Filter News
Area of Research
News Topics
- (-) 3-D Printing/Advanced Manufacturing (8)
- (-) Isotopes (1)
- (-) Materials Science (6)
- Artificial Intelligence (1)
- Bioenergy (1)
- Biology (1)
- Chemical Sciences (2)
- Climate Change (1)
- Composites (3)
- Computer Science (2)
- Critical Materials (1)
- Cybersecurity (1)
- Energy Storage (1)
- Frontier (1)
- Fusion (1)
- ITER (1)
- Materials (12)
- Microscopy (5)
- Nanotechnology (6)
- Neutron Science (4)
- Physics (1)
- Polymers (1)
- Quantum Computing (1)
- Quantum Science (2)
- Space Exploration (2)
- Sustainable Energy (3)
Media Contacts

Ten scientists from the Department of Energy’s Oak Ridge National Laboratory are among the world’s most highly cited researchers, according to a bibliometric analysis conducted by the scientific publication analytics firm Clarivate.

Amy Elliott, a group leader for robotics and intelligent systems at Oak Ridge National Laboratory, has received the 2021 ASTM International Additive Manufacturing Young Professional Award for her early career research contributions
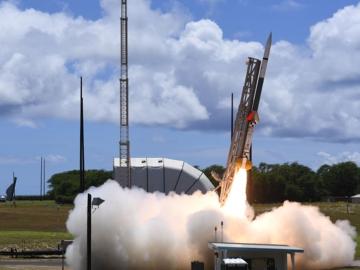
Oak Ridge National Laboratory researchers have developed a novel process to manufacture extreme heat resistant carbon-carbon composites. The performance of these materials will be tested in a U.S. Navy rocket that NASA will launch this fall.
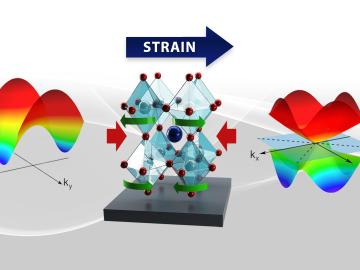
A team led by the ORNL has found a rare quantum material in which electrons move in coordinated ways, essentially “dancing.”
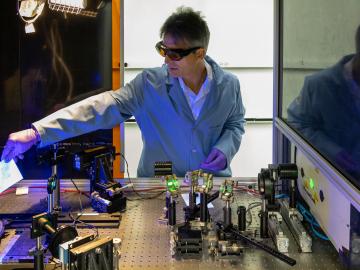
A multidisciplinary team of scientists at ORNL has applied a laser-interference structuring, or LIS, technique that makes significant strides toward eliminating the need for hazardous chemicals in corrosion protection for vehicles.

A research team at Oak Ridge National Laboratory have 3D printed a thermal protection shield, or TPS, for a capsule that will launch with the Cygnus cargo spacecraft as part of the supply mission to the International Space Station.

Scientists at ORNL and the University of Tennessee, Knoxville, have found a way to simultaneously increase the strength and ductility of an alloy by introducing tiny precipitates into its matrix and tuning their size and spacing.
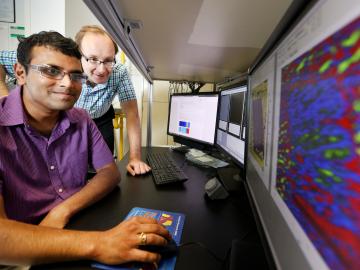
At the Department of Energy’s Oak Ridge National Laboratory, scientists use artificial intelligence, or AI, to accelerate the discovery and development of materials for energy and information technologies.
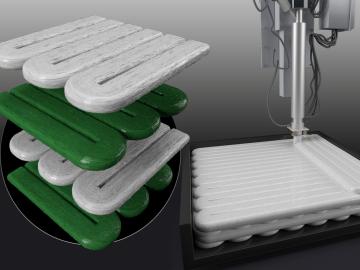
Oak Ridge National Laboratory researchers combined additive manufacturing with conventional compression molding to produce high-performance thermoplastic composites reinforced with short carbon fibers.

A team of Oak Ridge National Laboratory researchers demonstrated that an additively manufactured hot stamping die – a tool used to create car body components – cooled faster than those produced by conventional manufacturing methods.