Filter News
Area of Research
- (-) Fusion and Fission (5)
- (-) Materials (28)
- Advanced Manufacturing (1)
- Biology and Environment (61)
- Biology and Soft Matter (1)
- Clean Energy (31)
- Climate and Environmental Systems (1)
- Computational Biology (1)
- Computer Science (2)
- Isotopes (2)
- Materials for Computing (6)
- National Security (12)
- Neutron Science (16)
- Nuclear Science and Technology (7)
- Quantum information Science (1)
- Supercomputing (51)
News Topics
- (-) Advanced Reactors (3)
- (-) Composites (2)
- (-) Computer Science (9)
- (-) Environment (8)
- (-) Materials Science (17)
- (-) Space Exploration (1)
- 3-D Printing/Advanced Manufacturing (7)
- Artificial Intelligence (5)
- Big Data (2)
- Bioenergy (2)
- Biomedical (2)
- Buildings (1)
- Chemical Sciences (8)
- Clean Water (2)
- Coronavirus (1)
- Cybersecurity (1)
- Decarbonization (2)
- Energy Storage (7)
- Exascale Computing (2)
- Frontier (1)
- Fusion (14)
- Grid (2)
- High-Performance Computing (3)
- Isotopes (6)
- ITER (2)
- Machine Learning (2)
- Materials (19)
- Mathematics (1)
- Microscopy (6)
- Nanotechnology (8)
- Net Zero (1)
- Neutron Science (9)
- Nuclear Energy (26)
- Partnerships (3)
- Physics (12)
- Polymers (4)
- Quantum Computing (1)
- Security (2)
- Simulation (2)
- Summit (1)
- Sustainable Energy (5)
- Transformational Challenge Reactor (2)
- Transportation (5)
Media Contacts

In fiscal year 2023 — Oct. 1–Sept. 30, 2023 — Oak Ridge National Laboratory was awarded more than $8 million in technology maturation funding through the Department of Energy’s Technology Commercialization Fund, or TCF.
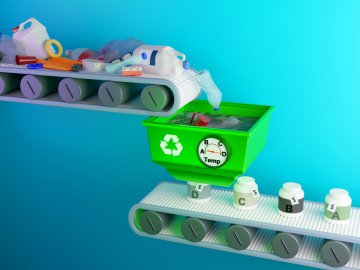
Little of the mixed consumer plastics thrown away or placed in recycle bins actually ends up being recycled. Nearly 90% is buried in landfills or incinerated at commercial facilities that generate greenhouse gases and airborne toxins. Neither outcome is ideal for the environment.

A scientific instrument at ORNL could help create a noninvasive cancer treatment derived from a common tropical plant.
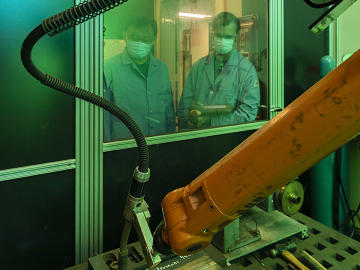
The U.S. Departments of Energy and Defense teamed up to create a series of weld filler materials that could dramatically improve high-strength steel repair in vehicles, bridges and pipelines.

Researchers in the geothermal energy industry are joining forces with fusion experts at ORNL to repurpose gyrotron technology, a tool used in fusion. Gyrotrons produce high-powered microwaves to heat up fusion plasmas.
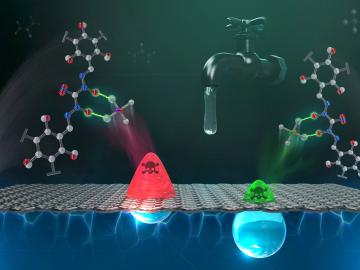
Researchers at ORNL are tackling a global water challenge with a unique material designed to target not one, but two toxic, heavy metal pollutants for simultaneous removal.

A study led by researchers at ORNL could help make materials design as customizable as point-and-click.
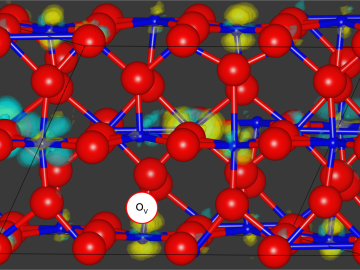
Neuromorphic devices — which emulate the decision-making processes of the human brain — show great promise for solving pressing scientific problems, but building physical systems to realize this potential presents researchers with a significant
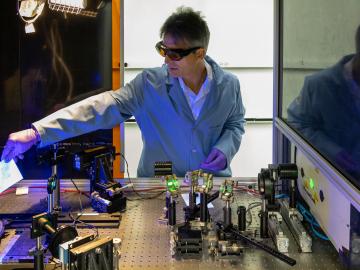
A multidisciplinary team of scientists at ORNL has applied a laser-interference structuring, or LIS, technique that makes significant strides toward eliminating the need for hazardous chemicals in corrosion protection for vehicles.
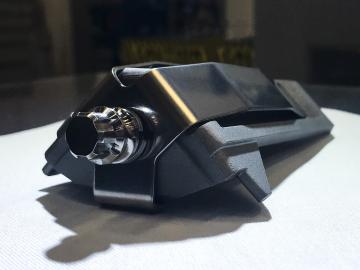
Four first-of-a-kind 3D-printed fuel assembly brackets, produced at the Department of Energy’s Manufacturing Demonstration Facility at Oak Ridge National Laboratory, have been installed and are now under routine operating