Filter News
Area of Research
- (-) Materials (19)
- (-) National Security (3)
- Advanced Manufacturing (8)
- Biology and Environment (2)
- Building Technologies (1)
- Clean Energy (33)
- Climate and Environmental Systems (1)
- Computational Engineering (1)
- Computer Science (8)
- Fusion Energy (1)
- Neutron Science (3)
- Nuclear Science and Technology (1)
- Quantum information Science (3)
- Supercomputing (31)
News Topics
- (-) 3-D Printing/Advanced Manufacturing (7)
- (-) Big Data (1)
- (-) Computer Science (6)
- (-) Cybersecurity (2)
- (-) Grid (2)
- (-) Polymers (5)
- (-) Sustainable Energy (5)
- Advanced Reactors (1)
- Artificial Intelligence (2)
- Bioenergy (3)
- Biomedical (3)
- Clean Water (2)
- Composites (3)
- Energy Storage (5)
- Environment (5)
- Fusion (3)
- Isotopes (6)
- Machine Learning (1)
- Materials Science (25)
- Microscopy (9)
- Molten Salt (1)
- Nanotechnology (12)
- Neutron Science (7)
- Nuclear Energy (9)
- Physics (6)
- Quantum Science (2)
- Security (2)
- Space Exploration (1)
- Transportation (7)
Media Contacts
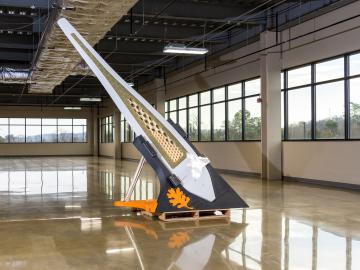
In the shifting landscape of global manufacturing, American ingenuity is once again giving U.S companies an edge with radical productivity improvements as a result of advanced materials and robotic systems developed at the Department of Energy’s Manufacturing Demonstration Facility (MDF) at Oak Ridge National Laboratory.
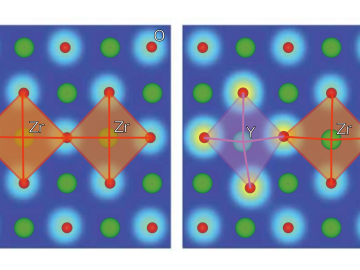
Ionic conduction involves the movement of ions from one location to another inside a material. The ions travel through point defects, which are irregularities in the otherwise consistent arrangement of atoms known as the crystal lattice. This sometimes sluggish process can limit the performance and efficiency of fuel cells, batteries, and other energy storage technologies.
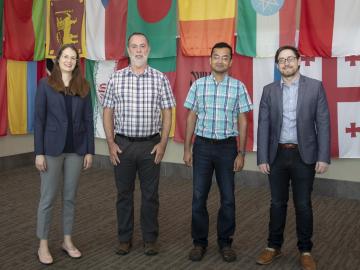
Scientists at the Department of Energy’s Oak Ridge National Laboratory are working to understand both the complex nature of uranium and the various oxide forms it can take during processing steps that might occur throughout the nuclear fuel cycle.
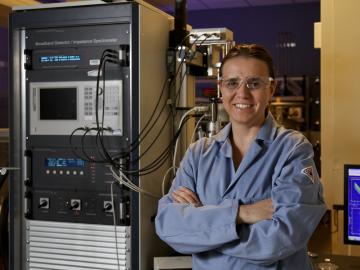
Vera Bocharova at the Department of Energy’s Oak Ridge National Laboratory investigates the structure and dynamics of soft materials—polymer nanocomposites, polymer electrolytes and biological macromolecules—to advance materials and technologies for energy, medicine and other applications.
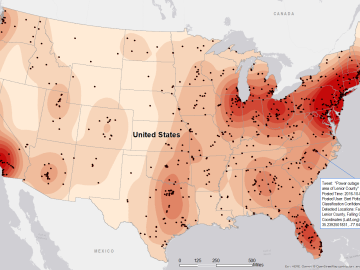
Gleaning valuable data from social platforms such as Twitter—particularly to map out critical location information during emergencies— has become more effective and efficient thanks to Oak Ridge National Laboratory.
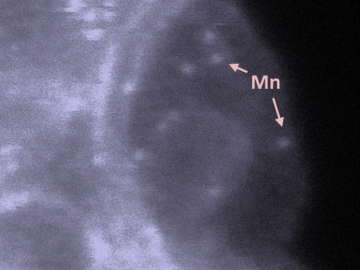
Oak Ridge National Laboratory scientists studying fuel cells as a potential alternative to internal combustion engines used sophisticated electron microscopy to investigate the benefits of replacing high-cost platinum with a lower cost, carbon-nitrogen-manganese-based catalyst.
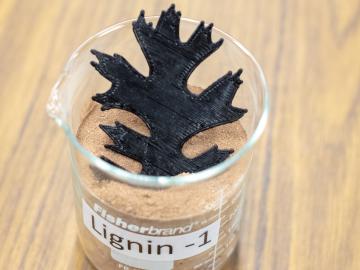
Scientists at the Department of Energy’s Oak Ridge National Laboratory have created a recipe for a renewable 3D printing feedstock that could spur a profitable new use for an intractable biorefinery byproduct: lignin.
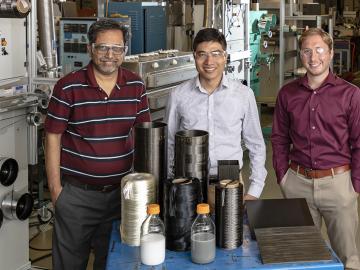
Carbon fiber composites—lightweight and strong—are great structural materials for automobiles, aircraft and other transportation vehicles. They consist of a polymer matrix, such as epoxy, into which reinforcing carbon fibers have been embedded. Because of differences in the mecha...
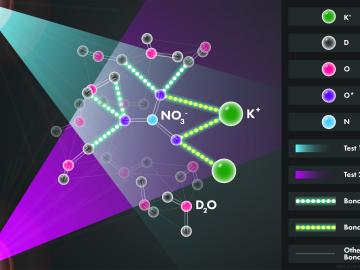
Scientists at the Department of Energy’s Oak Ridge National Laboratory used neutrons, isotopes and simulations to “see” the atomic structure of a saturated solution and found evidence supporting one of two competing hypotheses about how ions come
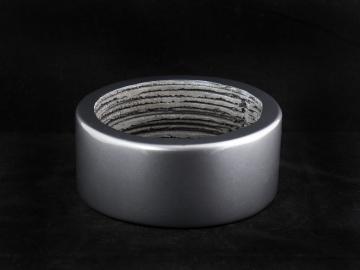
Oak Ridge National Laboratory scientists have improved a mixture of materials used to 3D print permanent magnets with increased density, which could yield longer lasting, better performing magnets for electric motors, sensors and vehicle applications. Building on previous research, ...