Filter News
Area of Research
- (-) Advanced Manufacturing (10)
- (-) Neutron Science (15)
- Biological Systems (1)
- Biology and Environment (51)
- Clean Energy (102)
- Fusion and Fission (6)
- Isotopes (21)
- Materials (42)
- Materials for Computing (8)
- National Security (6)
- Nuclear Science and Technology (9)
- Quantum information Science (1)
- Supercomputing (18)
News Type
News Topics
- (-) 3-D Printing/Advanced Manufacturing (14)
- (-) Bioenergy (6)
- (-) Clean Water (2)
- (-) Transportation (3)
- Artificial Intelligence (6)
- Big Data (2)
- Biology (5)
- Biomedical (9)
- Biotechnology (1)
- Chemical Sciences (1)
- Climate Change (1)
- Composites (1)
- Computer Science (14)
- Coronavirus (8)
- Cybersecurity (2)
- Decarbonization (2)
- Energy Storage (4)
- Environment (6)
- Fossil Energy (1)
- Frontier (1)
- Fusion (1)
- High-Performance Computing (2)
- Machine Learning (4)
- Materials (11)
- Materials Science (20)
- Mathematics (1)
- Microscopy (2)
- Nanotechnology (8)
- National Security (2)
- Neutron Science (73)
- Nuclear Energy (3)
- Physics (8)
- Polymers (1)
- Quantum Computing (1)
- Quantum Science (5)
- Security (2)
- Space Exploration (2)
- Summit (6)
- Sustainable Energy (4)
- Transformational Challenge Reactor (1)
Media Contacts

Scientists at ORNL have developed 3D-printed collimator techniques that can be used to custom design collimators that better filter out noise during different types of neutron scattering experiments

How do you get water to float in midair? With a WAND2, of course. But it’s hardly magic. In fact, it’s a scientific device used by scientists to study matter.
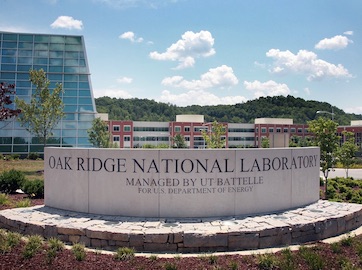
The Department of Energy’s Office of Science has selected three ORNL research teams to receive funding through DOE’s new Biopreparedness Research Virtual Environment initiative.

The ExOne Company, the global leader in industrial sand and metal 3D printers using binder jetting technology, announced it has reached a commercial license agreement with Oak Ridge National Laboratory to 3D print parts in aluminum-infiltrated boron carbide.
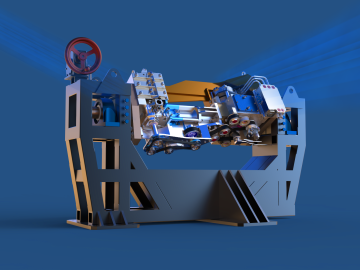
In the quest for advanced vehicles with higher energy efficiency and ultra-low emissions, ORNL researchers are accelerating a research engine that gives scientists and engineers an unprecedented view inside the atomic-level workings of combustion engines in real time.
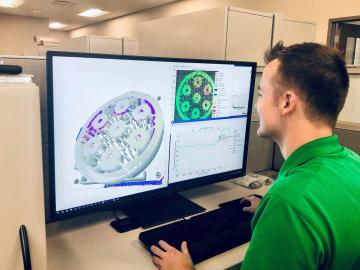
Oak Ridge National Laboratory researchers have developed artificial intelligence software for powder bed 3D printers that assesses the quality of parts in real time, without the need for expensive characterization equipment.
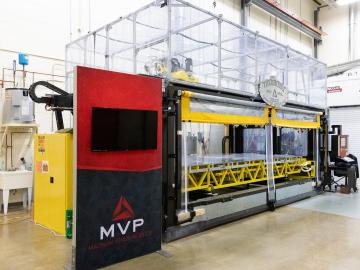
ORNL has licensed two additive manufacturing-related technologies that aim to streamline and ramp up production processes to Knoxville-based Magnum Venus Products, Inc., a global manufacturer of fluid movement and product solutions for industrial applications in composites and adhesives.
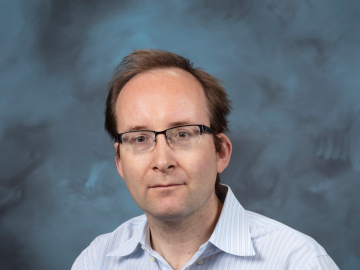
Five researchers at the Department of Energy’s Oak Ridge National Laboratory have been named ORNL Corporate Fellows in recognition of significant career accomplishments and continued leadership in their scientific fields.
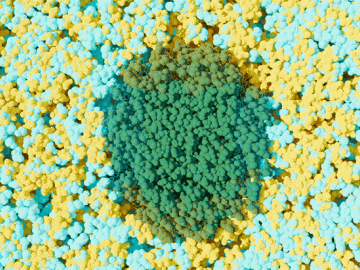
Scientists at ORNL used neutron scattering and supercomputing to better understand how an organic solvent and water work together to break down plant biomass, creating a pathway to significantly improve the production of renewable
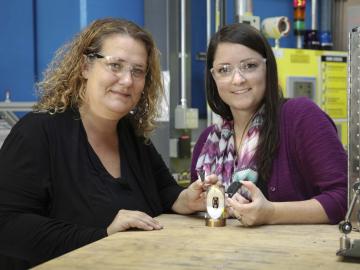
Oak Ridge National Laboratory has licensed a novel method to 3D print components used in neutron instruments for scientific research to the ExOne Company, a leading maker of binder jet 3D printing technology.