
- Climate Change (21)
- Composites (17)
- Computer Science (30)
- Coronavirus (15)
- Critical Materials (9)
- Cybersecurity (8)
- Decarbonization (33)
- Energy Storage (72)
- Environment (54)
- Exascale Computing (2)
- Fossil Energy (2)
- Frontier (2)
- Fusion (1)
- Grid (40)
- High-Performance Computing (6)
- Hydropower (2)
- Isotopes (2)
- Machine Learning (7)
- Materials (43)
- Materials Science (38)
- Mathematics (2)
- Microelectronics (1)
- Microscopy (12)
- Molten Salt (1)
- Nanotechnology (14)
- National Security (6)
- Net Zero (3)
- Nuclear Energy (7)
- Partnerships (12)
- Physics (1)
- Polymers (14)
- Quantum Computing (1)
- Renewable Energy (1)
- Security (7)
- Simulation (4)
- Space Exploration (4)
- Statistics (1)
- Summit (5)
- Sustainable Energy (70)
- Transformational Challenge Reactor (3)
- Transportation (67)
Media Contacts
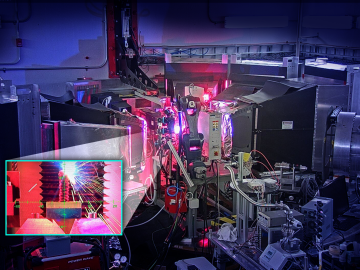
Using neutrons to see the additive manufacturing process at the atomic level, scientists have shown that they can measure strain in a material as it evolves and track how atoms move in response to stress.

Yarom Polsky, director of the Manufacturing Science Division, or MSD, at the Department of Energy’s Oak Ridge National Laboratory, has been elected a Fellow of the American Society of Mechanical Engineers, or ASME.
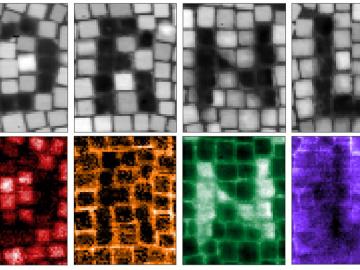
Drilling with the beam of an electron microscope, scientists at ORNL precisely machined tiny electrically conductive cubes that can interact with light and organized them in patterned structures that confine and relay light’s electromagnetic signal.
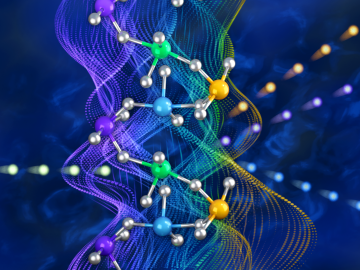
A discovery by Oak Ridge National Laboratory researchers may aid the design of materials that better manage heat.

A team led by the U.S. Department of Energy’s Oak Ridge National Laboratory demonstrated the viability of a “quantum entanglement witness” capable of proving the presence of entanglement between magnetic particles, or spins, in a quantum material.
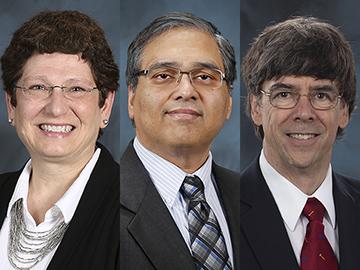
ASM International recently elected three researchers from ORNL as 2021 fellows. Selected were Beth Armstrong and Govindarajan Muralidharan, both from ORNL’s Material Sciences and Technology Division, and Andrew Payzant from the Neutron Scattering Division.
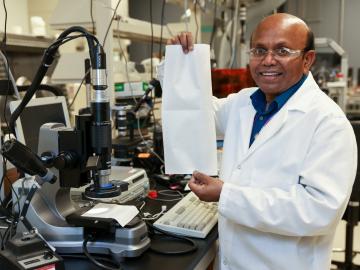
When COVID-19 was declared a pandemic in March 2020, Oak Ridge National Laboratory’s Parans Paranthaman suddenly found himself working from home like millions of others.
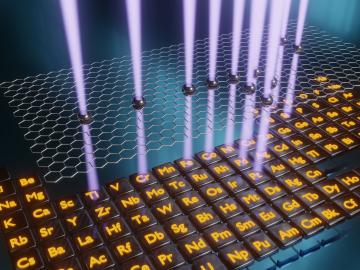
Oak Ridge National Laboratory scientists demonstrated that an electron microscope can be used to selectively remove carbon atoms from graphene’s atomically thin lattice and stitch transition-metal dopant atoms in their place.
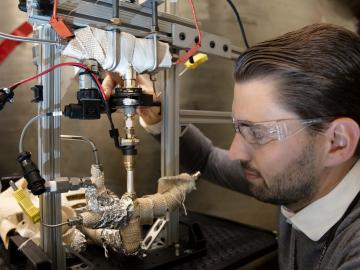
For a researcher who started out in mechanical engineering with a focus on engine combustion, Martin Wissink has learned a lot about neutrons on the job

The ExOne Company, the global leader in industrial sand and metal 3D printers using binder jetting technology, announced it has reached a commercial license agreement with Oak Ridge National Laboratory to 3D print parts in aluminum-infiltrated boron carbide.