Filter News
Area of Research
- (-) Advanced Manufacturing (7)
- (-) Mathematics (1)
- (-) Neutron Science (5)
- Biology and Environment (12)
- Building Technologies (2)
- Clean Energy (51)
- Climate and Environmental Systems (1)
- Computational Engineering (2)
- Computer Science (10)
- Energy Sciences (2)
- Fusion and Fission (3)
- Fusion Energy (6)
- Isotopes (1)
- Materials (29)
- Materials for Computing (8)
- National Security (2)
- Nuclear Science and Technology (1)
- Quantum information Science (3)
- Supercomputing (18)
- Transportation Systems (1)
News Topics
- (-) Computer Science (1)
- (-) Energy Storage (2)
- (-) Fusion (1)
- (-) Materials Science (7)
- (-) Microscopy (1)
- (-) Sustainable Energy (3)
- 3-D Printing/Advanced Manufacturing (11)
- Advanced Reactors (1)
- Artificial Intelligence (1)
- Bioenergy (1)
- Biomedical (2)
- Chemical Sciences (1)
- Clean Water (1)
- Climate Change (1)
- Composites (3)
- Environment (2)
- Materials (7)
- Mathematics (1)
- Nanotechnology (1)
- Neutron Science (23)
- Nuclear Energy (2)
- Physics (1)
- Quantum Science (1)
- Space Exploration (2)
- Transportation (1)
Media Contacts
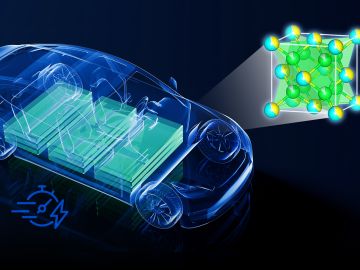
Currently, the biggest hurdle for electric vehicles, or EVs, is the development of advanced battery technology to extend driving range, safety and reliability.
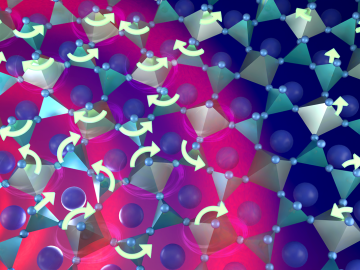
Warming a crystal of the mineral fresnoite, ORNL scientists discovered that excitations called phasons carried heat three times farther and faster than phonons, the excitations that usually carry heat through a material.

Oak Ridge National Laboratory researchers determined that designing polymers specifically with upcycling in mind could reduce future plastic waste considerably and facilitate a circular economy where the material is used repeatedly.
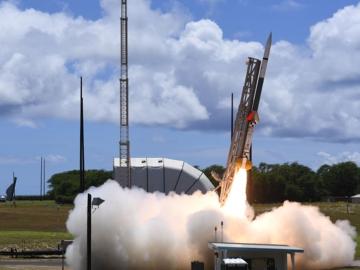
Oak Ridge National Laboratory researchers have developed a novel process to manufacture extreme heat resistant carbon-carbon composites. The performance of these materials will be tested in a U.S. Navy rocket that NASA will launch this fall.

A research team at Oak Ridge National Laboratory have 3D printed a thermal protection shield, or TPS, for a capsule that will launch with the Cygnus cargo spacecraft as part of the supply mission to the International Space Station.
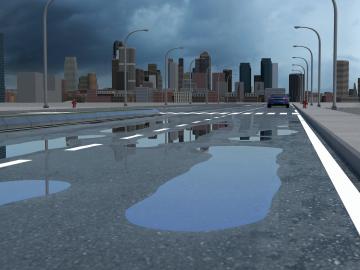
Researchers at Oak Ridge National Laboratory have identified a statistical relationship between the growth of cities and the spread of paved surfaces like roads and sidewalks. These impervious surfaces impede the flow of water into the ground, affecting the water cycle and, by extension, the climate.

Oak Ridge National Laboratory researchers have demonstrated that a new class of superalloys made of cobalt and nickel remains crack-free and defect-resistant in extreme heat, making them conducive for use in metal-based 3D printing applications.
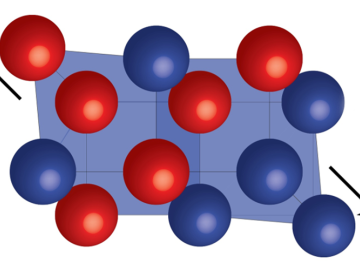
Pauling’s Rules is the standard model used to describe atomic arrangements in ordered materials. Neutron scattering experiments at Oak Ridge National Laboratory confirmed this approach can also be used to describe highly disordered materials.
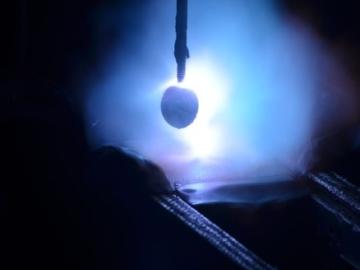
Researchers at Oak Ridge National Laboratory demonstrated that an additively manufactured polymer layer, when applied to carbon fiber reinforced plastic, or CFRP, can serve as an effective protector against aircraft lightning strikes.
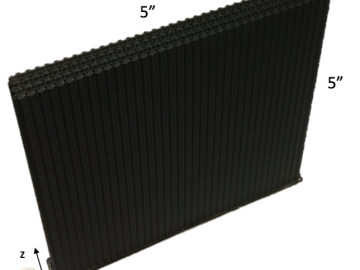
A team including Oak Ridge National Laboratory and University of Tennessee researchers demonstrated a novel 3D printing approach called Z-pinning that can increase the material’s strength and toughness by more than three and a half times compared to conventional additive manufacturing processes.