
Filter News
Area of Research
News Topics
- (-) Advanced Reactors (3)
- (-) Clean Water (2)
- (-) Composites (2)
- (-) Cybersecurity (1)
- (-) Energy Storage (7)
- (-) Exascale Computing (2)
- (-) Neutron Science (9)
- (-) Polymers (4)
- (-) Space Exploration (1)
- 3-D Printing/Advanced Manufacturing (7)
- Artificial Intelligence (5)
- Big Data (2)
- Bioenergy (2)
- Biomedical (2)
- Buildings (1)
- Chemical Sciences (8)
- Computer Science (9)
- Coronavirus (1)
- Decarbonization (2)
- Environment (8)
- Frontier (1)
- Fusion (14)
- Grid (2)
- High-Performance Computing (3)
- Isotopes (6)
- ITER (2)
- Machine Learning (2)
- Materials (19)
- Materials Science (17)
- Mathematics (1)
- Microscopy (6)
- Nanotechnology (8)
- Net Zero (1)
- Nuclear Energy (26)
- Partnerships (3)
- Physics (12)
- Quantum Computing (1)
- Security (2)
- Simulation (2)
- Summit (1)
- Sustainable Energy (5)
- Transformational Challenge Reactor (2)
- Transportation (5)
Media Contacts
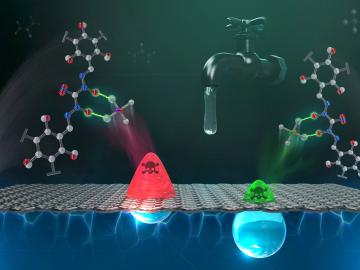
Researchers at ORNL are tackling a global water challenge with a unique material designed to target not one, but two toxic, heavy metal pollutants for simultaneous removal.
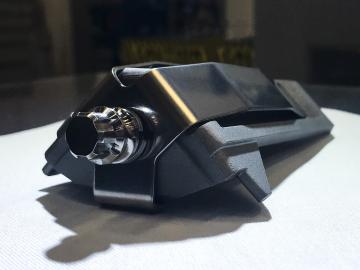
Four first-of-a-kind 3D-printed fuel assembly brackets, produced at the Department of Energy’s Manufacturing Demonstration Facility at Oak Ridge National Laboratory, have been installed and are now under routine operating
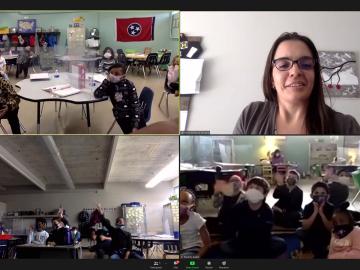
Twenty-seven ORNL researchers Zoomed into 11 middle schools across Tennessee during the annual Engineers Week in February. East Tennessee schools throughout Oak Ridge and Roane, Sevier, Blount and Loudon counties participated, with three West Tennessee schools joining in.

On Feb. 18, the world will be watching as NASA’s Perseverance rover makes its final descent into Jezero Crater on the surface of Mars. Mars 2020 is the first NASA mission that uses plutonium-238 produced at the Department of Energy’s Oak Ridge National Laboratory.
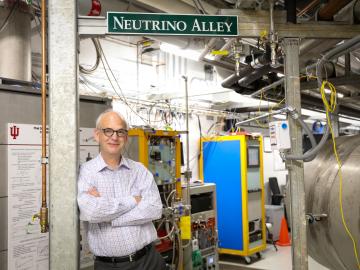
Marcel Demarteau is director of the Physics Division at the Department of Energy’s Oak Ridge National Laboratory. For topics from nuclear structure to astrophysics, he shapes ORNL’s physics research agenda.
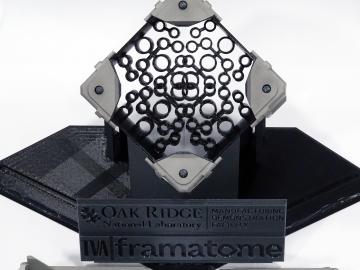
The Transformational Challenge Reactor, or TCR, a microreactor built using 3D printing and other new advanced technologies, could be operational by 2024.
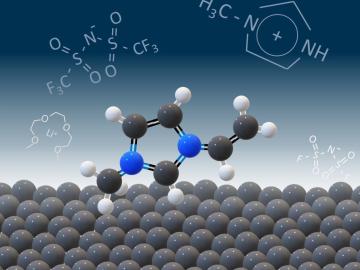
Scientists seeking ways to improve a battery’s ability to hold a charge longer, using advanced materials that are safe, stable and efficient, have determined that the materials themselves are only part of the solution.
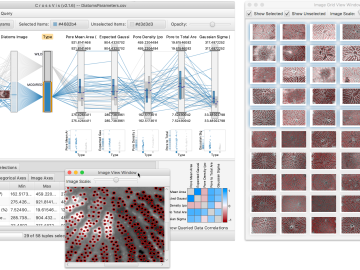
From materials science and earth system modeling to quantum information science and cybersecurity, experts in many fields run simulations and conduct experiments to collect the abundance of data necessary for scientific progress.
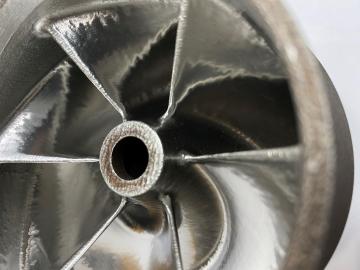
Scientists at the Department of Energy Manufacturing Demonstration Facility at ORNL have their eyes on the prize: the Transformational Challenge Reactor, or TCR, a microreactor built using 3D printing and other new approaches that will be up and running by 2023.
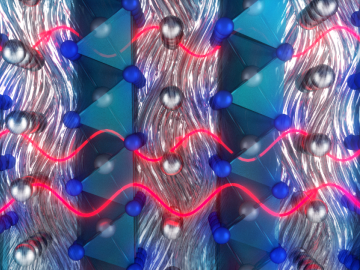
Research by an international team led by Duke University and the Department of Energy’s Oak Ridge National Laboratory scientists could speed the way to safer rechargeable batteries for consumer electronics such as laptops and cellphones.