Filter News
Area of Research
- (-) Clean Energy (46)
- Advanced Manufacturing (12)
- Biological Systems (1)
- Biology and Environment (31)
- Building Technologies (1)
- Computational Biology (1)
- Fusion and Fission (2)
- Fusion Energy (2)
- Isotopes (11)
- Materials (26)
- Materials for Computing (4)
- National Security (6)
- Neutron Science (5)
- Nuclear Science and Technology (4)
- Quantum information Science (1)
- Supercomputing (9)
News Type
News Topics
- (-) 3-D Printing/Advanced Manufacturing (33)
- (-) Bioenergy (4)
- (-) Biomedical (2)
- (-) Cybersecurity (2)
- (-) Mercury (2)
- (-) Microscopy (3)
- (-) Space Exploration (2)
- (-) Summit (1)
- Artificial Intelligence (1)
- Big Data (2)
- Biology (3)
- Biotechnology (1)
- Buildings (19)
- Chemical Sciences (1)
- Clean Water (5)
- Climate Change (8)
- Composites (9)
- Computer Science (10)
- Coronavirus (6)
- Critical Materials (5)
- Decarbonization (12)
- Energy Storage (32)
- Environment (21)
- Grid (21)
- High-Performance Computing (1)
- Hydropower (2)
- Machine Learning (2)
- Materials (14)
- Materials Science (10)
- Mathematics (2)
- Nanotechnology (1)
- National Security (1)
- Net Zero (2)
- Neutron Science (1)
- Nuclear Energy (1)
- Polymers (5)
- Security (2)
- Simulation (1)
- Statistics (1)
- Sustainable Energy (33)
- Transportation (36)
Media Contacts
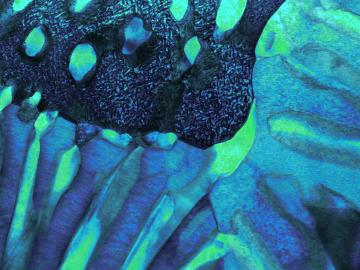
Oak Ridge National Laboratory scientists proved molybdenum titanium carbide, a refractory metal alloy that can withstand extreme temperature environments, can also be crack free and dense when produced with electron beam powder bed fusion.
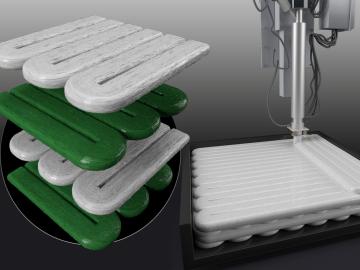
Oak Ridge National Laboratory researchers combined additive manufacturing with conventional compression molding to produce high-performance thermoplastic composites reinforced with short carbon fibers.

A team of Oak Ridge National Laboratory researchers demonstrated that an additively manufactured hot stamping die – a tool used to create car body components – cooled faster than those produced by conventional manufacturing methods.

Oak Ridge National Laboratory researchers have demonstrated that a new class of superalloys made of cobalt and nickel remains crack-free and defect-resistant in extreme heat, making them conducive for use in metal-based 3D printing applications.
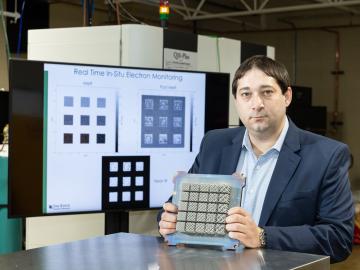
Growing up in the heart of the American automobile industry near Detroit, Oak Ridge National Laboratory materials scientist Mike Kirka was no stranger to manufacturing.
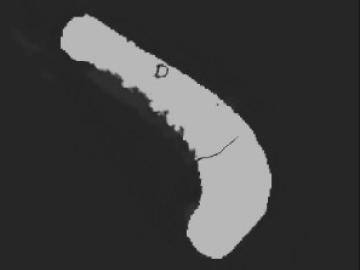
Algorithms developed at Oak Ridge National Laboratory can greatly enhance X-ray computed tomography images of 3D-printed metal parts, resulting in more accurate, faster scans.
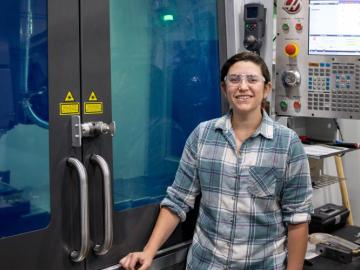
Growing up in Florida, Emma Betters was fascinated by rockets and for good reason. Any time she wanted to see a space shuttle launch from NASA’s nearby Kennedy Space Center, all she had to do was sit on her front porch.
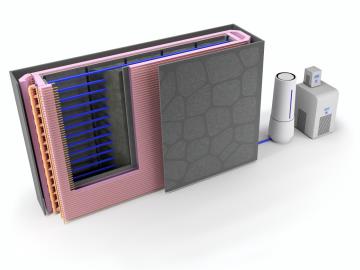
Oak Ridge National Laboratory researchers used additive manufacturing to build a first-of-its kind smart wall called EMPOWER.
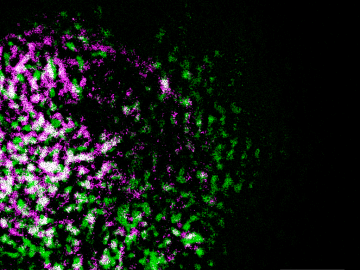
Oak Ridge National Laboratory researchers have built a novel microscope that provides a “chemical lens” for viewing biological systems including cell membranes and biofilms.

Ada Sedova’s journey to Oak Ridge National Laboratory has taken her on the path from pre-med studies in college to an accelerated graduate career in mathematics and biophysics and now to the intersection of computational science and biology