Filter News
Area of Research
- (-) Fusion and Fission (4)
- (-) Materials (16)
- (-) Nuclear Science and Technology (8)
- Advanced Manufacturing (3)
- Biological Systems (1)
- Biology and Environment (17)
- Clean Energy (44)
- Computational Biology (1)
- Isotopes (17)
- Materials for Computing (2)
- National Security (2)
- Neutron Science (10)
- Supercomputing (9)
News Topics
- (-) 3-D Printing/Advanced Manufacturing (8)
- (-) Advanced Reactors (6)
- (-) Biomedical (2)
- (-) Energy Storage (7)
- (-) Isotopes (7)
- (-) Molten Salt (1)
- (-) Space Exploration (2)
- Artificial Intelligence (5)
- Big Data (2)
- Bioenergy (2)
- Buildings (1)
- Chemical Sciences (8)
- Clean Water (2)
- Composites (2)
- Computer Science (10)
- Coronavirus (2)
- Cybersecurity (1)
- Decarbonization (2)
- Environment (8)
- Exascale Computing (2)
- Frontier (1)
- Fusion (20)
- Grid (2)
- High-Performance Computing (3)
- ITER (2)
- Machine Learning (2)
- Materials (19)
- Materials Science (17)
- Mathematics (1)
- Microscopy (6)
- Nanotechnology (8)
- Net Zero (1)
- Neutron Science (10)
- Nuclear Energy (38)
- Partnerships (3)
- Physics (13)
- Polymers (4)
- Quantum Computing (1)
- Security (2)
- Simulation (2)
- Summit (1)
- Sustainable Energy (5)
- Transformational Challenge Reactor (3)
- Transportation (5)
Media Contacts
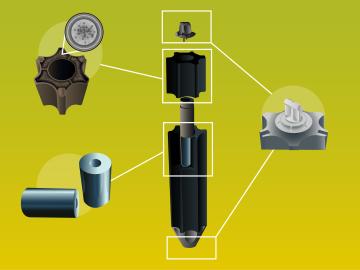
It’s a new type of nuclear reactor core. And the materials that will make it up are novel — products of Oak Ridge National Laboratory’s advanced materials and manufacturing technologies.
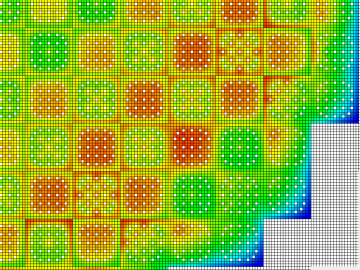
As CASL ends and transitions to VERA Users Group, ORNL looks at the history of the program and its impact on the nuclear industry.
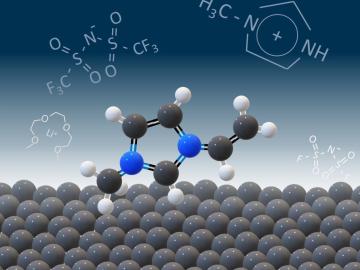
Scientists seeking ways to improve a battery’s ability to hold a charge longer, using advanced materials that are safe, stable and efficient, have determined that the materials themselves are only part of the solution.
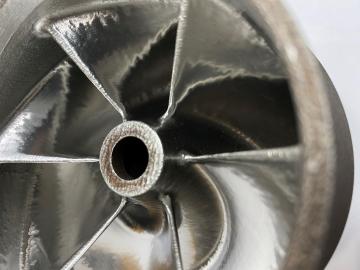
Scientists at the Department of Energy Manufacturing Demonstration Facility at ORNL have their eyes on the prize: the Transformational Challenge Reactor, or TCR, a microreactor built using 3D printing and other new approaches that will be up and running by 2023.
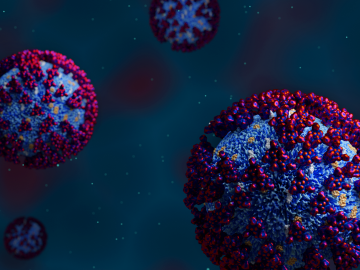
In the race to identify solutions to the COVID-19 pandemic, researchers at the Department of Energy’s Oak Ridge National Laboratory are joining the fight by applying expertise in computational science, advanced manufacturing, data science and neutron science.
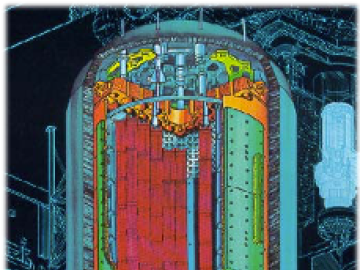
A software package, 10 years in the making, that can predict the behavior of nuclear reactors’ cores with stunning accuracy has been licensed commercially for the first time.
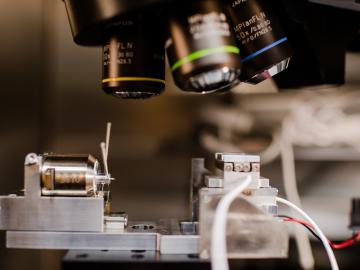
The formation of lithium dendrites is still a mystery, but materials engineers study the conditions that enable dendrites and how to stop them.
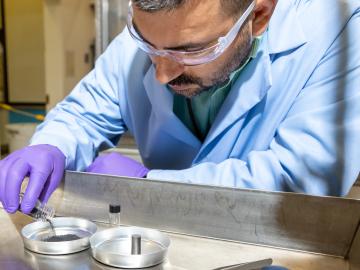
Ask Tyler Gerczak to find a negative in working at the Department of Energy’s Oak Ridge National Laboratory, and his only complaint is the summer weather. It is not as forgiving as the summers in Pulaski, Wisconsin, his hometown.
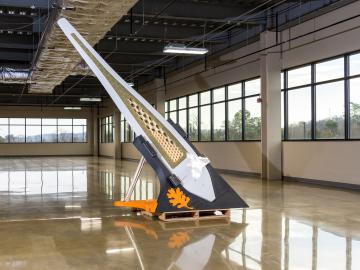
In the shifting landscape of global manufacturing, American ingenuity is once again giving U.S companies an edge with radical productivity improvements as a result of advanced materials and robotic systems developed at the Department of Energy’s Manufacturing Demonstration Facility (MDF) at Oak Ridge National Laboratory.
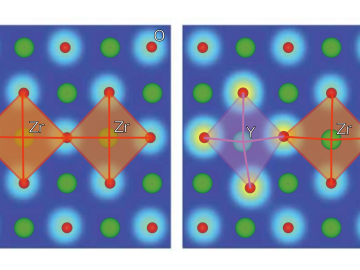
Ionic conduction involves the movement of ions from one location to another inside a material. The ions travel through point defects, which are irregularities in the otherwise consistent arrangement of atoms known as the crystal lattice. This sometimes sluggish process can limit the performance and efficiency of fuel cells, batteries, and other energy storage technologies.