Filter News
Area of Research
- Advanced Manufacturing (4)
- Biology and Environment (6)
- Clean Energy (23)
- Climate and Environmental Systems (2)
- Computational Engineering (1)
- Computer Science (4)
- Fuel Cycle Science and Technology (1)
- Fusion and Fission (4)
- Fusion Energy (10)
- Isotopes (2)
- Materials (19)
- National Security (8)
- Neutron Science (7)
- Nuclear Science and Technology (33)
- Nuclear Systems Modeling, Simulation and Validation (2)
- Sensors and Controls (1)
- Supercomputing (20)
News Topics
- (-) Advanced Reactors (22)
- (-) Artificial Intelligence (22)
- (-) Climate Change (11)
- (-) Composites (7)
- (-) Frontier (3)
- (-) Mathematics (2)
- (-) Nuclear Energy (58)
- (-) Security (12)
- 3-D Printing/Advanced Manufacturing (49)
- Big Data (21)
- Bioenergy (25)
- Biology (7)
- Biomedical (30)
- Biotechnology (3)
- Buildings (1)
- Chemical Sciences (5)
- Clean Water (8)
- Computer Science (94)
- Coronavirus (23)
- Critical Materials (3)
- Cybersecurity (14)
- Decarbonization (1)
- Energy Storage (32)
- Environment (55)
- Exascale Computing (6)
- Fusion (23)
- Grid (15)
- High-Performance Computing (3)
- Isotopes (15)
- Machine Learning (13)
- Materials (2)
- Materials Science (69)
- Mercury (4)
- Microscopy (19)
- Molten Salt (7)
- Nanotechnology (32)
- National Security (2)
- Neutron Science (58)
- Physics (30)
- Polymers (14)
- Quantum Science (27)
- Space Exploration (8)
- Summit (28)
- Sustainable Energy (32)
- Transformational Challenge Reactor (5)
- Transportation (36)
Media Contacts
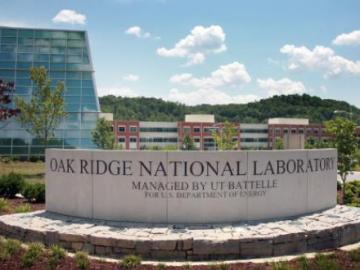
James Peery, who led critical national security programs at Sandia National Laboratories and held multiple leadership positions at Los Alamos National Laboratory before arriving at the Department of Energy’s Oak Ridge National Laboratory last year, has been named a...
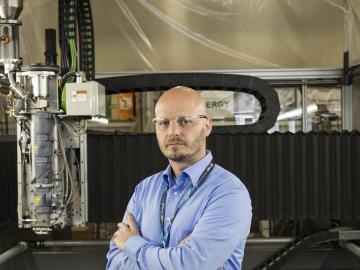
Vlastimil Kunc grew up in a family of scientists where his natural curiosity was encouraged—an experience that continues to drive his research today in polymer composite additive manufacturing at Oak Ridge National Laboratory. “I’ve been interested in the science of composites si...
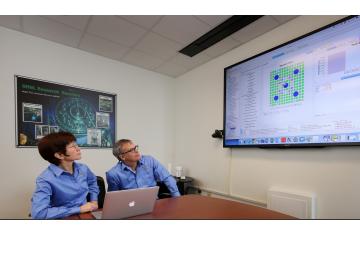
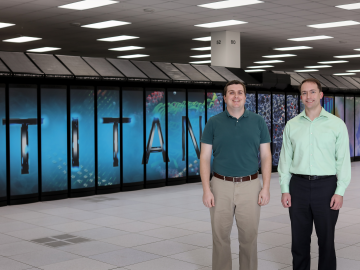
A team of researchers from the Department of Energy’s Oak Ridge National Laboratory has married artificial intelligence and high-performance computing to achieve a peak speed of 20 petaflops in the generation and training of deep learning networks on the
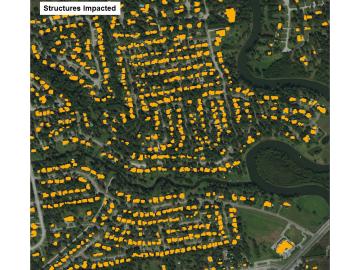
Geospatial scientists at Oak Ridge National Laboratory have developed a novel method to quickly gather building structure datasets that support emergency response teams assessing properties damaged by Hurricanes Harvey and Irma. By coupling deep learning with high-performance comp...
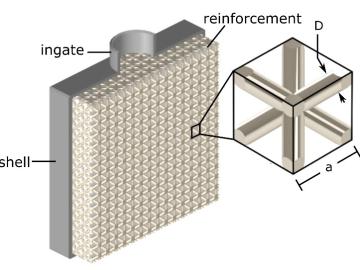
A new manufacturing method created by Oak Ridge National Laboratory and Rice University combines 3D printing with traditional casting to produce damage-tolerant components composed of multiple materials. Composite components made by pouring an aluminum alloy over a printed steel lattice showed an order of magnitude greater damage tolerance than aluminum alone.