
Filter News
Area of Research
- Advanced Manufacturing (3)
- Biology and Environment (23)
- Biology and Soft Matter (1)
- Clean Energy (49)
- Electricity and Smart Grid (1)
- Functional Materials for Energy (1)
- Fusion and Fission (3)
- Materials (15)
- Materials for Computing (2)
- National Security (2)
- Neutron Science (3)
- Nuclear Science and Technology (1)
- Supercomputing (5)
- Transportation Systems (1)
News Topics
- (-) Composites (26)
- (-) Decarbonization (79)
- (-) Element Discovery (1)
- 3-D Printing/Advanced Manufacturing (119)
- Advanced Reactors (34)
- Artificial Intelligence (91)
- Big Data (53)
- Bioenergy (91)
- Biology (98)
- Biomedical (58)
- Biotechnology (22)
- Buildings (57)
- Chemical Sciences (63)
- Clean Water (29)
- Climate Change (99)
- Computer Science (187)
- Coronavirus (46)
- Critical Materials (25)
- Cybersecurity (35)
- Education (4)
- Emergency (2)
- Energy Storage (108)
- Environment (194)
- Exascale Computing (37)
- Fossil Energy (5)
- Frontier (42)
- Fusion (53)
- Grid (62)
- High-Performance Computing (84)
- Hydropower (11)
- Irradiation (3)
- Isotopes (53)
- ITER (7)
- Machine Learning (47)
- Materials (143)
- Materials Science (139)
- Mathematics (7)
- Mercury (12)
- Microelectronics (2)
- Microscopy (51)
- Molten Salt (8)
- Nanotechnology (60)
- National Security (60)
- Net Zero (13)
- Neutron Science (131)
- Nuclear Energy (106)
- Partnerships (43)
- Physics (61)
- Polymers (33)
- Quantum Computing (34)
- Quantum Science (69)
- Renewable Energy (2)
- Security (24)
- Simulation (47)
- Software (1)
- Space Exploration (25)
- Statistics (3)
- Summit (57)
- Sustainable Energy (125)
- Transformational Challenge Reactor (7)
- Transportation (97)
Media Contacts
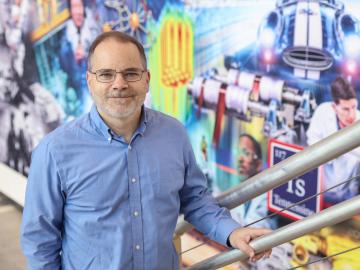
David Sholl has come to the U.S. Department of Energy’s Oak Ridge National Laboratory with a wealth of scientific expertise and a personal mission: hasten the development and deployment of decarbonization solutions for the nation’s energy system.
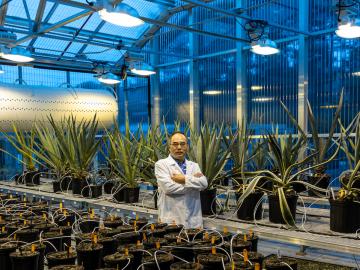
Scientists at ORNL have discovered a single gene that simultaneously boosts plant growth and tolerance for stresses such as drought and salt, all while tackling the root cause of climate change by enabling plants to pull more carbon dioxide from the atmosphere.
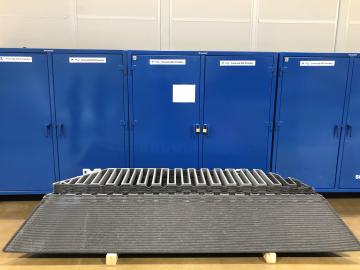
Oak Ridge National Laboratory researchers, in collaboration with Cincinnati Inc., demonstrated the potential for using multimaterials and recycled composites in large-scale applications by 3D printing a mold that replicated a single facet of a
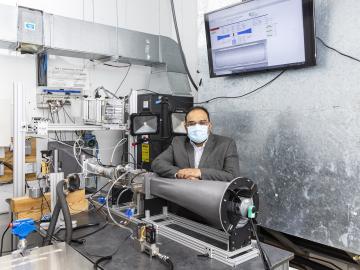
When Kashif Nawaz looks at a satellite map of the U.S., he sees millions of buildings that could hold a potential solution for the capture of carbon dioxide, a plentiful gas that can be harmful when excessive amounts are released into the atmosphere, raising the Earth’s temperature.
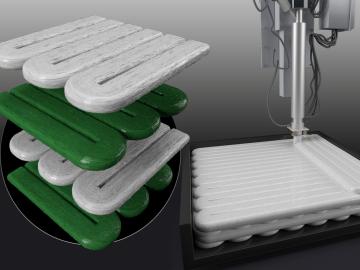
Oak Ridge National Laboratory researchers combined additive manufacturing with conventional compression molding to produce high-performance thermoplastic composites reinforced with short carbon fibers.
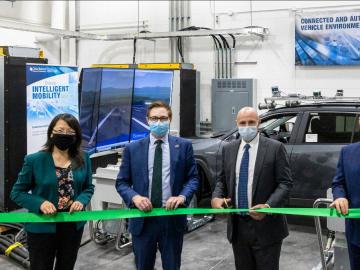
ORNL and Department of Energy officials dedicated the launch of two clean energy research initiatives that focus on the recycling and recovery of advanced manufacturing materials and on connected and
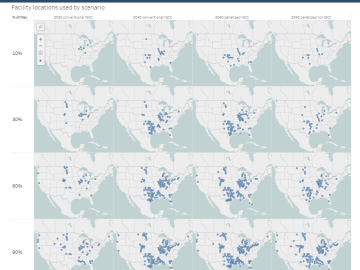
The combination of bioenergy with carbon capture and storage could cost-effectively sequester hundreds of millions of metric tons per year of carbon dioxide in the United States, making it a competitive solution for carbon management, according to a new analysis by ORNL scientists.

ORNL and The University of Toledo have entered into a memorandum of understanding for collaborative research.
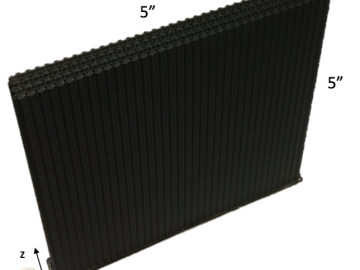
A team including Oak Ridge National Laboratory and University of Tennessee researchers demonstrated a novel 3D printing approach called Z-pinning that can increase the material’s strength and toughness by more than three and a half times compared to conventional additive manufacturing processes.
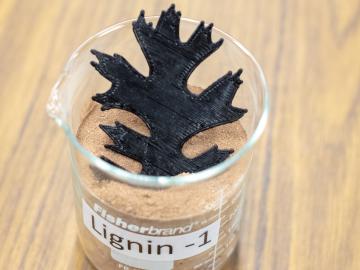
Scientists at the Department of Energy’s Oak Ridge National Laboratory have created a recipe for a renewable 3D printing feedstock that could spur a profitable new use for an intractable biorefinery byproduct: lignin.