Filter News
Area of Research
News Topics
- (-) 3-D Printing/Advanced Manufacturing (8)
- (-) Grid (2)
- (-) Materials Science (3)
- (-) Microscopy (1)
- (-) Polymers (1)
- (-) Space Exploration (3)
- Advanced Reactors (1)
- Artificial Intelligence (4)
- Big Data (4)
- Bioenergy (3)
- Biomedical (2)
- Biotechnology (1)
- Clean Water (3)
- Composites (1)
- Computer Science (19)
- Energy Storage (5)
- Environment (9)
- Exascale Computing (1)
- Mercury (1)
- Nanotechnology (2)
- Nuclear Energy (3)
- Quantum Science (1)
- Summit (6)
- Sustainable Energy (3)
- Transportation (8)
Media Contacts
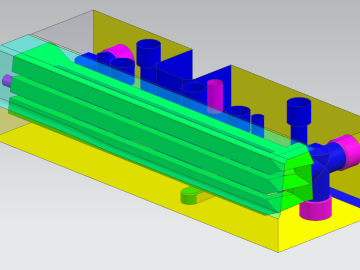
Researchers demonstrated that an additively manufactured hot stamping die can withstand up to 25,000 usage cycles, proving that this technique is a viable solution for production.

The type of vehicle that will carry people to the Red Planet is shaping up to be “like a two-story house you’re trying to land on another planet.
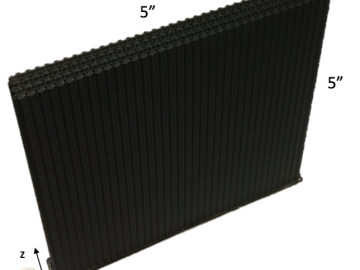
A team including Oak Ridge National Laboratory and University of Tennessee researchers demonstrated a novel 3D printing approach called Z-pinning that can increase the material’s strength and toughness by more than three and a half times compared to conventional additive manufacturing processes.
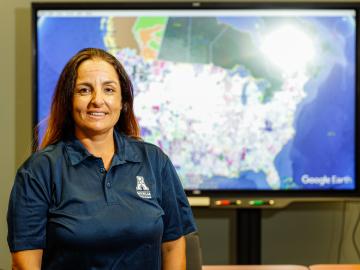
Isabelle Snyder calls faults as she sees them, whether it’s modeling operations for the nation’s power grid or officiating at the US Open Tennis Championships.
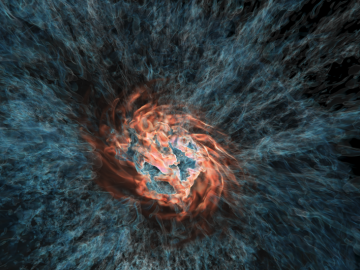
Using the Titan supercomputer at Oak Ridge National Laboratory, a team of astrophysicists created a set of galactic wind simulations of the highest resolution ever performed. The simulations will allow researchers to gather and interpret more accurate, detailed data that elucidates how galactic winds affect the formation and evolution of galaxies.
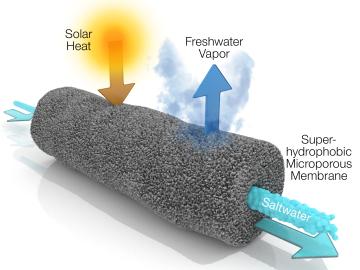
A new method developed at Oak Ridge National Laboratory improves the energy efficiency of a desalination process known as solar-thermal evaporation.

A team of researchers at Oak Ridge National Laboratory have demonstrated that designed synthetic polymers can serve as a high-performance binding material for next-generation lithium-ion batteries.
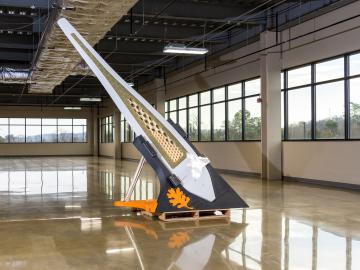
In the shifting landscape of global manufacturing, American ingenuity is once again giving U.S companies an edge with radical productivity improvements as a result of advanced materials and robotic systems developed at the Department of Energy’s Manufacturing Demonstration Facility (MDF) at Oak Ridge National Laboratory.
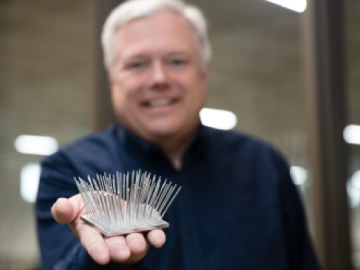
When Scott Smith looks at a machine tool, he thinks not about what the powerful equipment used to shape metal can do – he’s imagining what it could do with the right added parts and strategies. As ORNL’s leader for a newly formed group, Machining and Machine Tool Research, Smith will have the opportunity to do just that.
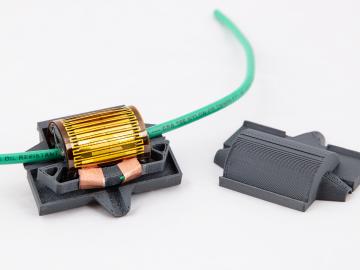
Scientists at Oak Ridge National Laboratory have developed a low-cost, printed, flexible sensor that can wrap around power cables to precisely monitor electrical loads from household appliances to support grid operations.