
Filter News
Area of Research
- (-) Clean Energy (33)
- (-) Nuclear Science and Technology (8)
- Advanced Manufacturing (2)
- Biological Systems (1)
- Biology and Environment (28)
- Computational Biology (1)
- Computer Science (2)
- Fusion and Fission (6)
- Isotopes (17)
- Materials (34)
- Materials for Computing (7)
- National Security (14)
- Neutron Science (37)
- Quantum information Science (1)
- Supercomputing (56)
News Topics
- (-) Advanced Reactors (6)
- (-) Artificial Intelligence (2)
- (-) Biomedical (2)
- (-) Computer Science (8)
- (-) Energy Storage (20)
- (-) Isotopes (2)
- (-) Mercury (1)
- (-) Neutron Science (3)
- (-) Physics (1)
- (-) Space Exploration (2)
- 3-D Printing/Advanced Manufacturing (24)
- Bioenergy (10)
- Biology (4)
- Biotechnology (1)
- Buildings (11)
- Chemical Sciences (3)
- Clean Water (3)
- Climate Change (8)
- Composites (2)
- Coronavirus (6)
- Cybersecurity (5)
- Decarbonization (15)
- Environment (18)
- Fossil Energy (1)
- Fusion (6)
- Grid (13)
- High-Performance Computing (2)
- Materials (5)
- Materials Science (6)
- Mathematics (1)
- Microelectronics (1)
- Microscopy (2)
- Molten Salt (1)
- Nanotechnology (2)
- National Security (1)
- Net Zero (1)
- Nuclear Energy (18)
- Partnerships (4)
- Polymers (1)
- Quantum Science (1)
- Security (3)
- Simulation (1)
- Summit (2)
- Sustainable Energy (14)
- Transformational Challenge Reactor (2)
- Transportation (17)
Media Contacts
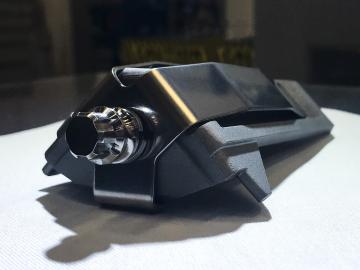
Four first-of-a-kind 3D-printed fuel assembly brackets, produced at the Department of Energy’s Manufacturing Demonstration Facility at Oak Ridge National Laboratory, have been installed and are now under routine operating
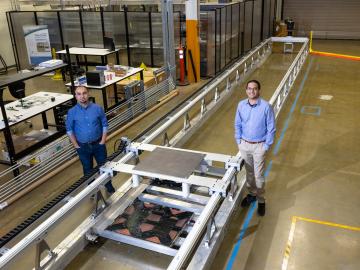
Consumer buy-in is key to the future of a decarbonized transportation sector in which electric vehicles largely replace today’s conventionally fueled cars and trucks.
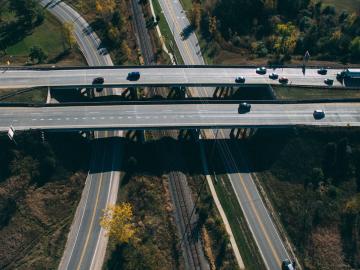
Through a consortium of Department of Energy national laboratories, ORNL scientists are applying their expertise to provide solutions that enable the commercialization of emission-free hydrogen fuel cell technology for heavy-duty
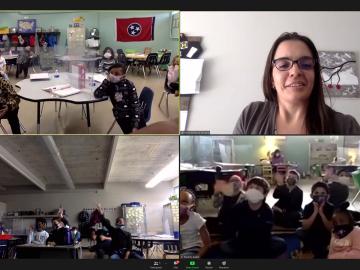
Twenty-seven ORNL researchers Zoomed into 11 middle schools across Tennessee during the annual Engineers Week in February. East Tennessee schools throughout Oak Ridge and Roane, Sevier, Blount and Loudon counties participated, with three West Tennessee schools joining in.

The ExOne Company, the global leader in industrial sand and metal 3D printers using binder jetting technology, announced it has reached a commercial license agreement with Oak Ridge National Laboratory to 3D print parts in aluminum-infiltrated boron carbide.
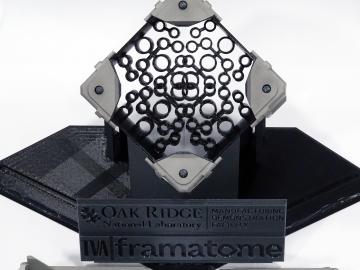
The Transformational Challenge Reactor, or TCR, a microreactor built using 3D printing and other new advanced technologies, could be operational by 2024.
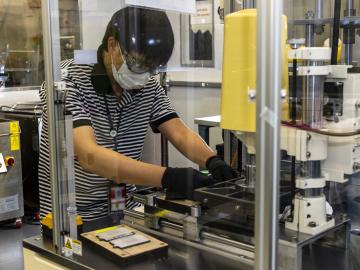
Soteria Battery Innovation Group has exclusively licensed and optioned a technology developed by Oak Ridge National Laboratory designed to eliminate thermal runaway in lithium ion batteries due to mechanical damage.
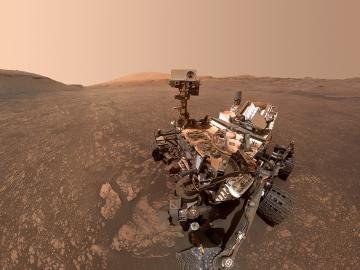
Radioactive isotopes power some of NASA’s best-known spacecraft. But predicting how radiation emitted from these isotopes might affect nearby materials is tricky
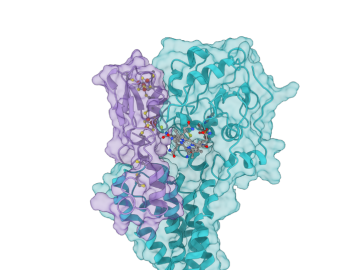
A team led by ORNL created a computational model of the proteins responsible for the transformation of mercury to toxic methylmercury, marking a step forward in understanding how the reaction occurs and how mercury cycles through the environment.
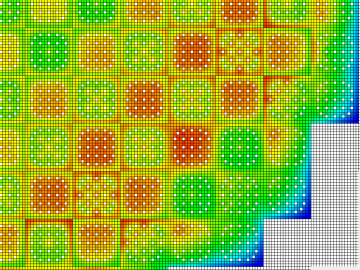
As CASL ends and transitions to VERA Users Group, ORNL looks at the history of the program and its impact on the nuclear industry.