Filter News
Area of Research
- (-) Fusion and Fission (5)
- (-) Nuclear Science and Technology (3)
- Advanced Manufacturing (3)
- Biology and Environment (58)
- Biology and Soft Matter (1)
- Clean Energy (55)
- Climate and Environmental Systems (1)
- Isotopes (1)
- Materials (28)
- Materials for Computing (5)
- National Security (6)
- Neutron Science (13)
- Supercomputing (25)
News Topics
- (-) 3-D Printing/Advanced Manufacturing (5)
- (-) Environment (2)
- (-) Materials Science (2)
- (-) Transportation (1)
- Advanced Reactors (6)
- Artificial Intelligence (1)
- Bioenergy (1)
- Buildings (1)
- Chemical Sciences (2)
- Composites (1)
- Computer Science (2)
- Coronavirus (1)
- Decarbonization (1)
- Energy Storage (2)
- Exascale Computing (1)
- Frontier (1)
- Fusion (18)
- Grid (1)
- High-Performance Computing (2)
- Isotopes (2)
- ITER (2)
- Molten Salt (1)
- Net Zero (1)
- Neutron Science (1)
- Nuclear Energy (32)
- Partnerships (1)
- Physics (2)
- Security (1)
- Simulation (2)
- Space Exploration (1)
- Sustainable Energy (3)
- Transformational Challenge Reactor (2)
Media Contacts

Researchers in the geothermal energy industry are joining forces with fusion experts at ORNL to repurpose gyrotron technology, a tool used in fusion. Gyrotrons produce high-powered microwaves to heat up fusion plasmas.
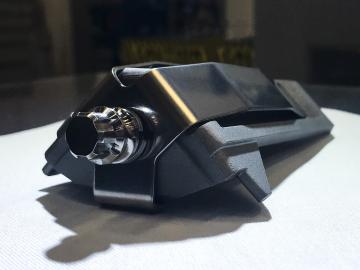
Four first-of-a-kind 3D-printed fuel assembly brackets, produced at the Department of Energy’s Manufacturing Demonstration Facility at Oak Ridge National Laboratory, have been installed and are now under routine operating
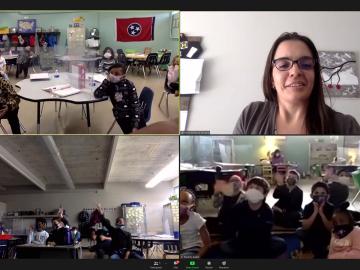
Twenty-seven ORNL researchers Zoomed into 11 middle schools across Tennessee during the annual Engineers Week in February. East Tennessee schools throughout Oak Ridge and Roane, Sevier, Blount and Loudon counties participated, with three West Tennessee schools joining in.
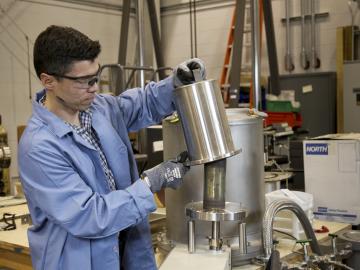
As program manager for the Department of Energy’s Oak Ridge National Laboratory’s Package Testing Program, Oscar Martinez enjoys finding and fixing technical issues.
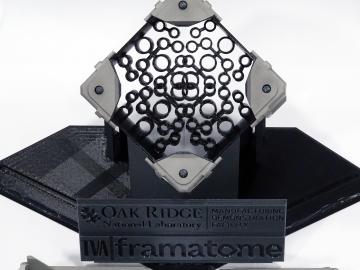
The Transformational Challenge Reactor, or TCR, a microreactor built using 3D printing and other new advanced technologies, could be operational by 2024.
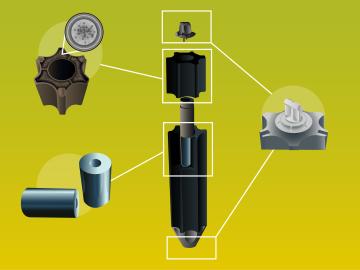
It’s a new type of nuclear reactor core. And the materials that will make it up are novel — products of Oak Ridge National Laboratory’s advanced materials and manufacturing technologies.
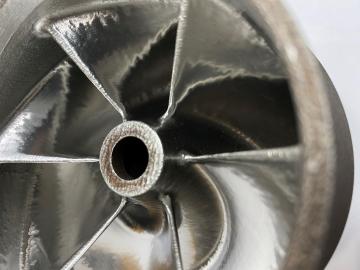
Scientists at the Department of Energy Manufacturing Demonstration Facility at ORNL have their eyes on the prize: the Transformational Challenge Reactor, or TCR, a microreactor built using 3D printing and other new approaches that will be up and running by 2023.
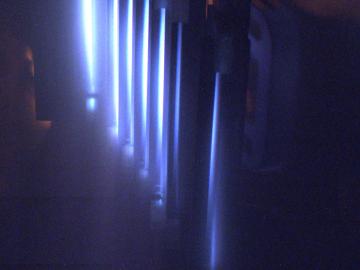
A tiny vial of gray powder produced at the Department of Energy’s Oak Ridge National Laboratory is the backbone of a new experiment to study the intense magnetic fields created in nuclear collisions.