Filter News
Area of Research
- (-) Clean Energy (11)
- Advanced Manufacturing (2)
- Biology and Environment (9)
- Climate and Environmental Systems (1)
- Computational Biology (1)
- Computational Engineering (1)
- Fusion and Fission (1)
- Isotopes (11)
- Materials (24)
- Materials for Computing (5)
- National Security (3)
- Neutron Science (9)
- Nuclear Science and Technology (3)
- Supercomputing (7)
News Topics
- (-) Biomedical (1)
- (-) Composites (6)
- (-) Cybersecurity (1)
- (-) Mercury (2)
- (-) Microscopy (1)
- (-) Space Exploration (2)
- 3-D Printing/Advanced Manufacturing (27)
- Advanced Reactors (1)
- Artificial Intelligence (1)
- Big Data (3)
- Bioenergy (4)
- Biology (6)
- Biotechnology (1)
- Buildings (11)
- Chemical Sciences (1)
- Clean Water (1)
- Climate Change (5)
- Computer Science (5)
- Coronavirus (2)
- Critical Materials (3)
- Decarbonization (5)
- Energy Storage (21)
- Environment (15)
- Grid (11)
- High-Performance Computing (4)
- Materials (17)
- Materials Science (7)
- Mathematics (1)
- Nanotechnology (2)
- Net Zero (1)
- Neutron Science (3)
- Nuclear Energy (1)
- Polymers (4)
- Security (3)
- Statistics (1)
- Summit (2)
- Sustainable Energy (24)
- Transportation (20)
Media Contacts

Ten scientists from the Department of Energy’s Oak Ridge National Laboratory are among the world’s most highly cited researchers, according to a bibliometric analysis conducted by the scientific publication analytics firm Clarivate.
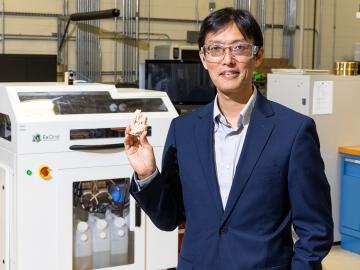
Researchers at ORNL designed a novel polymer to bind and strengthen silica sand for binder jet additive manufacturing, a 3D-printing method used by industries for prototyping and part production.

A research team at Oak Ridge National Laboratory have 3D printed a thermal protection shield, or TPS, for a capsule that will launch with the Cygnus cargo spacecraft as part of the supply mission to the International Space Station.
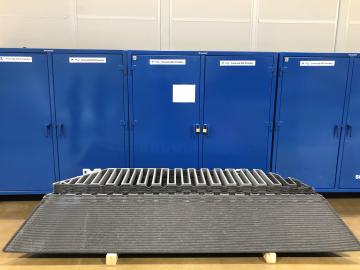
Oak Ridge National Laboratory researchers, in collaboration with Cincinnati Inc., demonstrated the potential for using multimaterials and recycled composites in large-scale applications by 3D printing a mold that replicated a single facet of a
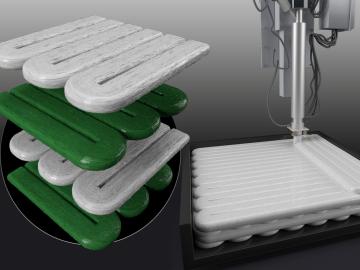
Oak Ridge National Laboratory researchers combined additive manufacturing with conventional compression molding to produce high-performance thermoplastic composites reinforced with short carbon fibers.

Biologists from Oak Ridge National Laboratory and the Smithsonian Environmental Research Center have confirmed that microorganisms called methanogens can transform mercury into the neurotoxin methylmercury with varying efficiency across species.
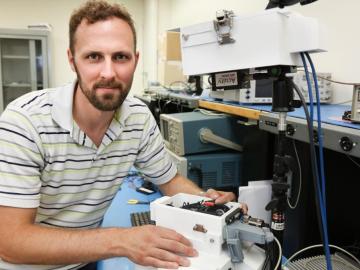
As leader of the RF, Communications, and Cyber-Physical Security Group at Oak Ridge National Laboratory, Kerekes heads an accelerated lab-directed research program to build virtual models of critical infrastructure systems like the power grid that can be used to develop ways to detect and repel cyber-intrusion and to make the network resilient when disruption occurs.
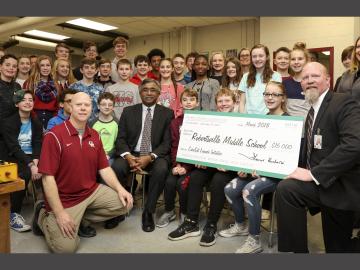
Last November a team of students and educators from Robertsville Middle School in Oak Ridge and scientists from Oak Ridge National Laboratory submitted a proposal to NASA for their Cube Satellite Launch Initiative in hopes of sending a student-designed nanosatellite named RamSat into...
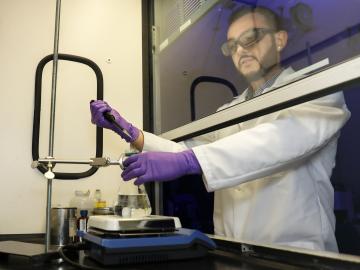
A novel method developed at Oak Ridge National Laboratory creates supertough renewable plastic with improved manufacturability. Working with polylactic acid, a biobased plastic often used in packaging, textiles, biomedical implants and 3D printing, the research team added tiny amo...
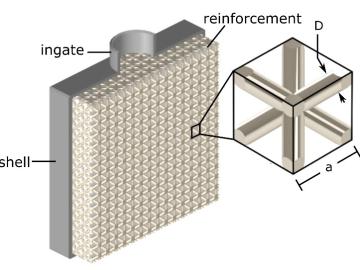
A new manufacturing method created by Oak Ridge National Laboratory and Rice University combines 3D printing with traditional casting to produce damage-tolerant components composed of multiple materials. Composite components made by pouring an aluminum alloy over a printed steel lattice showed an order of magnitude greater damage tolerance than aluminum alone.