Filter News
Area of Research
- (-) Clean Energy (76)
- (-) Neutron Science (17)
- Advanced Manufacturing (14)
- Biological Systems (2)
- Biology and Environment (78)
- Building Technologies (1)
- Climate and Environmental Systems (1)
- Computational Biology (2)
- Fusion and Fission (6)
- Fusion Energy (1)
- Isotopes (20)
- Materials (50)
- Materials for Computing (7)
- National Security (13)
- Nuclear Science and Technology (8)
- Quantum information Science (3)
- Supercomputing (40)
News Type
News Topics
- (-) 3-D Printing/Advanced Manufacturing (50)
- (-) Bioenergy (15)
- (-) Biology (7)
- (-) Biomedical (10)
- (-) Cybersecurity (5)
- (-) Mercury (2)
- (-) Microscopy (6)
- (-) Physics (2)
- (-) Quantum Computing (1)
- (-) Space Exploration (5)
- Advanced Reactors (2)
- Artificial Intelligence (8)
- Big Data (3)
- Biotechnology (2)
- Buildings (27)
- Chemical Sciences (6)
- Clean Water (9)
- Climate Change (14)
- Composites (11)
- Computer Science (22)
- Coronavirus (11)
- Critical Materials (5)
- Decarbonization (23)
- Energy Storage (48)
- Environment (39)
- Fossil Energy (2)
- Grid (30)
- High-Performance Computing (4)
- Hydropower (2)
- Machine Learning (5)
- Materials (24)
- Materials Science (24)
- Mathematics (3)
- Microelectronics (1)
- Nanotechnology (6)
- National Security (2)
- Net Zero (2)
- Neutron Science (58)
- Nuclear Energy (5)
- Partnerships (4)
- Polymers (7)
- Quantum Science (3)
- Security (4)
- Simulation (2)
- Statistics (1)
- Summit (4)
- Sustainable Energy (43)
- Transportation (48)
Media Contacts
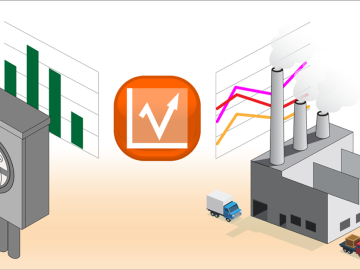
Researchers at ORNL have developed an online tool that offers industrial plants an easier way to track and download information about their energy footprint and carbon emissions.
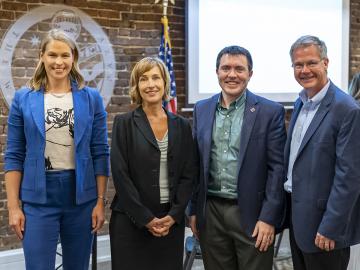
A crowd of investors and supporters turned out for last week’s Innovation Crossroads Showcase at the Knoxville Chamber as part of Innov865 Week. Sponsored by ORNL and the Tennessee Advanced Energy Business Council, the event celebrated deep-tech entrepreneurs and the Oak Ridge Corridor as a growing energy innovation hub for the nation.
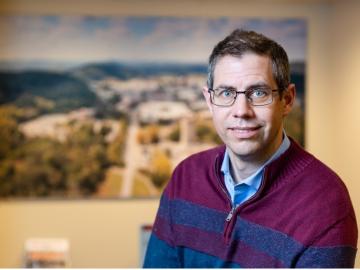
What’s getting Jim Szybist fired up these days? It’s the opportunity to apply his years of alternative fuel combustion and thermodynamics research to the challenge of cleaning up the hard-to-decarbonize, heavy-duty mobility sector — from airplanes to locomotives to ships and massive farm combines.
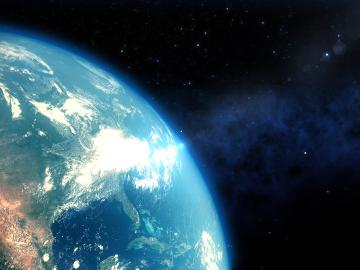
Tackling the climate crisis and achieving an equitable clean energy future are among the biggest challenges of our time.

When Andrew Sutton arrived at ORNL in late 2020, he knew the move would be significant in more ways than just a change in location.

Bruce Warmack has been fascinated by science since his mother finally let him have a chemistry set at the age of nine. He’d been pestering her for one since he was six.

A team led by the U.S. Department of Energy’s Oak Ridge National Laboratory demonstrated the viability of a “quantum entanglement witness” capable of proving the presence of entanglement between magnetic particles, or spins, in a quantum material.
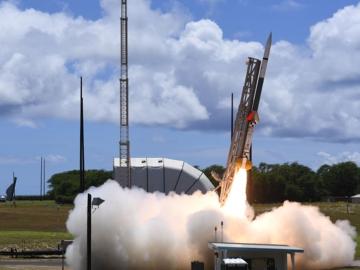
Oak Ridge National Laboratory researchers have developed a novel process to manufacture extreme heat resistant carbon-carbon composites. The performance of these materials will be tested in a U.S. Navy rocket that NASA will launch this fall.
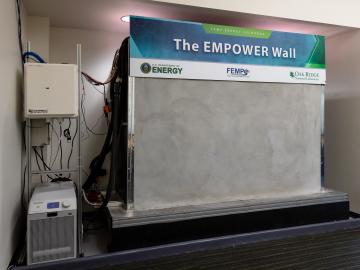
Oak Ridge National Laboratory researchers demonstrated that cooling cost savings could be achieved with a 3D printed concrete smart wall following a three-month field test.
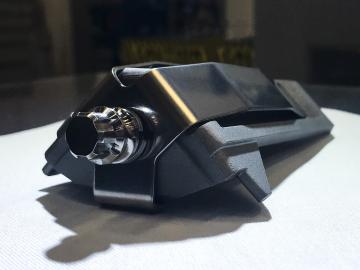
Four first-of-a-kind 3D-printed fuel assembly brackets, produced at the Department of Energy’s Manufacturing Demonstration Facility at Oak Ridge National Laboratory, have been installed and are now under routine operating