Filter News
Area of Research
News Topics
- (-) Advanced Reactors (3)
- (-) Artificial Intelligence (5)
- (-) Bioenergy (2)
- (-) Security (2)
- (-) Transportation (5)
- 3-D Printing/Advanced Manufacturing (7)
- Big Data (2)
- Biomedical (2)
- Buildings (1)
- Chemical Sciences (8)
- Clean Water (2)
- Composites (2)
- Computer Science (9)
- Coronavirus (1)
- Cybersecurity (1)
- Decarbonization (2)
- Energy Storage (7)
- Environment (8)
- Exascale Computing (2)
- Frontier (1)
- Fusion (14)
- Grid (2)
- High-Performance Computing (3)
- Isotopes (6)
- ITER (2)
- Machine Learning (2)
- Materials (19)
- Materials Science (17)
- Mathematics (1)
- Microscopy (6)
- Nanotechnology (8)
- Net Zero (1)
- Neutron Science (9)
- Nuclear Energy (26)
- Partnerships (3)
- Physics (12)
- Polymers (4)
- Quantum Computing (1)
- Simulation (2)
- Space Exploration (1)
- Summit (1)
- Sustainable Energy (5)
- Transformational Challenge Reactor (2)
Media Contacts

In fiscal year 2023 — Oct. 1–Sept. 30, 2023 — Oak Ridge National Laboratory was awarded more than $8 million in technology maturation funding through the Department of Energy’s Technology Commercialization Fund, or TCF.

ORNL hosted its fourth Artificial Intelligence for Robust Engineering and Science, or AIRES, workshop from April 18-20. Over 100 attendees from government, academia and industry convened to identify research challenges and investment areas, carving the future of the discipline.
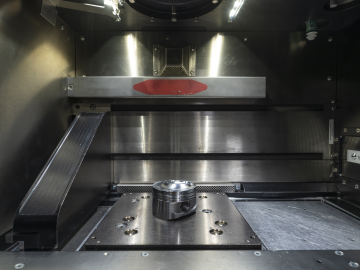
Dean Pierce of ORNL and a research team led by ORNL’s Alex Plotkowski were honored by DOE’s Vehicle Technologies Office for development of novel high-performance alloys that can withstand extreme environments.

A study led by researchers at ORNL could help make materials design as customizable as point-and-click.
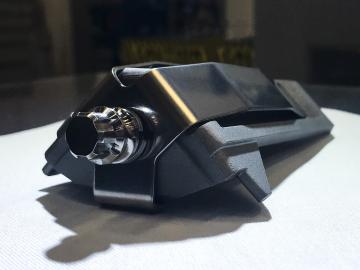
Four first-of-a-kind 3D-printed fuel assembly brackets, produced at the Department of Energy’s Manufacturing Demonstration Facility at Oak Ridge National Laboratory, have been installed and are now under routine operating
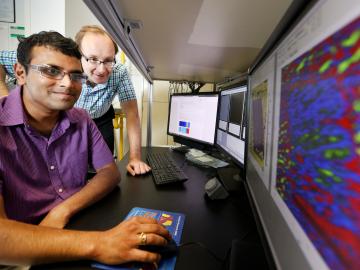
At the Department of Energy’s Oak Ridge National Laboratory, scientists use artificial intelligence, or AI, to accelerate the discovery and development of materials for energy and information technologies.
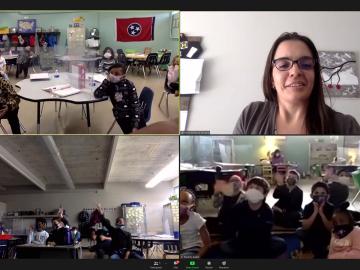
Twenty-seven ORNL researchers Zoomed into 11 middle schools across Tennessee during the annual Engineers Week in February. East Tennessee schools throughout Oak Ridge and Roane, Sevier, Blount and Loudon counties participated, with three West Tennessee schools joining in.
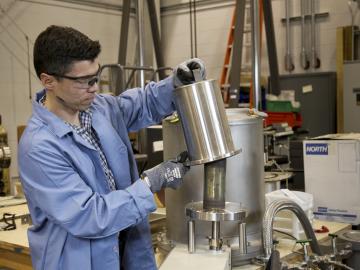
As program manager for the Department of Energy’s Oak Ridge National Laboratory’s Package Testing Program, Oscar Martinez enjoys finding and fixing technical issues.
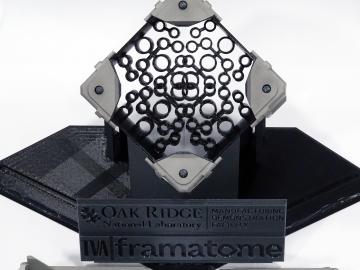
The Transformational Challenge Reactor, or TCR, a microreactor built using 3D printing and other new advanced technologies, could be operational by 2024.
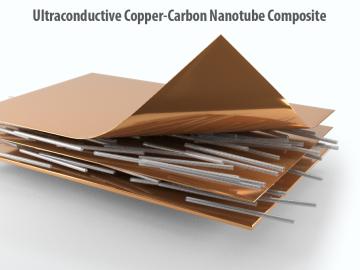
Scientists at Oak Ridge National Laboratory used new techniques to create a composite that increases the electrical current capacity of copper wires, providing a new material that can be scaled for use in ultra-efficient, power-dense electric vehicle traction motors.