Filter Results
Related Organization
- Biological and Environmental Systems Science Directorate (29)
- Computing and Computational Sciences Directorate (39)
- Energy Science and Technology Directorate (229)
- Fusion and Fission Energy and Science Directorate (24)
- Information Technology Services Directorate (3)
- Isotope Science and Enrichment Directorate (7)
- National Security Sciences Directorate (20)
- Neutron Sciences Directorate (11)
- Physical Sciences Directorate (138)
- User Facilities (28)
Researcher
- Ryan Dehoff
- Venugopal K Varma
- Mahabir Bhandari
- Michael Kirka
- Vincent Paquit
- Ying Yang
- Adam Aaron
- Adam Stevens
- Ahmed Hassen
- Alexander I Kolesnikov
- Alex Plotkowski
- Alice Perrin
- Amir K Ziabari
- Amit Shyam
- Andres Marquez Rossy
- Bekki Mills
- Blane Fillingim
- Brian Post
- Charles D Ottinger
- Christopher Ledford
- Clay Leach
- David Nuttall
- Govindarajan Muralidharan
- James Haley
- John Wenzel
- Mark Loguillo
- Matthew B Stone
- Patxi Fernandez-Zelaia
- Peeyush Nandwana
- Philip Bingham
- Rangasayee Kannan
- Roger G Miller
- Rose Montgomery
- Sarah Graham
- Sergey Smolentsev
- Steven J Zinkle
- Sudarsanam Babu
- Thomas R Muth
- Venkatakrishnan Singanallur Vaidyanathan
- Victor Fanelli
- Vipin Kumar
- Vlastimil Kunc
- William Peter
- Yan-Ru Lin
- Yanli Wang
- Yukinori Yamamoto
- Yutai Kato
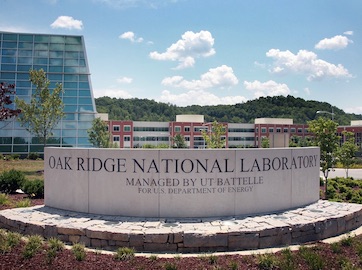
V-Cr-Ti alloys have been proposed as candidate structural materials in fusion reactor blanket concepts with operation temperatures greater than that for reduced activation ferritic martensitic steels (RAFMs).
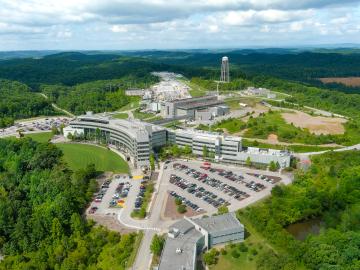
Neutron scattering experiments cover a large temperature range in which experimenters want to test their samples.
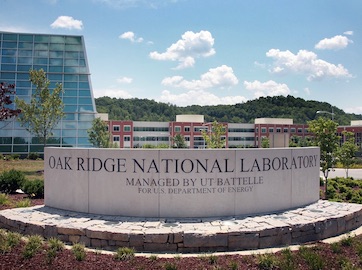
Fusion reactors need efficient systems to create tritium fuel and handle intense heat and radiation. Traditional liquid metal systems face challenges like high pressure losses and material breakdown in strong magnetic fields.

Neutron beams are used around the world to study materials for various purposes.
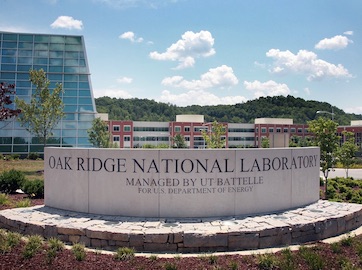
The traditional window installation process involves many steps. These are becoming even more complex with newer construction requirements such as installation of windows over exterior continuous insulation walls.

High strength, oxidation resistant refractory alloys are difficult to fabricate for commercial use in extreme environments.

In manufacturing parts for industry using traditional molds and dies, about 70 percent to 80 percent of the time it takes to create a part is a result of a relatively slow cooling process.
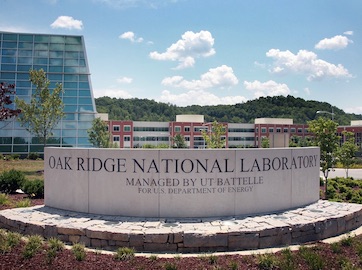
This technology combines 3D printing and compression molding to produce high-strength, low-porosity composite articles.