Filter News
Area of Research
- Advanced Manufacturing (1)
- Biological Systems (1)
- Biology and Environment (26)
- Clean Energy (26)
- Computational Biology (1)
- Computational Engineering (1)
- Computer Science (1)
- Fusion and Fission (10)
- Fusion Energy (1)
- Isotope Development and Production (1)
- Isotopes (23)
- Materials (67)
- Materials Characterization (1)
- Materials for Computing (10)
- Materials Under Extremes (1)
- National Security (7)
- Neutron Science (28)
- Nuclear Science and Technology (11)
- Supercomputing (52)
News Type
News Topics
- (-) Advanced Reactors (17)
- (-) Biomedical (43)
- (-) Frontier (35)
- (-) Isotopes (39)
- (-) Materials Science (88)
- 3-D Printing/Advanced Manufacturing (77)
- Artificial Intelligence (66)
- Big Data (28)
- Bioenergy (72)
- Biology (75)
- Biotechnology (17)
- Buildings (29)
- Chemical Sciences (48)
- Clean Water (15)
- Climate Change (66)
- Composites (14)
- Computer Science (134)
- Coronavirus (34)
- Critical Materials (11)
- Cybersecurity (31)
- Decarbonization (59)
- Education (3)
- Element Discovery (1)
- Emergency (2)
- Energy Storage (68)
- Environment (135)
- Exascale Computing (31)
- Fossil Energy (5)
- Fusion (41)
- Grid (36)
- High-Performance Computing (65)
- Hydropower (5)
- ITER (4)
- Machine Learning (31)
- Materials (97)
- Mathematics (5)
- Mercury (9)
- Microelectronics (2)
- Microscopy (35)
- Molten Salt (3)
- Nanotechnology (42)
- National Security (46)
- Net Zero (10)
- Neutron Science (92)
- Nuclear Energy (75)
- Partnerships (37)
- Physics (49)
- Polymers (19)
- Quantum Computing (24)
- Quantum Science (52)
- Renewable Energy (2)
- Security (21)
- Simulation (34)
- Software (1)
- Space Exploration (14)
- Statistics (1)
- Summit (50)
- Sustainable Energy (71)
- Transformational Challenge Reactor (7)
- Transportation (51)
Media Contacts
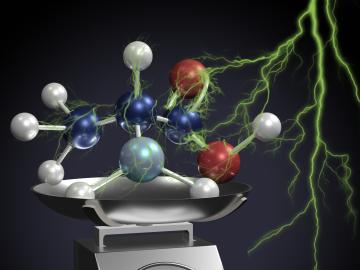
OAK RIDGE, Tenn., Jan. 31, 2019—A new electron microscopy technique that detects the subtle changes in the weight of proteins at the nanoscale—while keeping the sample intact—could open a new pathway for deeper, more comprehensive studies of the basic building blocks of life.
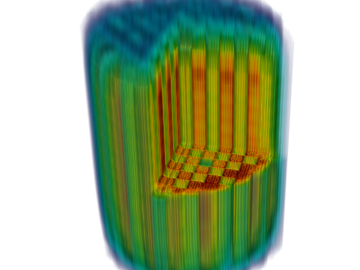
The Department of Energy’s Oak Ridge National Laboratory is collaborating with industry on six new projects focused on advancing commercial nuclear energy technologies that offer potential improvements to current nuclear reactors and move new reactor designs closer to deployment.
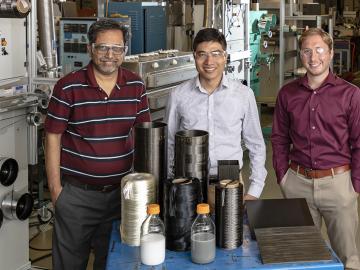
Carbon fiber composites—lightweight and strong—are great structural materials for automobiles, aircraft and other transportation vehicles. They consist of a polymer matrix, such as epoxy, into which reinforcing carbon fibers have been embedded. Because of differences in the mecha...
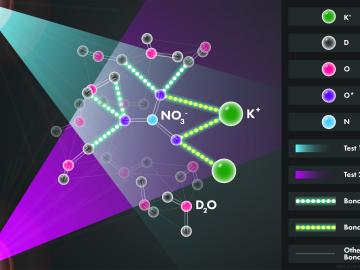
Scientists at the Department of Energy’s Oak Ridge National Laboratory used neutrons, isotopes and simulations to “see” the atomic structure of a saturated solution and found evidence supporting one of two competing hypotheses about how ions come
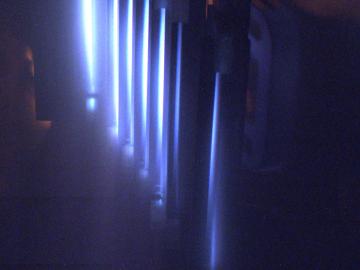
A tiny vial of gray powder produced at the Department of Energy’s Oak Ridge National Laboratory is the backbone of a new experiment to study the intense magnetic fields created in nuclear collisions.
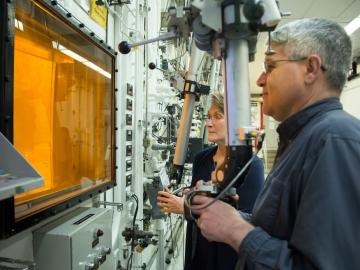
The Department of Energy’s Oak Ridge National Laboratory is now producing actinium-227 (Ac-227) to meet projected demand for a highly effective cancer drug through a 10-year contract between the U.S. DOE Isotope Program and Bayer.
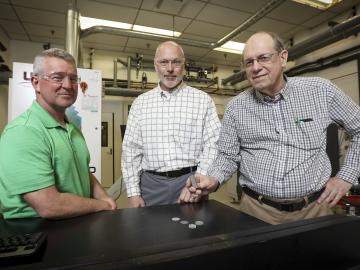
“Made in the USA.” That can now be said of the radioactive isotope molybdenum-99 (Mo-99), last made in the United States in the late 1980s. Its short-lived decay product, technetium-99m (Tc-99m), is the most widely used radioisotope in medical diagnostic imaging. Tc-99m is best known ...
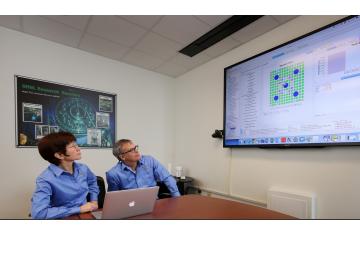
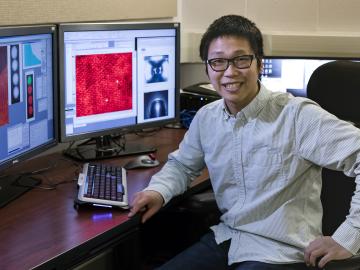
Researchers have long sought electrically conductive materials for economical energy-storage devices. Two-dimensional (2D) ceramics called MXenes are contenders. Unlike most 2D ceramics, MXenes have inherently good conductivity because they are molecular sheets made from the carbides ...
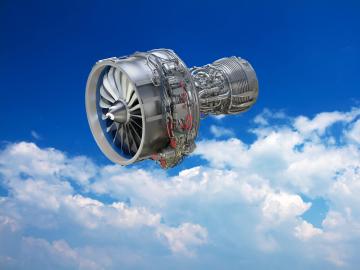
Ceramic matrix composite (CMC) materials are made of coated ceramic fibers surrounded by a ceramic matrix. They are tough, lightweight and capable of withstanding temperatures 300–400 degrees F hotter than metal alloys can endure. If certain components were made with CMCs instead o...