Filter News
Area of Research
- (-) Advanced Manufacturing (8)
- (-) Supercomputing (8)
- Biology and Environment (5)
- Building Technologies (1)
- Clean Energy (44)
- Computational Biology (1)
- Fuel Cycle Science and Technology (1)
- Fusion and Fission (7)
- Fusion Energy (1)
- Isotopes (11)
- Materials (18)
- Materials for Computing (9)
- National Security (2)
- Neutron Science (20)
- Nuclear Science and Technology (6)
- Transportation Systems (1)
News Type
News Topics
- (-) 3-D Printing/Advanced Manufacturing (9)
- (-) Artificial Intelligence (4)
- (-) Neutron Science (3)
- (-) Transportation (2)
- Biology (1)
- Biomedical (1)
- Buildings (1)
- Chemical Sciences (1)
- Climate Change (3)
- Composites (2)
- Computer Science (20)
- Coronavirus (2)
- Critical Materials (1)
- Cybersecurity (2)
- Energy Storage (2)
- Environment (6)
- Frontier (3)
- High-Performance Computing (10)
- Machine Learning (1)
- Materials (5)
- Materials Science (4)
- Microscopy (2)
- Nanotechnology (1)
- National Security (1)
- Physics (2)
- Polymers (1)
- Quantum Computing (5)
- Quantum Science (4)
- Security (1)
- Space Exploration (1)
- Summit (7)
- Sustainable Energy (4)
Media Contacts

A team led by the U.S. Department of Energy’s Oak Ridge National Laboratory demonstrated the viability of a “quantum entanglement witness” capable of proving the presence of entanglement between magnetic particles, or spins, in a quantum material.
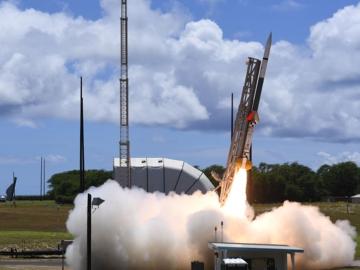
Oak Ridge National Laboratory researchers have developed a novel process to manufacture extreme heat resistant carbon-carbon composites. The performance of these materials will be tested in a U.S. Navy rocket that NASA will launch this fall.
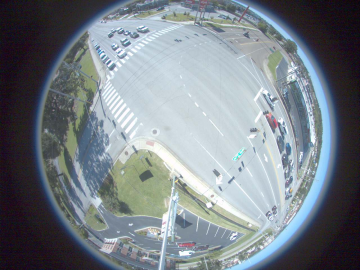
The daily traffic congestion along the streets and interstate lanes of Chattanooga could be headed the way of the horse and buggy with help from ORNL researchers.

A research team at Oak Ridge National Laboratory have 3D printed a thermal protection shield, or TPS, for a capsule that will launch with the Cygnus cargo spacecraft as part of the supply mission to the International Space Station.

An ORNL-led team comprising researchers from multiple DOE national laboratories is using artificial intelligence and computational screening techniques – in combination with experimental validation – to identify and design five promising drug therapy approaches to target the SARS-CoV-2 virus.
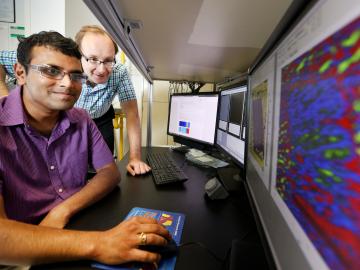
At the Department of Energy’s Oak Ridge National Laboratory, scientists use artificial intelligence, or AI, to accelerate the discovery and development of materials for energy and information technologies.
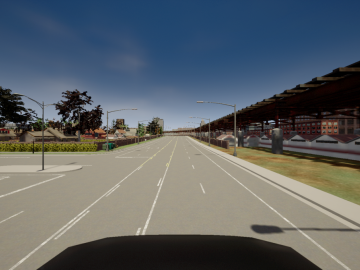
The Department of Energy’s Oak Ridge National Laboratory has licensed its award-winning artificial intelligence software system, the Multinode Evolutionary Neural Networks for Deep Learning, to General Motors for use in vehicle technology and design.
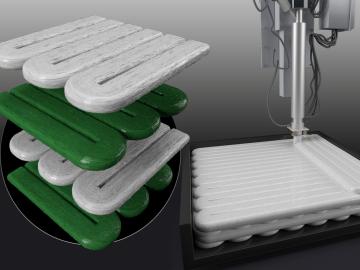
Oak Ridge National Laboratory researchers combined additive manufacturing with conventional compression molding to produce high-performance thermoplastic composites reinforced with short carbon fibers.

A team of Oak Ridge National Laboratory researchers demonstrated that an additively manufactured hot stamping die – a tool used to create car body components – cooled faster than those produced by conventional manufacturing methods.
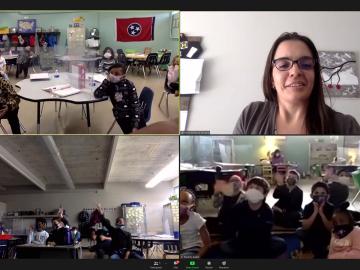
Twenty-seven ORNL researchers Zoomed into 11 middle schools across Tennessee during the annual Engineers Week in February. East Tennessee schools throughout Oak Ridge and Roane, Sevier, Blount and Loudon counties participated, with three West Tennessee schools joining in.