Filter News
Area of Research
- (-) Materials (16)
- (-) National Security (2)
- Advanced Manufacturing (6)
- Biological Systems (1)
- Biology and Environment (1)
- Clean Energy (29)
- Climate and Environmental Systems (1)
- Computational Engineering (1)
- Computer Science (8)
- Fusion Energy (5)
- Neutron Science (5)
- Nuclear Science and Technology (1)
- Quantum information Science (3)
- Supercomputing (24)
News Topics
- (-) 3-D Printing/Advanced Manufacturing (5)
- (-) Bioenergy (2)
- (-) Computer Science (5)
- (-) Energy Storage (4)
- (-) Fusion (2)
- (-) Polymers (2)
- (-) Sustainable Energy (5)
- Advanced Reactors (1)
- Artificial Intelligence (2)
- Big Data (1)
- Clean Water (2)
- Composites (1)
- Cybersecurity (2)
- Environment (5)
- Grid (1)
- Isotopes (1)
- Machine Learning (1)
- Materials Science (18)
- Microscopy (5)
- Molten Salt (1)
- Nanotechnology (6)
- Neutron Science (4)
- Nuclear Energy (7)
- Physics (2)
- Quantum Science (2)
- Security (1)
- Transportation (5)
Media Contacts
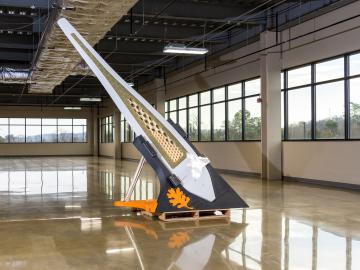
In the shifting landscape of global manufacturing, American ingenuity is once again giving U.S companies an edge with radical productivity improvements as a result of advanced materials and robotic systems developed at the Department of Energy’s Manufacturing Demonstration Facility (MDF) at Oak Ridge National Laboratory.
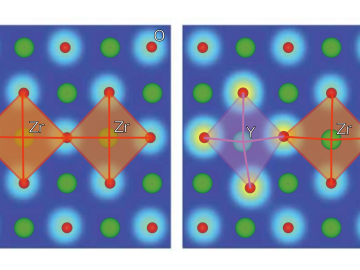
Ionic conduction involves the movement of ions from one location to another inside a material. The ions travel through point defects, which are irregularities in the otherwise consistent arrangement of atoms known as the crystal lattice. This sometimes sluggish process can limit the performance and efficiency of fuel cells, batteries, and other energy storage technologies.
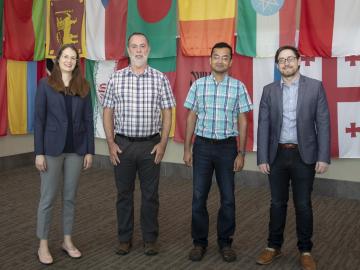
Scientists at the Department of Energy’s Oak Ridge National Laboratory are working to understand both the complex nature of uranium and the various oxide forms it can take during processing steps that might occur throughout the nuclear fuel cycle.
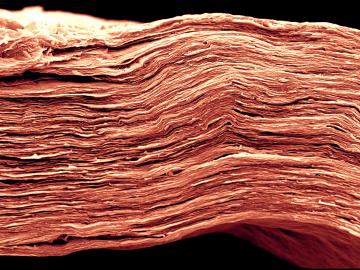
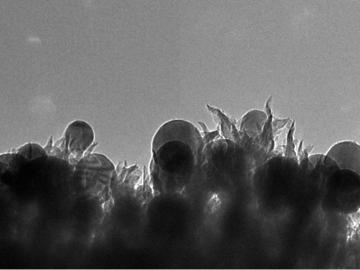
OAK RIDGE, Tenn., March 1, 2019—ReactWell, LLC, has licensed a novel waste-to-fuel technology from the Department of Energy’s Oak Ridge National Laboratory to improve energy conversion methods for cleaner, more efficient oil and gas, chemical and
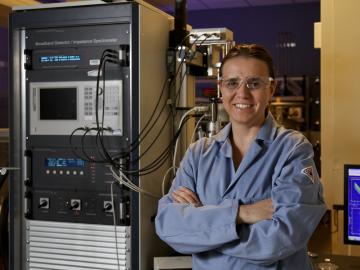
Vera Bocharova at the Department of Energy’s Oak Ridge National Laboratory investigates the structure and dynamics of soft materials—polymer nanocomposites, polymer electrolytes and biological macromolecules—to advance materials and technologies for energy, medicine and other applications.

Scientists have tested a novel heat-shielding graphite foam, originally created at Oak Ridge National Laboratory, at Germany’s Wendelstein 7-X stellarator with promising results for use in plasma-facing components of fusion reactors.
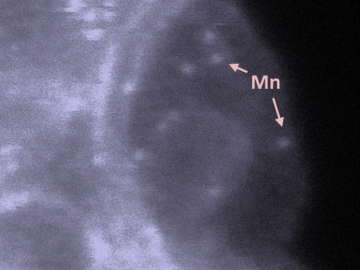
Oak Ridge National Laboratory scientists studying fuel cells as a potential alternative to internal combustion engines used sophisticated electron microscopy to investigate the benefits of replacing high-cost platinum with a lower cost, carbon-nitrogen-manganese-based catalyst.