Filter News
Area of Research
- (-) Clean Energy (56)
- (-) Fusion Energy (2)
- Advanced Manufacturing (8)
- Biological Systems (1)
- Biology and Environment (16)
- Computational Biology (1)
- Computer Science (2)
- Electricity and Smart Grid (1)
- Isotopes (1)
- Materials (33)
- Materials for Computing (9)
- National Security (3)
- Neutron Science (9)
- Nuclear Science and Technology (1)
- Quantum information Science (1)
- Sensors and Controls (1)
- Supercomputing (7)
- Transportation Systems (2)
News Topics
- (-) Bioenergy (2)
- (-) Biomedical (1)
- (-) Grid (15)
- (-) Materials (12)
- (-) Materials Science (11)
- (-) Mercury (1)
- (-) Transportation (26)
- 3-D Printing/Advanced Manufacturing (24)
- Advanced Reactors (6)
- Artificial Intelligence (1)
- Big Data (1)
- Biology (2)
- Biotechnology (1)
- Buildings (13)
- Chemical Sciences (1)
- Clean Water (4)
- Climate Change (6)
- Composites (9)
- Computer Science (11)
- Coronavirus (2)
- Critical Materials (4)
- Decarbonization (4)
- Energy Storage (21)
- Environment (15)
- Frontier (1)
- Fusion (6)
- High-Performance Computing (1)
- Hydropower (2)
- Machine Learning (2)
- Mathematics (1)
- Microscopy (2)
- Nanotechnology (1)
- Net Zero (1)
- Nuclear Energy (6)
- Polymers (5)
- Simulation (1)
- Space Exploration (2)
- Statistics (1)
- Summit (1)
- Sustainable Energy (28)
Media Contacts

Researchers at Oak Ridge National Laboratory have developed a nationwide modeling tool to help infrastructure planners decide where and when to locate electric vehicle charging stations along interstate highways. The goal is to encourage the adoption of EVs for cross-country travel.
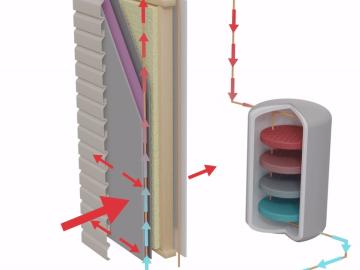
Researchers at Oak Ridge National Laboratory have developed a novel envelope system that diverts heat or coolness away from a building and stores it for future use.
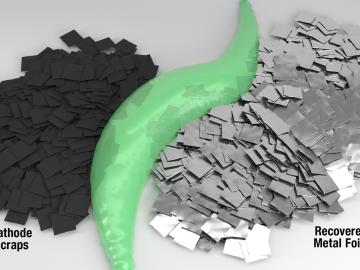
Scientists at Oak Ridge National Laboratory have developed a solvent that results in a more environmentally friendly process to recover valuable materials from used lithium-ion batteries, supports a stable domestic supply chain for new batteries
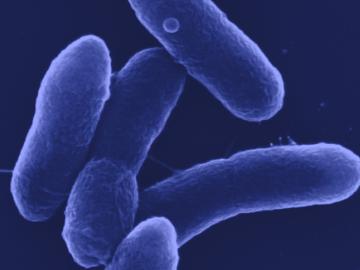
A research team led by Oak Ridge National Laboratory bioengineered a microbe to efficiently turn waste into itaconic acid, an industrial chemical used in plastics and paints.
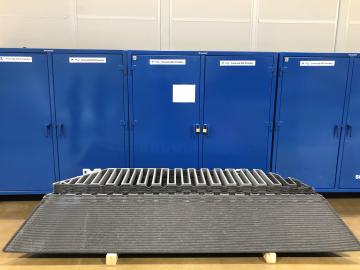
Oak Ridge National Laboratory researchers, in collaboration with Cincinnati Inc., demonstrated the potential for using multimaterials and recycled composites in large-scale applications by 3D printing a mold that replicated a single facet of a
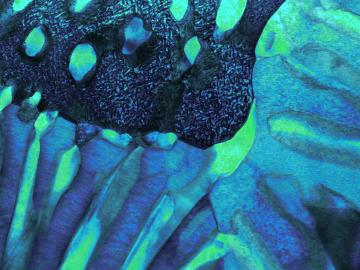
Oak Ridge National Laboratory scientists proved molybdenum titanium carbide, a refractory metal alloy that can withstand extreme temperature environments, can also be crack free and dense when produced with electron beam powder bed fusion.
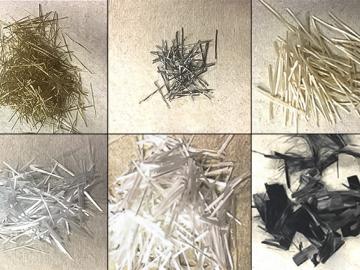
A team of researchers at Oak Ridge National Laboratory and the University of Tennessee have developed a concrete mix that demonstrated high early strength within six hours of mixing, potentially doubling the production capacity for the precast industry.
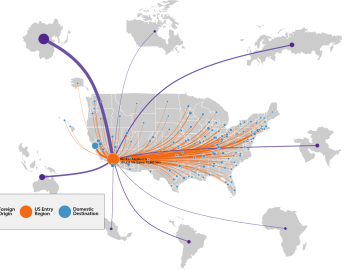
A newly released dataset that tracks the movement of everything from food to gasoline across the United States by air, water, truck, rail and pipeline showed the value and tonnage of those goods rose significantly between 2012 and 2017.

Scientists at Oak Ridge National Laboratory successfully demonstrated a technique to heal dendrites that formed in a solid electrolyte, resolving an issue that can hamper the performance of high energy-density, solid-state batteries.

A team of Oak Ridge National Laboratory researchers demonstrated that an additively manufactured hot stamping die – a tool used to create car body components – cooled faster than those produced by conventional manufacturing methods.