Filter News
Area of Research
News Topics
- (-) 3-D Printing/Advanced Manufacturing (15)
- (-) Clean Water (5)
- (-) Cybersecurity (5)
- (-) Energy Storage (8)
- (-) Frontier (2)
- (-) Isotopes (1)
- (-) Security (2)
- (-) Space Exploration (4)
- Advanced Reactors (7)
- Artificial Intelligence (12)
- Big Data (7)
- Bioenergy (9)
- Biomedical (5)
- Biotechnology (1)
- Composites (2)
- Computer Science (35)
- Environment (19)
- Exascale Computing (2)
- Fusion (5)
- Grid (5)
- Machine Learning (5)
- Materials Science (20)
- Mercury (1)
- Microscopy (5)
- Molten Salt (1)
- Nanotechnology (6)
- Neutron Science (18)
- Nuclear Energy (17)
- Physics (6)
- Polymers (2)
- Quantum Science (10)
- Summit (9)
- Sustainable Energy (8)
- Transportation (12)
Media Contacts
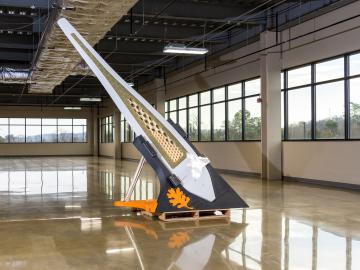
In the shifting landscape of global manufacturing, American ingenuity is once again giving U.S companies an edge with radical productivity improvements as a result of advanced materials and robotic systems developed at the Department of Energy’s Manufacturing Demonstration Facility (MDF) at Oak Ridge National Laboratory.
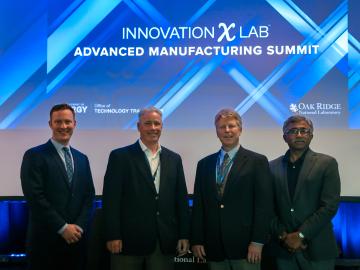
OAK RIDGE, Tenn., May 8, 2019—Oak Ridge National Laboratory and Lincoln Electric (NASDAQ: LECO) announced their continued collaboration on large-scale, robotic additive manufacturing technology at the Department of Energy’s Advanced Manufacturing InnovationXLab Summit.
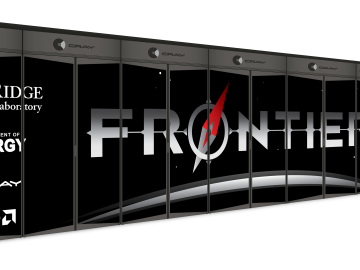
OAK RIDGE, Tenn., May 7, 2019—The U.S. Department of Energy today announced a contract with Cray Inc. to build the Frontier supercomputer at Oak Ridge National Laboratory, which is anticipated to debut in 2021 as the world’s most powerful computer with a performance of greater than 1.5 exaflops.
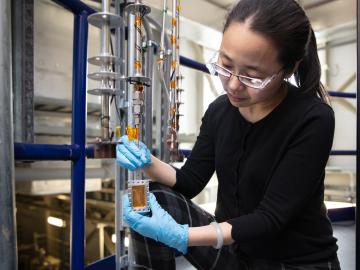
Researchers at the Department of Energy’s Oak Ridge National Laboratory, Pacific Northwest National Laboratory and Washington State University teamed up to investigate the complex dynamics of low-water liquids that challenge nuclear waste processing at federal cleanup sites.
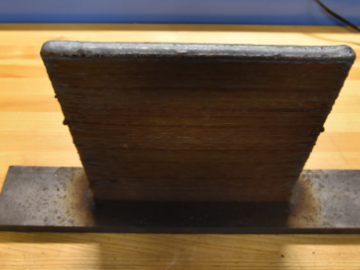
A novel additive manufacturing method developed by researchers at Oak Ridge National Laboratory could be a promising alternative for low-cost, high-quality production of large-scale metal parts with less material waste.
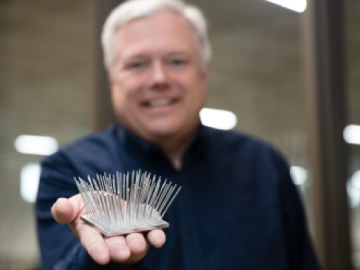
When Scott Smith looks at a machine tool, he thinks not about what the powerful equipment used to shape metal can do – he’s imagining what it could do with the right added parts and strategies. As ORNL’s leader for a newly formed group, Machining and Machine Tool Research, Smith will have the opportunity to do just that.
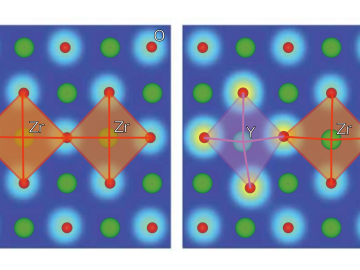
Ionic conduction involves the movement of ions from one location to another inside a material. The ions travel through point defects, which are irregularities in the otherwise consistent arrangement of atoms known as the crystal lattice. This sometimes sluggish process can limit the performance and efficiency of fuel cells, batteries, and other energy storage technologies.
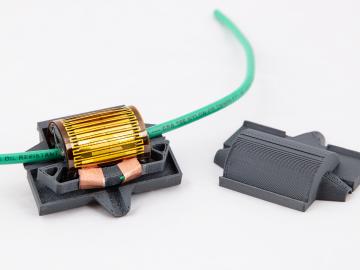
Scientists at Oak Ridge National Laboratory have developed a low-cost, printed, flexible sensor that can wrap around power cables to precisely monitor electrical loads from household appliances to support grid operations.
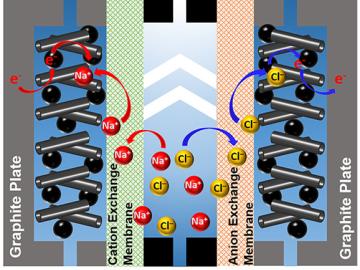
A team of scientists led by Oak Ridge National Laboratory used carbon nanotubes to improve a desalination process that attracts and removes ionic compounds such as salt from water using charged electrodes.
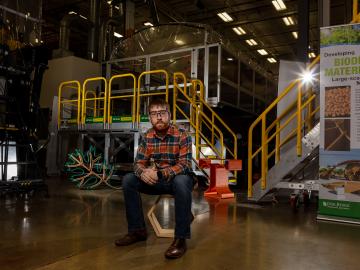
Alex Roschli is no stranger to finding himself in unique situations. After all, the early career researcher in ORNL’s Manufacturing Systems Research group bears a last name that only 29 other people share in the United States, and he’s certain he’s the only Roschli (a moniker that hails from Switzerland) with the first name Alex.