Filter News
Area of Research
- (-) Clean Energy (15)
- (-) National Security (1)
- (-) Neutron Science (3)
- (-) Nuclear Science and Technology (3)
- (-) Supercomputing (6)
- Advanced Manufacturing (3)
- Biological Systems (1)
- Biology and Environment (10)
- Computational Engineering (1)
- Computer Science (1)
- Isotopes (3)
- Materials (12)
- Materials for Computing (2)
- Mathematics (1)
- Quantum information Science (3)
News Topics
- (-) Bioenergy (3)
- (-) Composites (9)
- (-) Cybersecurity (1)
- (-) Isotopes (1)
- (-) Mathematics (1)
- (-) Polymers (7)
- (-) Quantum Science (4)
- (-) Space Exploration (5)
- 3-D Printing/Advanced Manufacturing (23)
- Advanced Reactors (5)
- Artificial Intelligence (3)
- Big Data (6)
- Biology (3)
- Biomedical (8)
- Biotechnology (1)
- Buildings (13)
- Chemical Sciences (3)
- Clean Water (4)
- Climate Change (7)
- Computer Science (23)
- Coronavirus (5)
- Critical Materials (7)
- Decarbonization (4)
- Energy Storage (24)
- Environment (18)
- Exascale Computing (1)
- Frontier (1)
- Fusion (2)
- Grid (16)
- High-Performance Computing (3)
- Hydropower (2)
- Machine Learning (3)
- Materials (16)
- Materials Science (13)
- Mercury (1)
- Microscopy (3)
- Molten Salt (3)
- Nanotechnology (3)
- Net Zero (1)
- Neutron Science (24)
- Nuclear Energy (11)
- Physics (1)
- Quantum Computing (4)
- Security (1)
- Simulation (2)
- Statistics (1)
- Summit (6)
- Sustainable Energy (28)
- Transportation (28)
Media Contacts
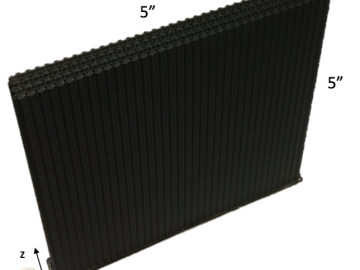
A team including Oak Ridge National Laboratory and University of Tennessee researchers demonstrated a novel 3D printing approach called Z-pinning that can increase the material’s strength and toughness by more than three and a half times compared to conventional additive manufacturing processes.
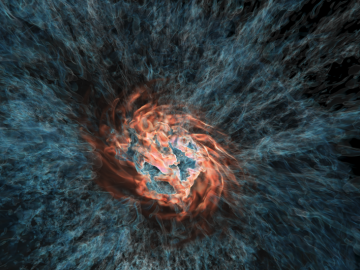
Using the Titan supercomputer at Oak Ridge National Laboratory, a team of astrophysicists created a set of galactic wind simulations of the highest resolution ever performed. The simulations will allow researchers to gather and interpret more accurate, detailed data that elucidates how galactic winds affect the formation and evolution of galaxies.

A team of researchers at Oak Ridge National Laboratory have demonstrated that designed synthetic polymers can serve as a high-performance binding material for next-generation lithium-ion batteries.

By automating the production of neptunium oxide-aluminum pellets, Oak Ridge National Laboratory scientists have eliminated a key bottleneck when producing plutonium-238 used by NASA to fuel deep space exploration.
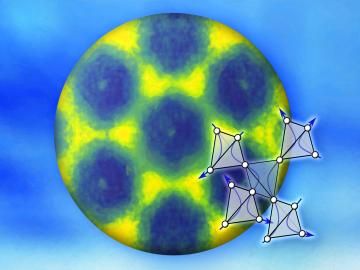
Researchers used neutron scattering at Oak Ridge National Laboratory’s Spallation Neutron Source to investigate bizarre magnetic behavior, believed to be a possible quantum spin liquid rarely found in a three-dimensional material. QSLs are exotic states of matter where magnetism continues to fluctuate at low temperatures instead of “freezing” into aligned north and south poles as with traditional magnets.
Scientists at Oak Ridge National Laboratory have conducted a series of breakthrough experimental and computational studies that cast doubt on a 40-year-old theory describing how polymers in plastic materials behave during processing.
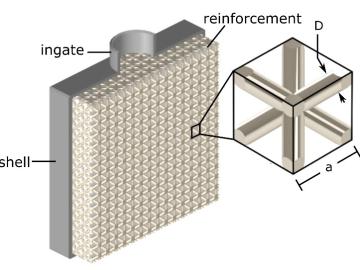
A new manufacturing method created by Oak Ridge National Laboratory and Rice University combines 3D printing with traditional casting to produce damage-tolerant components composed of multiple materials. Composite components made by pouring an aluminum alloy over a printed steel lattice showed an order of magnitude greater damage tolerance than aluminum alone.