Filter News
Area of Research
News Type
News Topics
- (-) Advanced Reactors (2)
- (-) Clean Water (13)
- (-) Composites (3)
- (-) Cybersecurity (5)
- (-) Space Exploration (2)
- 3-D Printing/Advanced Manufacturing (27)
- Artificial Intelligence (10)
- Big Data (8)
- Bioenergy (37)
- Biology (46)
- Biomedical (15)
- Biotechnology (7)
- Buildings (14)
- Chemical Sciences (7)
- Climate Change (30)
- Computer Science (21)
- Coronavirus (13)
- Critical Materials (1)
- Decarbonization (30)
- Energy Storage (26)
- Environment (77)
- Exascale Computing (4)
- Fossil Energy (2)
- Frontier (3)
- Grid (15)
- High-Performance Computing (13)
- Hydropower (5)
- Machine Learning (7)
- Materials (10)
- Materials Science (14)
- Mathematics (4)
- Mercury (7)
- Microelectronics (1)
- Microscopy (10)
- Nanotechnology (6)
- National Security (4)
- Net Zero (2)
- Neutron Science (35)
- Nuclear Energy (3)
- Partnerships (4)
- Physics (2)
- Polymers (3)
- Quantum Computing (1)
- Quantum Science (2)
- Renewable Energy (1)
- Security (4)
- Simulation (9)
- Summit (9)
- Sustainable Energy (30)
- Transportation (21)
Media Contacts
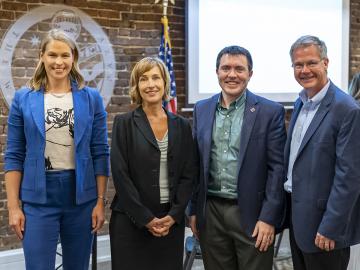
A crowd of investors and supporters turned out for last week’s Innovation Crossroads Showcase at the Knoxville Chamber as part of Innov865 Week. Sponsored by ORNL and the Tennessee Advanced Energy Business Council, the event celebrated deep-tech entrepreneurs and the Oak Ridge Corridor as a growing energy innovation hub for the nation.

Chemical and environmental engineer Samarthya Bhagia is focused on achieving carbon neutrality and a circular economy by designing new plant-based materials for a range of applications from energy storage devices and sensors to environmentally friendly bioplastics.
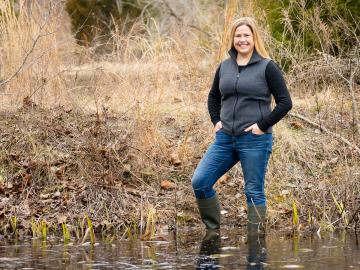
Spanning no less than three disciplines, Marie Kurz’s title — hydrogeochemist — already gives you a sense of the collaborative, interdisciplinary nature of her research at ORNL.
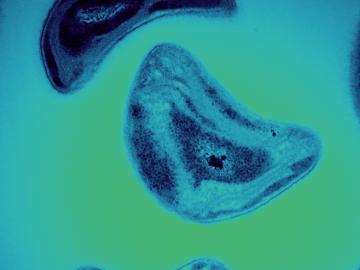
A team led by ORNL and the University of Michigan have discovered that certain bacteria can steal an essential compound from other microbes to break down methane and toxic methylmercury in the environment.
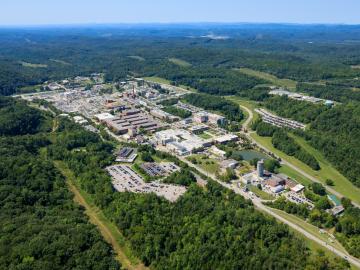
Anyone familiar with ORNL knows it’s a hub for world-class science. The nearly 33,000-acre space surrounding the lab is less known, but also unique.
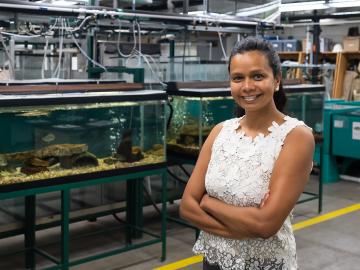
Moving to landlocked Tennessee isn’t an obvious choice for most scientists with new doctorate degrees in coastal oceanography.
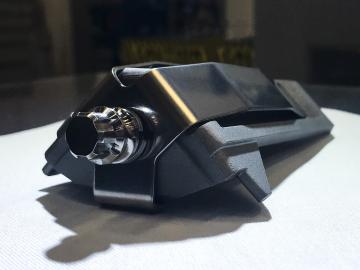
Four first-of-a-kind 3D-printed fuel assembly brackets, produced at the Department of Energy’s Manufacturing Demonstration Facility at Oak Ridge National Laboratory, have been installed and are now under routine operating
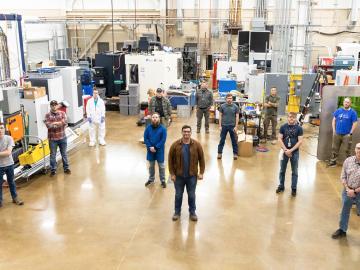
The University of Texas at San Antonio (UTSA) has formally launched the Cybersecurity Manufacturing Innovation Institute (CyManII), a $111 million public-private partnership.
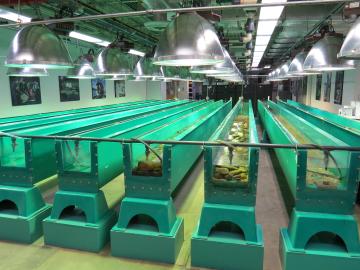
New capabilities and equipment recently installed at the Department of Energy’s Oak Ridge National Laboratory are bringing a creek right into the lab to advance understanding of mercury pollution and accelerate solutions.
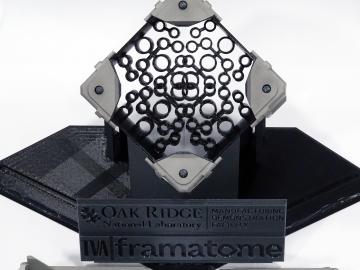
The Transformational Challenge Reactor, or TCR, a microreactor built using 3D printing and other new advanced technologies, could be operational by 2024.