Filter News
Area of Research
- (-) Clean Energy (50)
- (-) Nuclear Science and Technology (9)
- Advanced Manufacturing (2)
- Biological Systems (1)
- Biology and Environment (29)
- Computational Biology (1)
- Computer Science (2)
- Electricity and Smart Grid (1)
- Fusion and Fission (16)
- Fusion Energy (5)
- Isotopes (4)
- Materials (35)
- Materials for Computing (7)
- National Security (17)
- Neutron Science (38)
- Quantum information Science (1)
- Supercomputing (57)
News Topics
- (-) Artificial Intelligence (2)
- (-) Biomedical (2)
- (-) Computer Science (8)
- (-) Energy Storage (20)
- (-) Fusion (6)
- (-) Grid (13)
- (-) Materials Science (6)
- (-) Mercury (1)
- (-) Neutron Science (3)
- (-) Transportation (17)
- 3-D Printing/Advanced Manufacturing (24)
- Advanced Reactors (6)
- Bioenergy (10)
- Biology (4)
- Biotechnology (1)
- Buildings (11)
- Chemical Sciences (3)
- Clean Water (3)
- Climate Change (8)
- Composites (2)
- Coronavirus (6)
- Cybersecurity (5)
- Decarbonization (15)
- Environment (18)
- Fossil Energy (1)
- High-Performance Computing (2)
- Isotopes (2)
- Materials (5)
- Mathematics (1)
- Microelectronics (1)
- Microscopy (2)
- Molten Salt (1)
- Nanotechnology (2)
- National Security (1)
- Net Zero (1)
- Nuclear Energy (18)
- Partnerships (4)
- Physics (1)
- Polymers (1)
- Quantum Science (1)
- Security (3)
- Simulation (1)
- Space Exploration (2)
- Summit (2)
- Sustainable Energy (14)
- Transformational Challenge Reactor (2)
Media Contacts
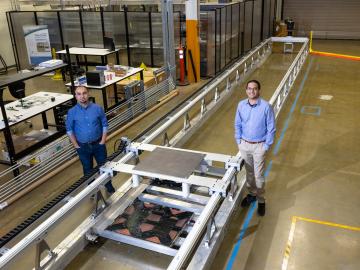
Consumer buy-in is key to the future of a decarbonized transportation sector in which electric vehicles largely replace today’s conventionally fueled cars and trucks.
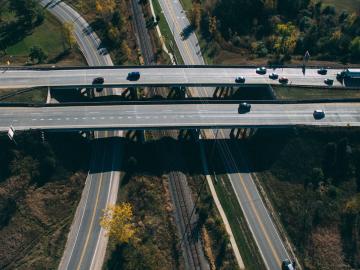
Through a consortium of Department of Energy national laboratories, ORNL scientists are applying their expertise to provide solutions that enable the commercialization of emission-free hydrogen fuel cell technology for heavy-duty
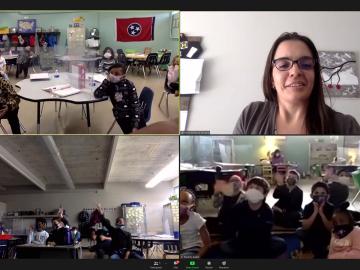
Twenty-seven ORNL researchers Zoomed into 11 middle schools across Tennessee during the annual Engineers Week in February. East Tennessee schools throughout Oak Ridge and Roane, Sevier, Blount and Loudon counties participated, with three West Tennessee schools joining in.

The ExOne Company, the global leader in industrial sand and metal 3D printers using binder jetting technology, announced it has reached a commercial license agreement with Oak Ridge National Laboratory to 3D print parts in aluminum-infiltrated boron carbide.
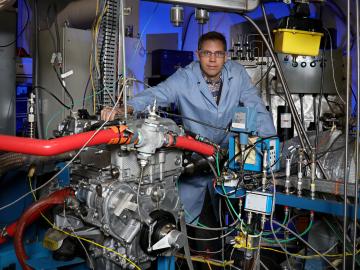
As ORNL’s fuel properties technical lead for the U.S. Department of Energy’s Co-Optimization of Fuel and Engines, or Co-Optima, initiative, Jim Szybist has been on a quest for the past few years to identify the most significant indicators for predicting how a fuel will perform in engines designed for light-duty vehicles such as passenger cars and pickup trucks.
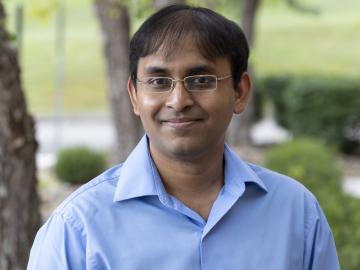
Planning for a digitized, sustainable smart power grid is a challenge to which Suman Debnath is using not only his own applied mathematics expertise, but also the wider communal knowledge made possible by his revival of a local chapter of the IEEE professional society.
A collaboration between the ORNL and a Florida-based medical device manufacturer has led to the addition of 500 jobs in the Miami area to support the mass production of N95 respirator masks.
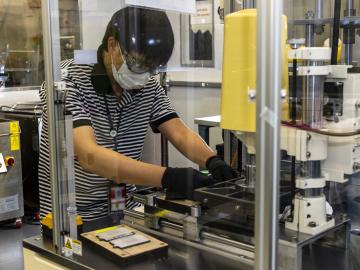
Soteria Battery Innovation Group has exclusively licensed and optioned a technology developed by Oak Ridge National Laboratory designed to eliminate thermal runaway in lithium ion batteries due to mechanical damage.
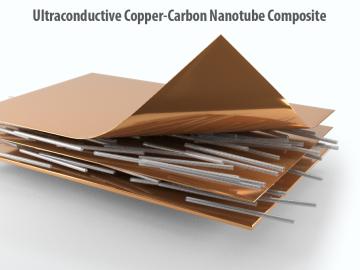
Scientists at Oak Ridge National Laboratory used new techniques to create a composite that increases the electrical current capacity of copper wires, providing a new material that can be scaled for use in ultra-efficient, power-dense electric vehicle traction motors.

The inside of future nuclear fusion energy reactors will be among the harshest environments ever produced on Earth. What’s strong enough to protect the inside of a fusion reactor from plasma-produced heat fluxes akin to space shuttles reentering Earth’s atmosphere?