Filter Results
Related Organization
- Biological and Environmental Systems Science Directorate (29)
- Computing and Computational Sciences Directorate (39)
- Energy Science and Technology Directorate (229)
- Fusion and Fission Energy and Science Directorate
(24)
- Information Technology Services Directorate (3)
- Isotope Science and Enrichment Directorate (7)
- National Security Sciences Directorate (20)
- Neutron Sciences Directorate (11)
- Physical Sciences Directorate (138)
- User Facilities (28)
Researcher
- Chris Tyler
- Justin West
- Ritin Mathews
- David Olvera Trejo
- Eddie Lopez Honorato
- J.R. R Matheson
- Jaydeep Karandikar
- Ryan Heldt
- Scott Smith
- Tyler Gerczak
- Akash Jag Prasad
- Alexander I Kolesnikov
- Alexei P Sokolov
- Bekki Mills
- Brian Gibson
- Brian Post
- Calen Kimmell
- Callie Goetz
- Christopher Hobbs
- Emma Betters
- Fred List III
- Greg Corson
- Jesse Heineman
- John Potter
- John Wenzel
- Josh B Harbin
- Keith Carver
- Keju An
- Mark Loguillo
- Matthew B Stone
- Matt Kurley III
- Richard Howard
- Rodney D Hunt
- Shannon M Mahurin
- Tao Hong
- Thomas Butcher
- Tomonori Saito
- Tony L Schmitz
- Victor Fanelli
- Vladimir Orlyanchik
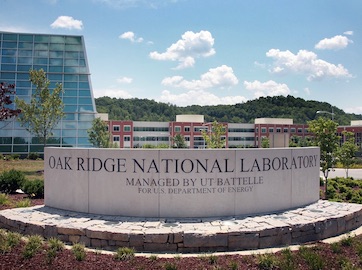
System and method for part porosity monitoring of additively manufactured components using machining
In additive manufacturing, choice of process parameters for a given material and geometry can result in porosities in the build volume, which can result in scrap.
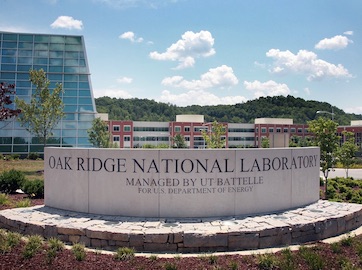
A pressure burst feature has been designed and demonstrated for relieving potentially hazardous excess pressure within irradiation capsules used in the ORNL High Flux Isotope Reactor (HFIR).
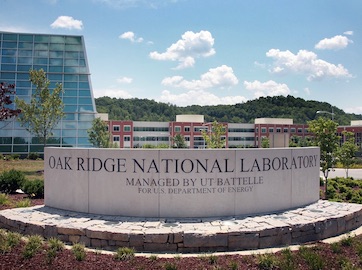
Distortion generated during additive manufacturing of metallic components affect the build as well as the baseplate geometries. These distortions are significant enough to disqualify components for functional purposes.
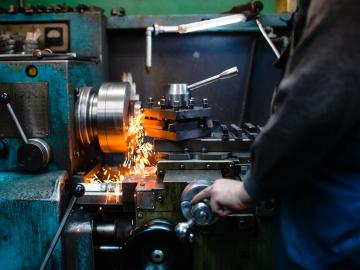
For additive manufacturing of large-scale parts, significant distortion can result from residual stresses during deposition and cooling. This can result in part scraps if the final part geometry is not contained in the additively manufactured preform.
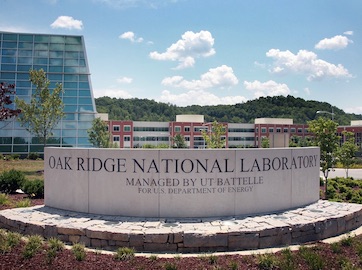
Sintering additives to improve densification and microstructure control of UN provides a facile approach to producing high quality nuclear fuels.
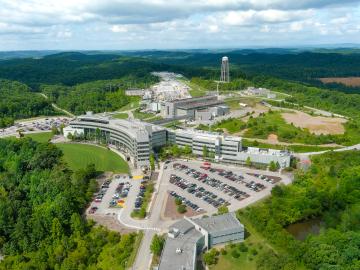
Neutron scattering experiments cover a large temperature range in which experimenters want to test their samples.
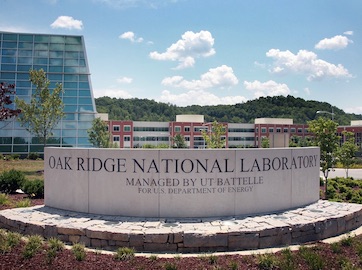
In additive manufacturing large stresses are induced in the build plate and part interface. A result of these stresses are deformations in the build plate and final component.
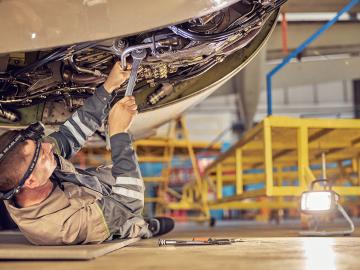
Materials produced via additive manufacturing, or 3D printing, can experience significant residual stress, distortion and cracking, negatively impacting the manufacturing process.

Neutron beams are used around the world to study materials for various purposes.