Filter News
Area of Research
News Type
News Topics
- (-) Advanced Reactors (1)
- (-) Bioenergy (2)
- (-) Buildings (8)
- (-) Clean Water (1)
- (-) Composites (3)
- (-) Space Exploration (1)
- 3-D Printing/Advanced Manufacturing (17)
- Artificial Intelligence (1)
- Big Data (2)
- Biology (3)
- Biotechnology (1)
- Climate Change (3)
- Computer Science (4)
- Coronavirus (1)
- Critical Materials (2)
- Decarbonization (4)
- Energy Storage (12)
- Environment (11)
- Grid (6)
- High-Performance Computing (3)
- Materials (12)
- Materials Science (4)
- Mathematics (1)
- Nanotechnology (1)
- Net Zero (1)
- Neutron Science (2)
- Nuclear Energy (1)
- Polymers (1)
- Security (1)
- Statistics (1)
- Summit (1)
- Sustainable Energy (19)
- Transportation (13)
Media Contacts
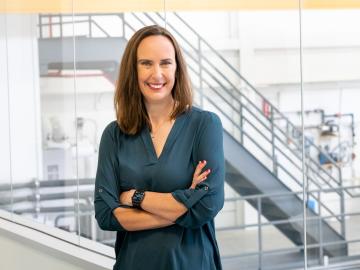
She may not wear a white coat or carry a stethoscope, but Christine Walker of ORNL spends her days diagnosing the energy health of buildings and figuring out how to improve their efficiency to achieve cost savings and reduce their carbon footprint.
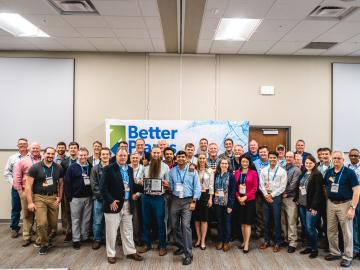
As the United States transitions to clean energy, the country has an ambitious goal: cut carbon dioxide emissions in half by the year 2030, if not before. One of the solutions to help meet this challenge is found at ORNL as part of the Better Plants Program.
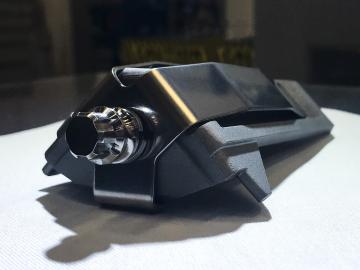
Four first-of-a-kind 3D-printed fuel assembly brackets, produced at the Department of Energy’s Manufacturing Demonstration Facility at Oak Ridge National Laboratory, have been installed and are now under routine operating

A research team at Oak Ridge National Laboratory have 3D printed a thermal protection shield, or TPS, for a capsule that will launch with the Cygnus cargo spacecraft as part of the supply mission to the International Space Station.
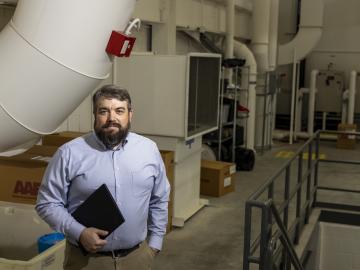
Long before COVID-19’s rapid transmission led to a worldwide pandemic, Oak Ridge National Laboratory’s Jason DeGraw was performing computer modeling to better understand the impact of virus-laden droplets on indoor air quality
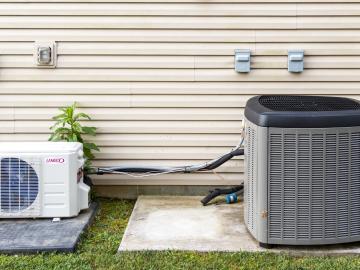
Oak Ridge National Laboratory researchers designed and field-tested an algorithm that could help homeowners maintain comfortable temperatures year-round while minimizing utility costs.
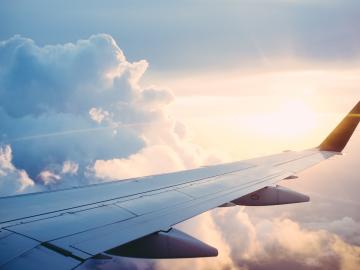
ORNL’s Zhenglong Li led a team tasked with improving the current technique for converting ethanol to C3+ olefins and demonstrated a unique composite catalyst that upends current practice and drives down costs. The research was published in ACS Catalysis.
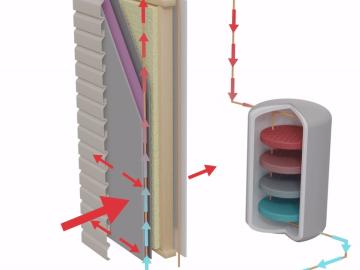
Researchers at Oak Ridge National Laboratory have developed a novel envelope system that diverts heat or coolness away from a building and stores it for future use.
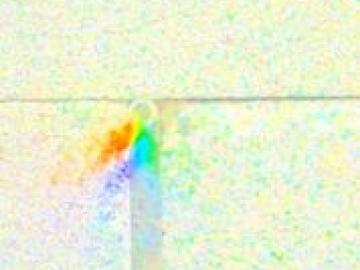
A team of researchers at Oak Ridge National Laboratory has developed a method to detect and measure air leaking from a building’s walls and roof that is quicker, cheaper and less disruptive to occupants.
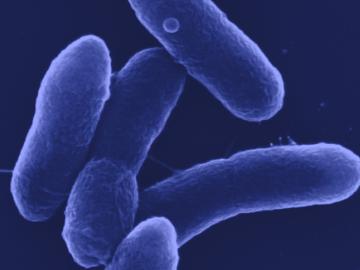
A research team led by Oak Ridge National Laboratory bioengineered a microbe to efficiently turn waste into itaconic acid, an industrial chemical used in plastics and paints.