Filter News
Area of Research
News Topics
- (-) Bioenergy (11)
- (-) Biomedical (5)
- (-) Composites (3)
- (-) Frontier (2)
- (-) Nuclear Energy (17)
- 3-D Printing/Advanced Manufacturing (16)
- Advanced Reactors (7)
- Artificial Intelligence (13)
- Big Data (9)
- Biology (1)
- Biotechnology (1)
- Clean Water (5)
- Computer Science (41)
- Cybersecurity (7)
- Energy Storage (9)
- Environment (23)
- Exascale Computing (3)
- Fusion (6)
- Grid (5)
- Isotopes (1)
- Machine Learning (5)
- Materials Science (22)
- Mercury (2)
- Microscopy (6)
- Molten Salt (1)
- Nanotechnology (6)
- Neutron Science (20)
- Physics (8)
- Polymers (2)
- Quantum Science (10)
- Security (2)
- Space Exploration (4)
- Summit (9)
- Sustainable Energy (8)
- Transportation (14)
Media Contacts
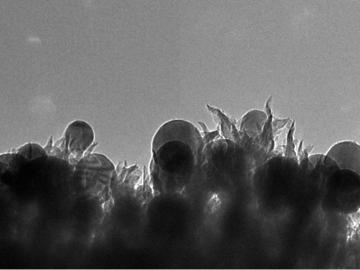
OAK RIDGE, Tenn., March 1, 2019—ReactWell, LLC, has licensed a novel waste-to-fuel technology from the Department of Energy’s Oak Ridge National Laboratory to improve energy conversion methods for cleaner, more efficient oil and gas, chemical and

Scientists have tested a novel heat-shielding graphite foam, originally created at Oak Ridge National Laboratory, at Germany’s Wendelstein 7-X stellarator with promising results for use in plasma-facing components of fusion reactors.
![Coexpression_hi-res_image[1].jpg Coexpression_hi-res_image[1].jpg](/sites/default/files/styles/list_page_thumbnail/public/Coexpression_hi-res_image%5B1%5D_0.jpg?itok=OnLe-krT)
While studying the genes in poplar trees that control callus formation, scientists at Oak Ridge National Laboratory have uncovered genetic networks at the root of tumor formation in several human cancers.

By automating the production of neptunium oxide-aluminum pellets, Oak Ridge National Laboratory scientists have eliminated a key bottleneck when producing plutonium-238 used by NASA to fuel deep space exploration.

With the licensing to Enchi Corporation of a microbe custom-designed to produce ethanol efficiently, Oak Ridge National Laboratory (ORNL) and the BioEnergy Science Center (BESC) mark the culmination of 10 years’ research into ways to improve biofuels production. Enchi ha...

The Department of Energy has announced funding for new research centers to accelerate the development of specialty plants and processes for a new generation of biofuels and bioproducts. The Center for Bioenergy Innovation (CBI), led by Oak Ridge National Laboratory...
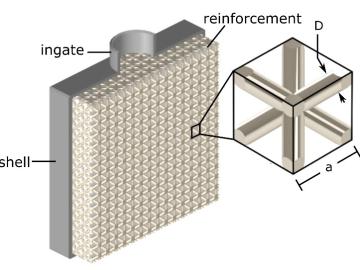
A new manufacturing method created by Oak Ridge National Laboratory and Rice University combines 3D printing with traditional casting to produce damage-tolerant components composed of multiple materials. Composite components made by pouring an aluminum alloy over a printed steel lattice showed an order of magnitude greater damage tolerance than aluminum alone.