Filter News
Area of Research
News Topics
- (-) 3-D Printing/Advanced Manufacturing (5)
- (-) Clean Water (3)
- (-) Energy Storage (4)
- (-) Polymers (2)
- (-) Quantum Science (1)
- Advanced Reactors (1)
- Artificial Intelligence (2)
- Bioenergy (1)
- Biomedical (1)
- Chemical Sciences (2)
- Composites (2)
- Computer Science (3)
- Coronavirus (1)
- Critical Materials (2)
- Decarbonization (1)
- Environment (5)
- Fusion (2)
- High-Performance Computing (1)
- Isotopes (2)
- Materials (12)
- Materials Science (11)
- Microscopy (4)
- Molten Salt (1)
- Nanotechnology (6)
- Neutron Science (4)
- Nuclear Energy (5)
- Physics (2)
- Sustainable Energy (3)
- Transportation (4)
Media Contacts
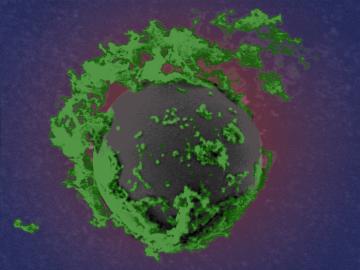
The presence of minerals called ash in plants makes little difference to the fitness of new naturally derived compound materials designed for additive manufacturing, an Oak Ridge National Laboratory-led team found.

Oak Ridge National Laboratory researchers serendipitously discovered when they automated the beam of an electron microscope to precisely drill holes in the atomically thin lattice of graphene, the drilled holes closed up.
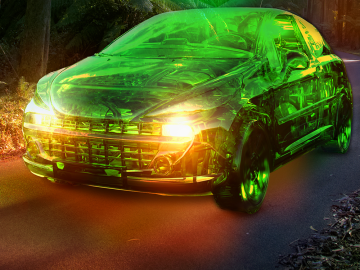
Oak Ridge National Laboratory scientists designed a recyclable polymer for carbon-fiber composites to enable circular manufacturing of parts that boost energy efficiency in automotive, wind power and aerospace applications.
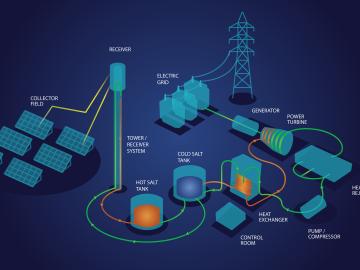
Oak Ridge National Laboratory scientists recently demonstrated a low-temperature, safe route to purifying molten chloride salts that minimizes their ability to corrode metals. This method could make the salts useful for storing energy generated from the sun’s heat.
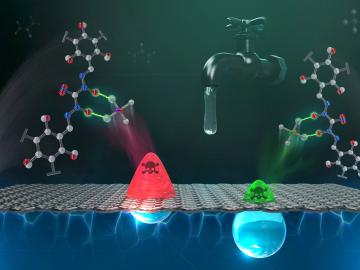
Researchers at ORNL are tackling a global water challenge with a unique material designed to target not one, but two toxic, heavy metal pollutants for simultaneous removal.
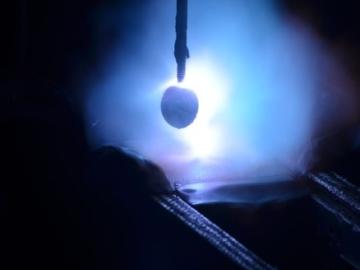
Researchers at Oak Ridge National Laboratory demonstrated that an additively manufactured polymer layer, when applied to carbon fiber reinforced plastic, or CFRP, can serve as an effective protector against aircraft lightning strikes.
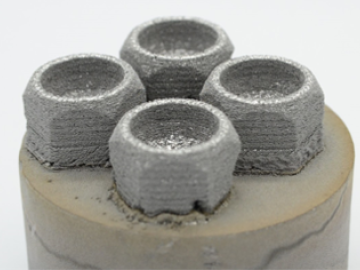
Using additive manufacturing, scientists experimenting with tungsten at Oak Ridge National Laboratory hope to unlock new potential of the high-performance heat-transferring material used to protect components from the plasma inside a fusion reactor. Fusion requires hydrogen isotopes to reach millions of degrees.
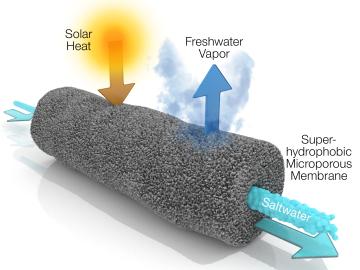
A new method developed at Oak Ridge National Laboratory improves the energy efficiency of a desalination process known as solar-thermal evaporation.

A team of researchers at Oak Ridge National Laboratory have demonstrated that designed synthetic polymers can serve as a high-performance binding material for next-generation lithium-ion batteries.
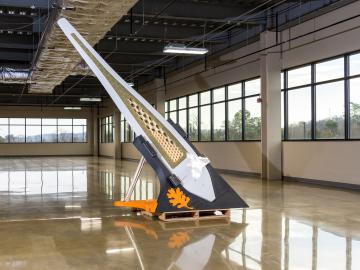
In the shifting landscape of global manufacturing, American ingenuity is once again giving U.S companies an edge with radical productivity improvements as a result of advanced materials and robotic systems developed at the Department of Energy’s Manufacturing Demonstration Facility (MDF) at Oak Ridge National Laboratory.