Filter News
Area of Research
- (-) Advanced Manufacturing (14)
- (-) Biology and Environment (18)
- Building Technologies (1)
- Clean Energy (58)
- Computational Engineering (1)
- Computer Science (3)
- Fusion and Fission (4)
- Fusion Energy (1)
- Materials (30)
- Materials for Computing (5)
- National Security (7)
- Neutron Science (5)
- Nuclear Science and Technology (6)
- Quantum information Science (2)
- Supercomputing (20)
News Type
News Topics
- (-) 3-D Printing/Advanced Manufacturing (18)
- (-) Big Data (8)
- (-) Composites (5)
- (-) Microscopy (7)
- Advanced Reactors (1)
- Artificial Intelligence (6)
- Bioenergy (38)
- Biology (56)
- Biomedical (12)
- Biotechnology (8)
- Chemical Sciences (3)
- Clean Water (11)
- Climate Change (33)
- Computer Science (14)
- Coronavirus (6)
- Decarbonization (17)
- Energy Storage (2)
- Environment (75)
- Exascale Computing (4)
- Frontier (3)
- Fusion (1)
- Grid (2)
- High-Performance Computing (15)
- Hydropower (8)
- Machine Learning (6)
- Materials (7)
- Materials Science (7)
- Mathematics (3)
- Mercury (7)
- Nanotechnology (2)
- National Security (2)
- Net Zero (1)
- Neutron Science (3)
- Nuclear Energy (1)
- Physics (1)
- Polymers (1)
- Renewable Energy (1)
- Security (1)
- Simulation (10)
- Space Exploration (1)
- Summit (7)
- Sustainable Energy (28)
- Transportation (1)
Media Contacts
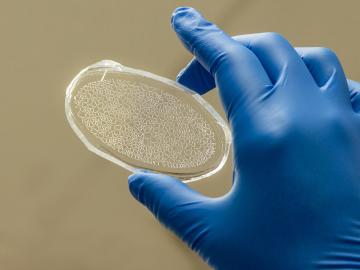
Scientists at ORNL have created a miniaturized environment to study the ecosystem around poplar tree roots for insights into plant health and soil carbon sequestration.

Chemical and environmental engineer Samarthya Bhagia is focused on achieving carbon neutrality and a circular economy by designing new plant-based materials for a range of applications from energy storage devices and sensors to environmentally friendly bioplastics.
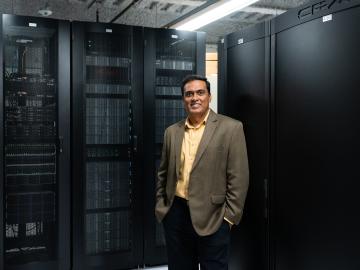
The Atmospheric Radiation Measurement Data Center is shepherding changes to its operations to make the treasure trove of data more easily available accessible and useful to scientists studying Earth’s climate.
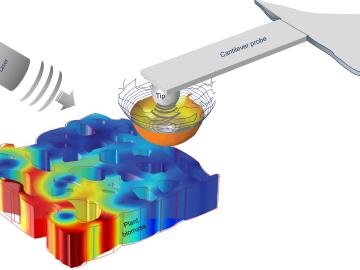
To optimize biomaterials for reliable, cost-effective paper production, building construction, and biofuel development, researchers often study the structure of plant cells using techniques such as freezing plant samples or placing them in a vacuum.
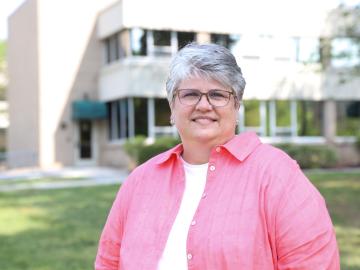
Jennifer Morrell-Falvey’s interest in visualizing the science behind natural processes was what drew her to ORNL in what she expected to be a short stint some 18 years ago.
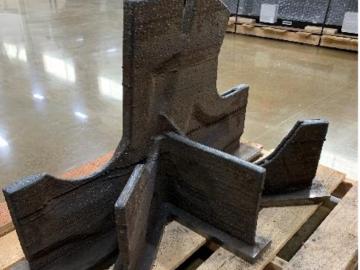
Oak Ridge National Laboratory researchers recently used large-scale additive manufacturing with metal to produce a full-strength steel component for a wind turbine, proving the technique as a viable alternative to
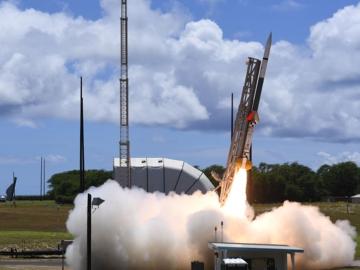
Oak Ridge National Laboratory researchers have developed a novel process to manufacture extreme heat resistant carbon-carbon composites. The performance of these materials will be tested in a U.S. Navy rocket that NASA will launch this fall.

A research team at Oak Ridge National Laboratory have 3D printed a thermal protection shield, or TPS, for a capsule that will launch with the Cygnus cargo spacecraft as part of the supply mission to the International Space Station.
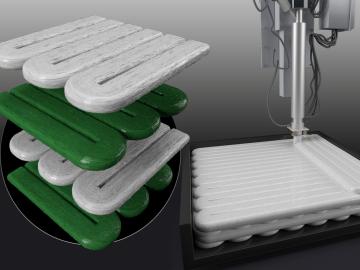
Oak Ridge National Laboratory researchers combined additive manufacturing with conventional compression molding to produce high-performance thermoplastic composites reinforced with short carbon fibers.

A team of Oak Ridge National Laboratory researchers demonstrated that an additively manufactured hot stamping die – a tool used to create car body components – cooled faster than those produced by conventional manufacturing methods.