Filter News
Area of Research
- (-) Advanced Manufacturing (6)
- (-) Neutron Science (14)
- (-) Supercomputing (15)
- Biology and Environment (12)
- Clean Energy (35)
- Electricity and Smart Grid (1)
- Functional Materials for Energy (2)
- Fusion and Fission (1)
- Fusion Energy (1)
- Isotopes (4)
- Materials (73)
- Materials Characterization (2)
- Materials for Computing (10)
- Materials Under Extremes (1)
- National Security (2)
News Topics
- (-) Materials (32)
- 3-D Printing/Advanced Manufacturing (28)
- Advanced Reactors (3)
- Artificial Intelligence (40)
- Big Data (20)
- Bioenergy (13)
- Biology (14)
- Biomedical (25)
- Biotechnology (2)
- Buildings (4)
- Chemical Sciences (6)
- Clean Water (2)
- Climate Change (17)
- Composites (4)
- Computer Science (98)
- Coronavirus (17)
- Critical Materials (3)
- Cybersecurity (9)
- Decarbonization (7)
- Energy Storage (14)
- Environment (28)
- Exascale Computing (22)
- Fossil Energy (1)
- Frontier (29)
- Fusion (3)
- Grid (5)
- High-Performance Computing (39)
- Isotopes (1)
- Machine Learning (17)
- Materials Science (37)
- Mathematics (1)
- Microscopy (8)
- Molten Salt (1)
- Nanotechnology (19)
- National Security (8)
- Net Zero (1)
- Neutron Science (101)
- Nuclear Energy (8)
- Partnerships (1)
- Physics (16)
- Polymers (3)
- Quantum Computing (19)
- Quantum Science (29)
- Security (6)
- Simulation (14)
- Software (1)
- Space Exploration (6)
- Summit (42)
- Sustainable Energy (15)
- Transformational Challenge Reactor (1)
- Transportation (10)
Media Contacts

A study led by researchers at ORNL could help make materials design as customizable as point-and-click.
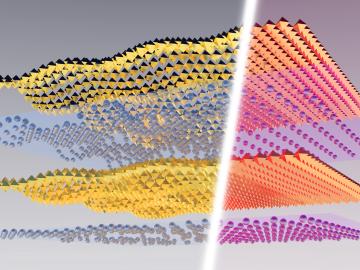
A study by researchers at the ORNL takes a fresh look at what could become the first step toward a new generation of solar batteries.
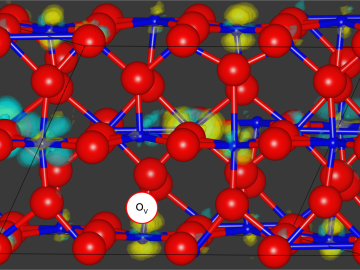
Neuromorphic devices — which emulate the decision-making processes of the human brain — show great promise for solving pressing scientific problems, but building physical systems to realize this potential presents researchers with a significant

Oak Ridge National Laboratory researchers determined that designing polymers specifically with upcycling in mind could reduce future plastic waste considerably and facilitate a circular economy where the material is used repeatedly.
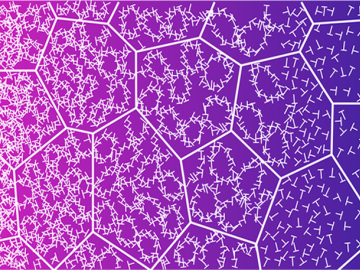
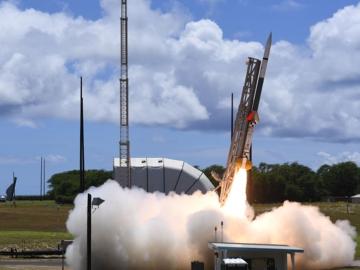
Oak Ridge National Laboratory researchers have developed a novel process to manufacture extreme heat resistant carbon-carbon composites. The performance of these materials will be tested in a U.S. Navy rocket that NASA will launch this fall.

A research team at Oak Ridge National Laboratory have 3D printed a thermal protection shield, or TPS, for a capsule that will launch with the Cygnus cargo spacecraft as part of the supply mission to the International Space Station.
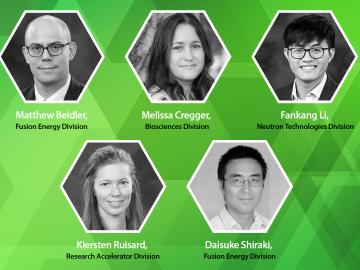
The Department of Energy’s Office of Science has selected five Oak Ridge National Laboratory scientists for Early Career Research Program awards.

A team of Oak Ridge National Laboratory researchers demonstrated that an additively manufactured hot stamping die – a tool used to create car body components – cooled faster than those produced by conventional manufacturing methods.

The ExOne Company, the global leader in industrial sand and metal 3D printers using binder jetting technology, announced it has reached a commercial license agreement with Oak Ridge National Laboratory to 3D print parts in aluminum-infiltrated boron carbide.