Filter Results
Related Organization
- Biological and Environmental Systems Science Directorate (29)
- Computing and Computational Sciences Directorate (39)
- Energy Science and Technology Directorate (229)
- Fusion and Fission Energy and Science Directorate
(24)
- Information Technology Services Directorate (3)
- National Security Sciences Directorate (20)
- Neutron Sciences Directorate (11)
- Physical Sciences Directorate (138)
- User Facilities (28)
- (-) Isotope Science and Enrichment Directorate (7)
Researcher
- Eddie Lopez Honorato
- Mike Zach
- Ryan Heldt
- Tyler Gerczak
- Alexander I Kolesnikov
- Alexei P Sokolov
- Andrew F May
- Annetta Burger
- Bekki Mills
- Ben Garrison
- Brad Johnson
- Bruce Moyer
- Carter Christopher
- Chance C Brown
- Charlie Cook
- Christopher Hershey
- Christopher Hobbs
- Craig Blue
- Daniel Rasmussen
- Debjani Pal
- Debraj De
- Gautam Malviya Thakur
- Hsin Wang
- James Gaboardi
- James Klett
- Jeffrey Einkauf
- Jennifer M Pyles
- Jesse McGaha
- John Lindahl
- John Wenzel
- Justin Griswold
- Keju An
- Kevin Sparks
- Kuntal De
- Laetitia H Delmau
- Liz McBride
- Luke Sadergaski
- Mark Loguillo
- Matthew B Stone
- Matt Kurley III
- Nedim Cinbiz
- Padhraic L Mulligan
- Rodney D Hunt
- Sandra Davern
- Shannon M Mahurin
- Tao Hong
- Todd Thomas
- Tomonori Saito
- Tony Beard
- Victor Fanelli
- Xiuling Nie
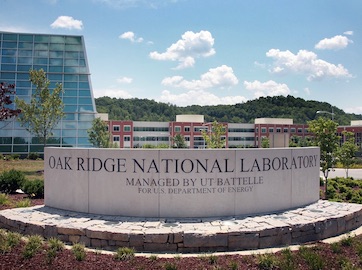
Often there are major challenges in developing diverse and complex human mobility metrics systematically and quickly.
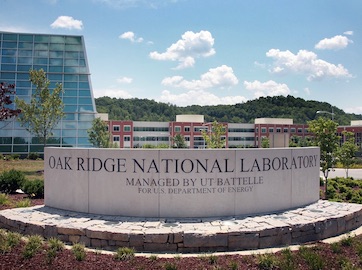
Ruthenium is recovered from used nuclear fuel in an oxidizing environment by depositing the volatile RuO4 species onto a polymeric substrate.
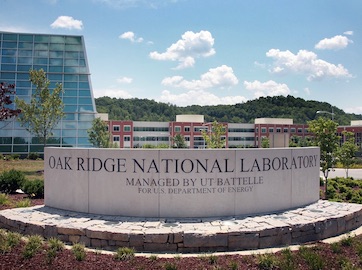
Sintering additives to improve densification and microstructure control of UN provides a facile approach to producing high quality nuclear fuels.
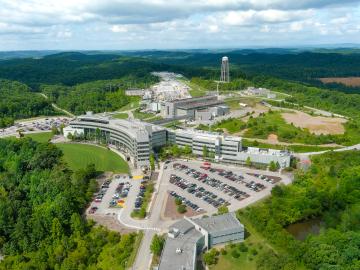
Neutron scattering experiments cover a large temperature range in which experimenters want to test their samples.
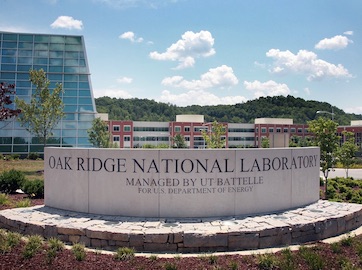
The technologies provide a system and method of needling of veiled AS4 fabric tape.

Neutron beams are used around the world to study materials for various purposes.
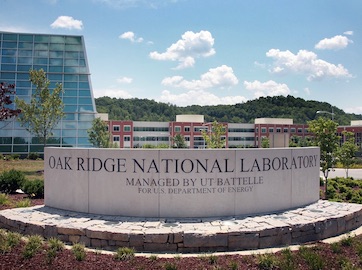
In order to avoid the limitations and costs due to the use of monolithic components for chemical vapor deposition, we developed a modular system in which the reaction chamber can be composed of a top and bottom cone, nozzle, and in-situ reaction chambers.
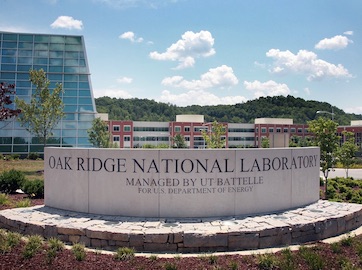
Spherical powders applied to nuclear targetry for isotope production will allow for enhanced heat transfer properties, tailored thermal conductivity and minimize time required for target fabrication and post processing.