Filter News
Area of Research
- (-) Advanced Manufacturing (6)
- (-) Computational Engineering (1)
- (-) National Security (6)
- Biology and Environment (26)
- Clean Energy (44)
- Computational Biology (1)
- Computer Science (4)
- Electricity and Smart Grid (1)
- Energy Frontier Research Centers (1)
- Functional Materials for Energy (2)
- Fusion and Fission (2)
- Fusion Energy (2)
- Isotopes (4)
- Materials (108)
- Materials Characterization (2)
- Materials for Computing (16)
- Materials Under Extremes (1)
- Neutron Science (32)
- Quantum information Science (9)
- Supercomputing (83)
News Topics
- (-) Materials (8)
- (-) Nanotechnology (1)
- (-) Quantum Science (1)
- (-) Summit (3)
- 3-D Printing/Advanced Manufacturing (24)
- Advanced Reactors (2)
- Artificial Intelligence (14)
- Big Data (7)
- Bioenergy (4)
- Biology (5)
- Biomedical (3)
- Biotechnology (1)
- Buildings (1)
- Chemical Sciences (2)
- Clean Water (1)
- Climate Change (6)
- Composites (3)
- Computer Science (23)
- Coronavirus (2)
- Cybersecurity (20)
- Decarbonization (2)
- Energy Storage (2)
- Environment (6)
- Exascale Computing (1)
- Frontier (1)
- Fusion (2)
- Grid (6)
- High-Performance Computing (5)
- Machine Learning (14)
- Materials Science (8)
- Mathematics (1)
- National Security (34)
- Neutron Science (6)
- Nuclear Energy (7)
- Partnerships (4)
- Physics (1)
- Security (11)
- Simulation (1)
- Space Exploration (1)
- Sustainable Energy (8)
- Transformational Challenge Reactor (1)
- Transportation (2)
Media Contacts

Scientists at ORNL have developed 3D-printed collimator techniques that can be used to custom design collimators that better filter out noise during different types of neutron scattering experiments
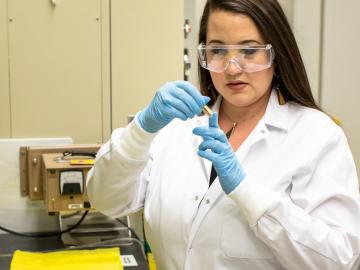
The word “exotic” may not spark thoughts of uranium, but Tyler Spano’s investigations of exotic phases of uranium are bringing new knowledge to the nuclear nonproliferation industry.
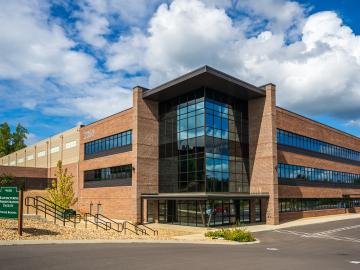
ORNL scientists will present new technologies available for licensing during the annual Technology Innovation Showcase. The event is 9 a.m. to 3 p.m. Thursday, June 16, at the Manufacturing Demonstration Facility at ORNL’s Hardin Valley campus.

ORNL researchers used the nation’s fastest supercomputer to map the molecular vibrations of an important but little-studied uranium compound produced during the nuclear fuel cycle for results that could lead to a cleaner, safer world.

Oak Ridge National Laboratory researchers determined that designing polymers specifically with upcycling in mind could reduce future plastic waste considerably and facilitate a circular economy where the material is used repeatedly.
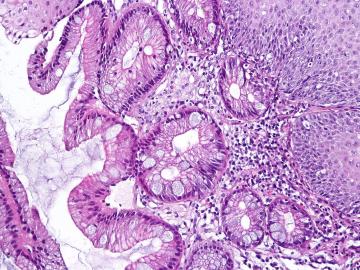
A team including researchers from the Department of Energy’s Oak Ridge National Laboratory has developed a digital tool to better monitor a condition known as Barrett’s esophagus, which affects more than 3 million people in the United States.
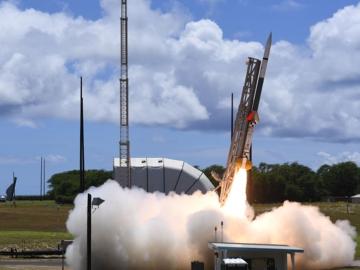
Oak Ridge National Laboratory researchers have developed a novel process to manufacture extreme heat resistant carbon-carbon composites. The performance of these materials will be tested in a U.S. Navy rocket that NASA will launch this fall.

A research team at Oak Ridge National Laboratory have 3D printed a thermal protection shield, or TPS, for a capsule that will launch with the Cygnus cargo spacecraft as part of the supply mission to the International Space Station.
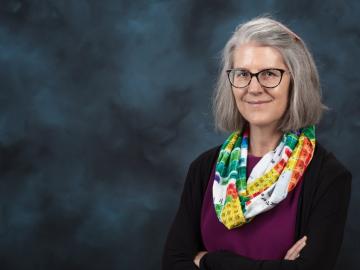
Deborah Frincke, one of the nation’s preeminent computer scientists and cybersecurity experts, serves as associate laboratory director of ORNL’s National Security Science Directorate. Credit: Carlos Jones/ORNL, U.S. Dept. of Energy

A team of Oak Ridge National Laboratory researchers demonstrated that an additively manufactured hot stamping die – a tool used to create car body components – cooled faster than those produced by conventional manufacturing methods.